filmov
tv
Understanding Pottery Chapter 20 Pottery Myths, Errors and Misconceptions Part 1
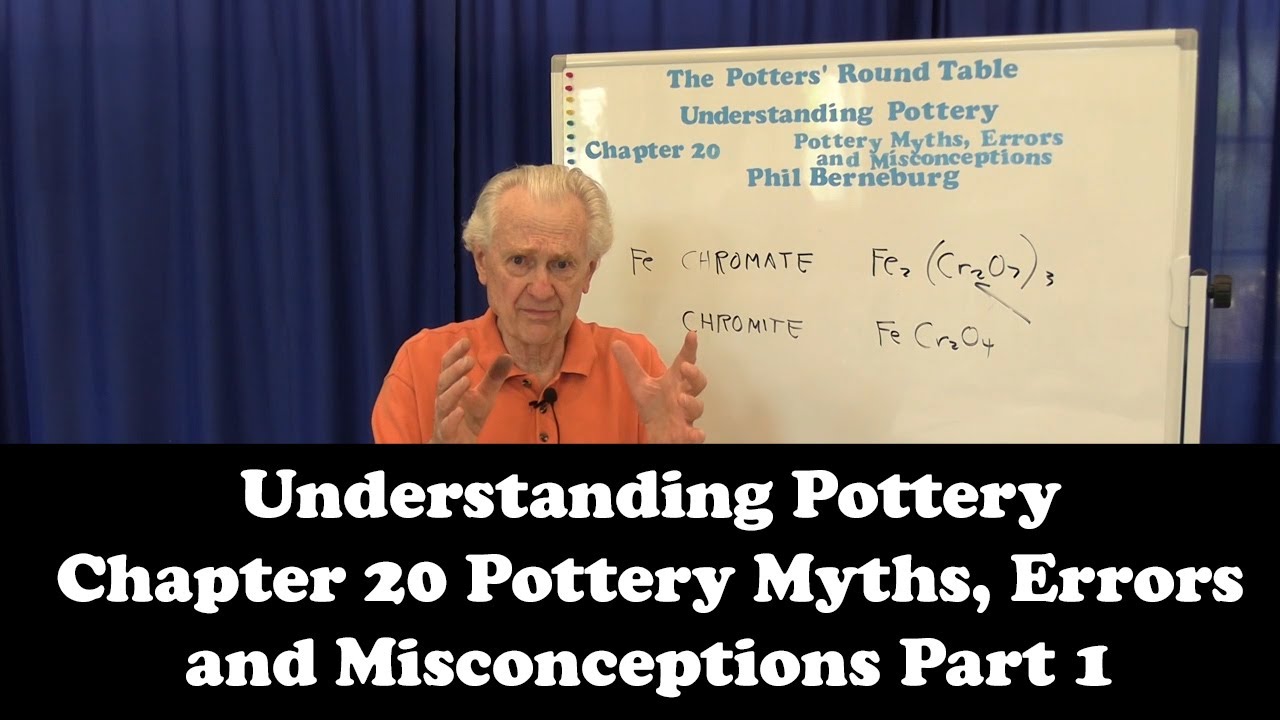
Показать описание
Welcome to Understanding Pottery, Chapter 20: Pottery Myths, Errors and Misconceptions Part 1.
Many terms and theories have surfaced over the years in the field of ceramics, many with no basis in science or physics. We are going to explore many pottery related myths, errors and misconceptions over the next few episodes.
The next topic in the series is Pottery Myths, Errors and Misconceptions Part 2.
Understanding Pottery is a series in production by Washington Street Studios. The video series is a digital textbook that will take you through the entire ceramic process from the raw material through the finished ceramic pieces. There are five sections and twenty-six chapters planned in the series and they are:
Section I: The Pottery Making Sequence
Chapter 1: What is Clay?
Chapter 2: Clay Properties and Drying
Chapter 3: Bisque Firing
Chapter 4: Tips for Successful Glazing
Chapter 5: Pyrometric Cones
Chapter 6: Glaze Firing
Section II: Use of Raw Materials
Chapter 7: Chemistry for Potters
Chapter 8: Glaze Chemistry
Chapter 9: Oxides, Washes, Underglazes and Stains
Chapter 10: Geology for Potters
Chapter 11: Use of Local Materials
Section III: Kilns and Firings
Chapter 12: Atmospheric Firings
Chapter 13: Wood-Fired Kilns
Chapter 14: Gas-Fired Kilns
Chapter 15: Electric Kilns
Chapter 16: Raku Kilns
Section IV: Solving Problems
Chapter 17: Kiln Performance Problems
Chapter 18: Clay Body Defects
Chapter 19: Glaze Defects
Section V: Practical Applications
Chapter 20: Pottery Myths, Errors and Misconceptions
Chapter 21: Thixotropy, Quartz Inversions and Other Pottery Mysteries
Chapter 22: Pottery and Physics
Chapter 23: Pottery Figurin’ (Math)
Chapter 24: Personal Safety with Pottery
Chapter 25: Critiquing Your Own Pottery: Design Principles You Can Use
Chapter 26: Tips for Buying Used Pottery Equipment
At Washington Street Studios, we believe the sharing of creative energy and knowledge will improve the quality of our art and increase the appreciation of art within our community. We are striving to create an environment where the arts are shared and appreciated. We want to grow as a family of artists and contribute to our community. This podcast is one of our steps to share our passion for the ceramic arts, creative energy and knowledge with other artists and art lovers.
We also created an audio version to expand our audience. If you are looking for the podcast of our show search for the ‘The Potters Round Table’ on your podcast platform of choice.
Many terms and theories have surfaced over the years in the field of ceramics, many with no basis in science or physics. We are going to explore many pottery related myths, errors and misconceptions over the next few episodes.
The next topic in the series is Pottery Myths, Errors and Misconceptions Part 2.
Understanding Pottery is a series in production by Washington Street Studios. The video series is a digital textbook that will take you through the entire ceramic process from the raw material through the finished ceramic pieces. There are five sections and twenty-six chapters planned in the series and they are:
Section I: The Pottery Making Sequence
Chapter 1: What is Clay?
Chapter 2: Clay Properties and Drying
Chapter 3: Bisque Firing
Chapter 4: Tips for Successful Glazing
Chapter 5: Pyrometric Cones
Chapter 6: Glaze Firing
Section II: Use of Raw Materials
Chapter 7: Chemistry for Potters
Chapter 8: Glaze Chemistry
Chapter 9: Oxides, Washes, Underglazes and Stains
Chapter 10: Geology for Potters
Chapter 11: Use of Local Materials
Section III: Kilns and Firings
Chapter 12: Atmospheric Firings
Chapter 13: Wood-Fired Kilns
Chapter 14: Gas-Fired Kilns
Chapter 15: Electric Kilns
Chapter 16: Raku Kilns
Section IV: Solving Problems
Chapter 17: Kiln Performance Problems
Chapter 18: Clay Body Defects
Chapter 19: Glaze Defects
Section V: Practical Applications
Chapter 20: Pottery Myths, Errors and Misconceptions
Chapter 21: Thixotropy, Quartz Inversions and Other Pottery Mysteries
Chapter 22: Pottery and Physics
Chapter 23: Pottery Figurin’ (Math)
Chapter 24: Personal Safety with Pottery
Chapter 25: Critiquing Your Own Pottery: Design Principles You Can Use
Chapter 26: Tips for Buying Used Pottery Equipment
At Washington Street Studios, we believe the sharing of creative energy and knowledge will improve the quality of our art and increase the appreciation of art within our community. We are striving to create an environment where the arts are shared and appreciated. We want to grow as a family of artists and contribute to our community. This podcast is one of our steps to share our passion for the ceramic arts, creative energy and knowledge with other artists and art lovers.
We also created an audio version to expand our audience. If you are looking for the podcast of our show search for the ‘The Potters Round Table’ on your podcast platform of choice.
Комментарии