filmov
tv
Professional Luthier Reacts: Taylor Guitar Factory Tour
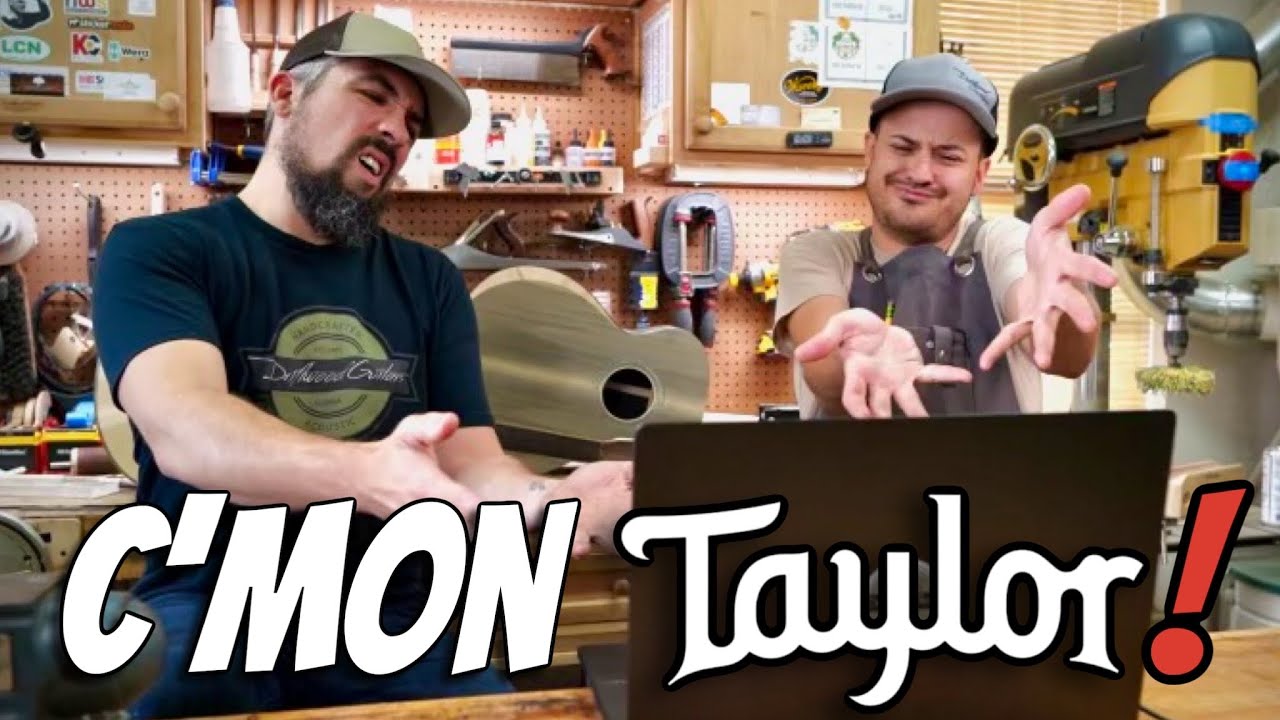
Показать описание
Want to help us make more content? Please consider becoming a member of our channel! It really helps us out. If this video helped you, we’re glad to hear it! You can also say thanks with a super thanks!
Chris and Matt sit down and watch a tour of Taylor Guitars' American factory.
For more information on Chris and his guitars, go to:
Chris and Matt sit down and watch a tour of Taylor Guitars' American factory.
For more information on Chris and his guitars, go to:
Professional Luthier Reacts: Taylor Guitar Factory Tour
Professional Luthier Reacts to Mean Comments
Professional Luthier Reacts: Breedlove Guitar Factory Tour
Professional Luthier Reacts: Ibanez Guitar Factory Tour
#Kingfish playing a 1989 #Fender #Stratocaster #NormansRareGuitars! 🔥 #throwback #2019 #straturday...
When you buy the guitar of your dreams but forget to buy an amp.
Humbled During Acoustic Guitar Practice #shorts
ONE SONG... 5 KILLER TAYLOR GUITARS!
Taylor Guitars TOP DEALER TOUR Tobias Music
Herman Li Breaks Guitar Onstage
Check your action #shorts
Bob Taylor of Taylor Guitars talks about the state of guitar woods across the planet
Driftwood Guitars brings in some help to start a new line of guitars.
Kirk Hammett On His 1959 Les Paul “Greeny” #guitar #kirkhammett #metallica #shorts
Guitar Tech REACTS - Q&A #10 | Guitar Tech Tips | Ep. 92 | Thomann
What no one will tell you about acoustic guitar soundboards!
$1 vs $1,000 guitar 🎸
Tell Me Yours & I'll Tell You Mine; Stories About Mistakes In My Career and How I Fixed The...
How To Make $60 An Hour As a Guitar Tech/Starting Luthier!
Earth 8: Taylor Guitars making instruments from urban lumber
POV: You Buy Your First CLASSICAL GUITAR ‼️
Very smart person changes Guitar strings
Is This $25,000 Guitar Ruined?
Turning an ACOUSTIC guitar into an ELECTRIC guitar?
Комментарии