filmov
tv
Holding Thin Workpieces: Vacuum, Superglue, and More!
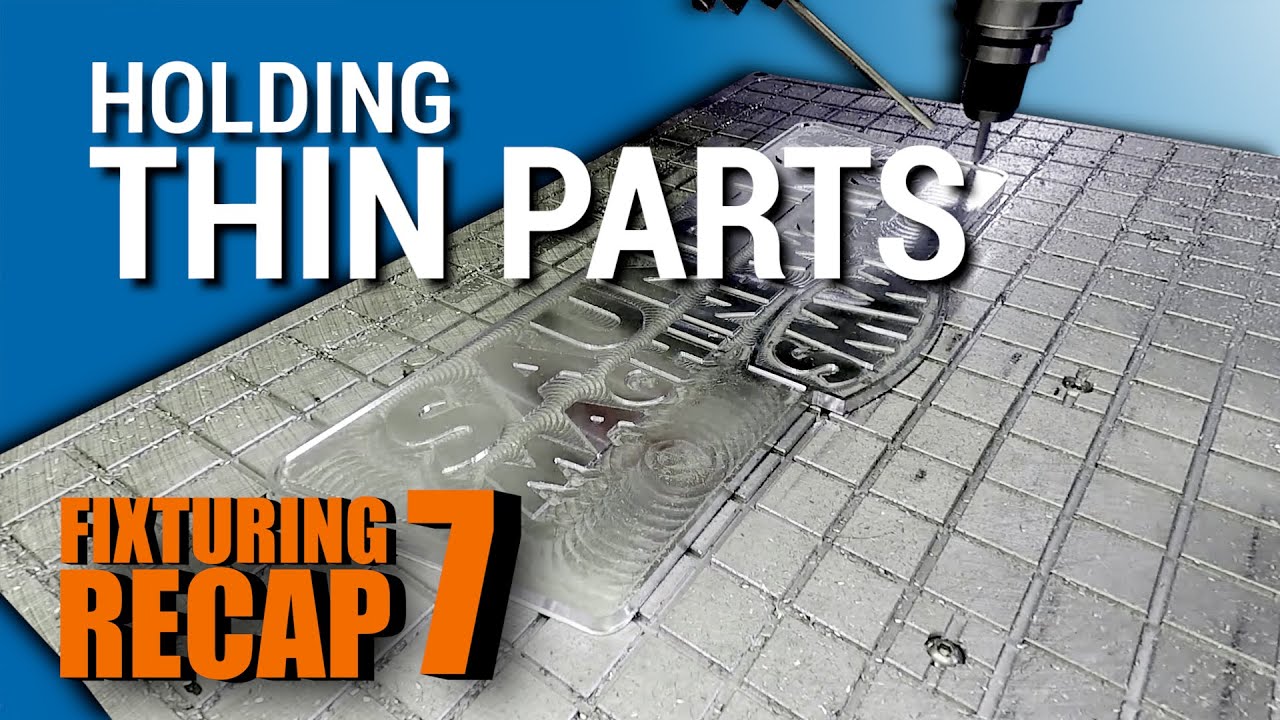
Показать описание
CNC Machining Workholding strategies for thin material and parts! Thin parts will often flex if clamped in a traditional vise, so we need to use other methods such as clamping to a fixture plate, vacuum workholding, or superglue.
00:00 Intro & Using Vacuum Workholding for a Sign Front: Sandpaper, Sharpies, & Calculating Workholding Forces
02:16 Machining Multiple Parts: Vacuum Workholding Tips
03:53 Hybrid Op 2 Fixture & Vacuum Workholding
04:18 CNC Machining Macor: High Volume Parts
05:18 Decking A Vacuum Chuck
05:40 Datron NEO's VacuCard
06:48 Super Glue Workholding for Large, Thin Parts
07:36 Custom Part: Strap Clamps + Fixture Plate
08:02 Final Thoughts
~~~~~~~~~~~~~~~~~~~~~~~~~~~~
Links for this video
Powder Coated Sign! WW136
Machining Thin Parts! Part 1 WW138
Machining Thin Parts! Part 2 WW139
Machining Macor on the Tormach 440! WW170
DATRON Neo: Our Thoughts after 6 months with this amazing CNC machine!
Building Johnny 5 Part 7: Cradle Base & Lower Torso | WW260
Manufacturing At Home: Machining Large Aluminum Plate with Tormach PCNC 1100
~~~~~~~~~~~~~~~~~~~~~~~~~~~~
Reach us / CNC Info:
00:00 Intro & Using Vacuum Workholding for a Sign Front: Sandpaper, Sharpies, & Calculating Workholding Forces
02:16 Machining Multiple Parts: Vacuum Workholding Tips
03:53 Hybrid Op 2 Fixture & Vacuum Workholding
04:18 CNC Machining Macor: High Volume Parts
05:18 Decking A Vacuum Chuck
05:40 Datron NEO's VacuCard
06:48 Super Glue Workholding for Large, Thin Parts
07:36 Custom Part: Strap Clamps + Fixture Plate
08:02 Final Thoughts
~~~~~~~~~~~~~~~~~~~~~~~~~~~~
Links for this video
Powder Coated Sign! WW136
Machining Thin Parts! Part 1 WW138
Machining Thin Parts! Part 2 WW139
Machining Macor on the Tormach 440! WW170
DATRON Neo: Our Thoughts after 6 months with this amazing CNC machine!
Building Johnny 5 Part 7: Cradle Base & Lower Torso | WW260
Manufacturing At Home: Machining Large Aluminum Plate with Tormach PCNC 1100
~~~~~~~~~~~~~~~~~~~~~~~~~~~~
Reach us / CNC Info:
Комментарии