filmov
tv
Hold Multiple Parts With NO CLAMPS! | Fixture Friday 16 | Pierson Workholding
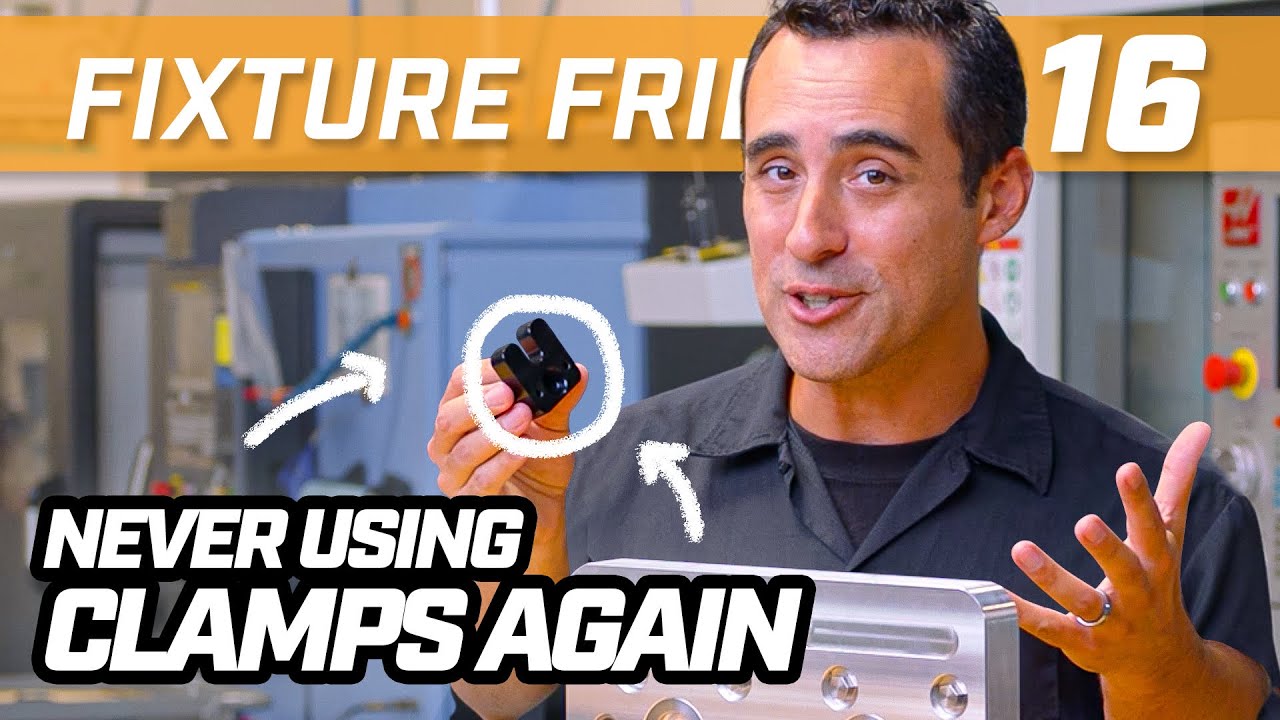
Показать описание
On this week's Pierson Workholding Fixture Friday, Jay looks at how to hold multiple parts with no clamps at all!
With the part we machined in this episode, if you look at it closely, it would require five setups using traditional vise workholding. But in this week's Fixture Friday, we look at how we palletized the second operation to get eight parts per cycle without using a single clamp. Let's get started!
Follow Pierson Workholding!
---------------------------------------------------------
**Videos We Recommend**
Fixture Friday Series:
THIS is the playlist to watch if you want to learn about designing fixtures.
The Move Series:
How we moved into our new shop!
00:00 Eight parts per cycle no clamps
00:35 Downside of 5-axis machining
02:15 Bolt-through pallet design
07:18 Outro
#FixtureFriday #Workholding #ProPalletSystem
With the part we machined in this episode, if you look at it closely, it would require five setups using traditional vise workholding. But in this week's Fixture Friday, we look at how we palletized the second operation to get eight parts per cycle without using a single clamp. Let's get started!
Follow Pierson Workholding!
---------------------------------------------------------
**Videos We Recommend**
Fixture Friday Series:
THIS is the playlist to watch if you want to learn about designing fixtures.
The Move Series:
How we moved into our new shop!
00:00 Eight parts per cycle no clamps
00:35 Downside of 5-axis machining
02:15 Bolt-through pallet design
07:18 Outro
#FixtureFriday #Workholding #ProPalletSystem
Hold Multiple Parts With NO CLAMPS! | Fixture Friday 16 | Pierson Workholding
Machinist's Minute: No movement clamping for unsupported parts
2 Liter Bottle Compressor (No Moving Parts)
'I'm Not Joe Biden' - What VP Kamala Harris Would Change If Elected President
Human Body PARTS We NO LONGER Need!😲
No Longer Available Car Parts
Ford with NO START issues - SOLVED for $20 All Parts needed listed below the video
How to learn major parts of the brain quickly
No Bad Parts: Unblending From Protectors in IFS Therapy
When You Have Too Many Car Parts and No Space...
Truth about Chinese chainsaws, NO Parts?
How To Farm Ship Parts For FREE!! No Man's Sky Orbital Update
Richard Schwartz: No Bad Parts
divide no in two parts# shorts video# trending
How to build AMAZING SharePoint custom web parts - NO CODE REQUIRED!
The worst iPod to collect! No parts available!!! #apple #angry!
Easiest Method Yet to Make Parts Boxes. NO 3D Printer or CNC Required
I Did 19 different parts in 2 weeks| you know what!!No tool break-Saving for next Job-Customer paid
3 really difficult parts of being a therapist that you have no idea about
'No Bad Parts' Chapter 1.1: We're All Multiple - Richard Schwartz
This is a one parter, no second parts. #commentary #booktok #shorts #sixofcrows
Hurricane Helene death toll nears 200, deadliest since Katrina
I thought I would have to do different parts but no I did it all in one video yay
Miss Circle doing your dares PT2 (there are no more parts) #fpe #fundamentalpapereducation
Комментарии