filmov
tv
Running Pipe Under a 24ft Driveway
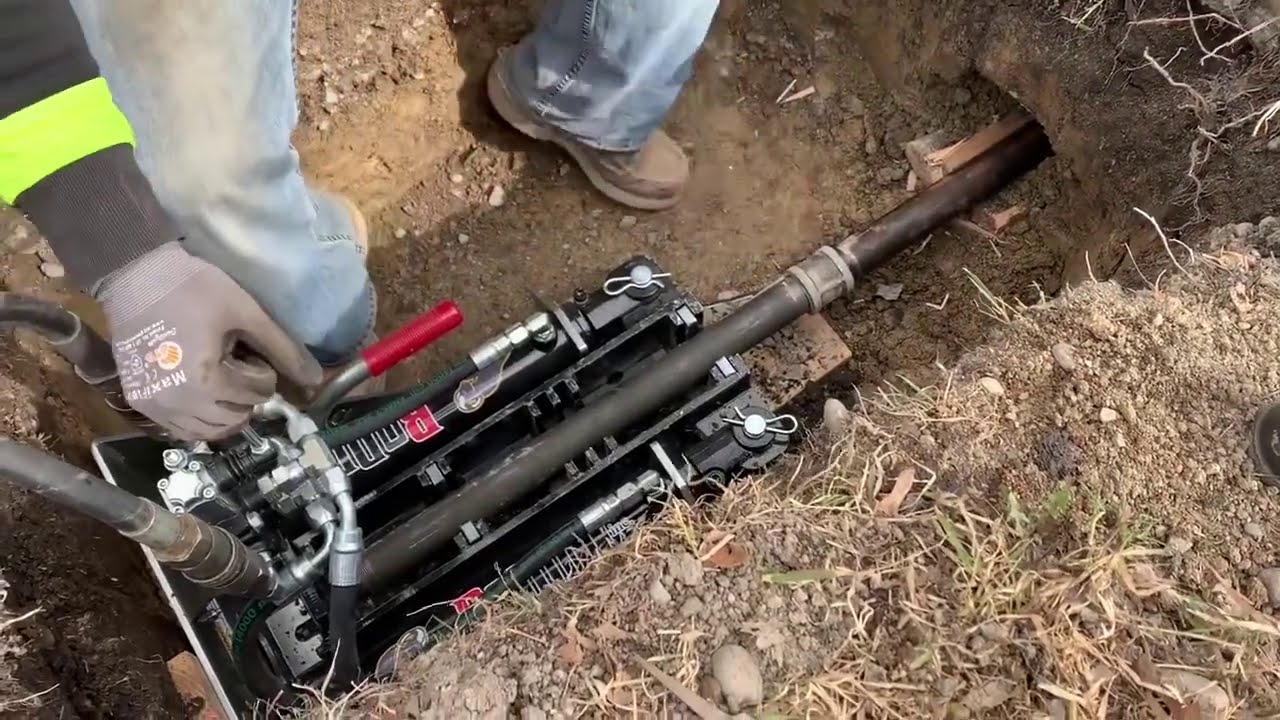
Показать описание
Installing new pipe under a 24ft driveway in a residential neighborhood using the Roddie Inc. Pipe Ram Directional Drill.
Running Pipe Under a 24ft Driveway
Bullet Mole Sidewalk Kit
Running pipe under a sidewalk - Part 2 // Shorts
Jetting a pipe under a 16' driveway
QUICK TIP | How to run electrical under a sidewalk
How To Easily Fish Wires Under Concrete Sidewalk
LONGEST PIPE runs under DRIVEWAY😱 #fyp #shorts #entertainment #rickythewaterboy #work #foryou
Tool to Install Pipe or Conduit Under Sidewalks Using Bullet Mole Sidewalk Kit
Horizontal directional drilling | pipe line installation 🤯 #technology #construction #shorts
Saniflo How the Upflush System Works
The #1 DWV Plumbing Mistake (and how to prevent it).
How Do I Run a Drainage Pipe Under a Driveway?
Running water pipe/irrigation underneath concrete driveway
Does French Drain Work with Fabric? Watch This Before You Install - PVC / Corrugated Pipe
No pit underground pipe installation- Good tools and machinery make work easy
Pulling a tire to clean a pipe
Pipe pulling construction # directional drilling
Protect Pipes From Freezing With Pipe Heating Cable & Waterproof Insulation
underground 20 mm earth piping work #construction #piping #electrical #civilengineering
Bending Metal Conduit! #shorts
Pontoon Boat hits big rock
Did You Know? Trenchless Pipe Installation #shorts
pipe under road drilling process process
You can save thousands on sewer trenchless pipe burst. Just ask how
Комментарии