filmov
tv
Creating sloppy parts to ensure perfect fit - 3D design for 3D printing
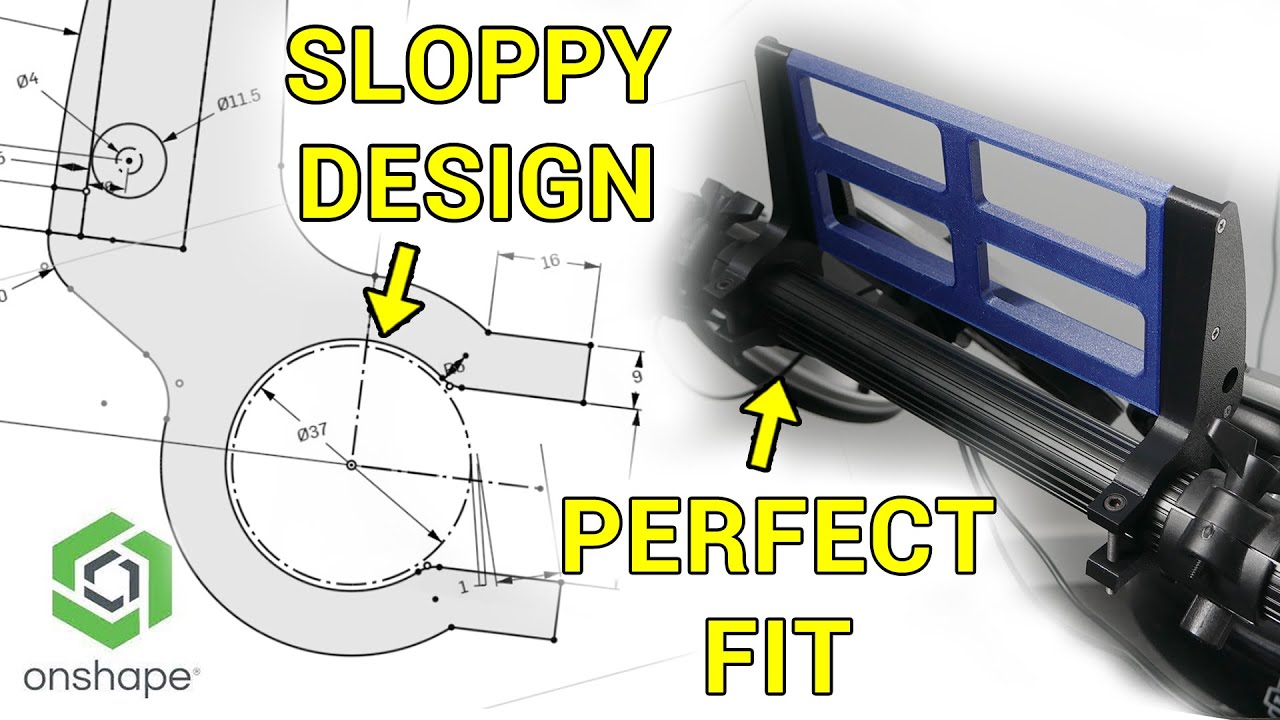
Показать описание
To get the best out of 3D printing, it helps if you can design your own parts. In this tutorial series, we will learn to use a free 3D CAD program to do just that.
In this episode, I demonstrate two projects with geometry that needs to be spot on. Rather than design and print over and over until the fit is perfect, I demonstrate purposely creating pas with too much clearance that can be bolted into the perfect place once in position.
0:00 Introduction
0:43 Scenario 1: Tablet holder
4:49 Scenario 2: Electronic door controller
11:06 Conclusion
Get Quality Resins from 3D Printers Online. 5% off storewide for Teaching Tech subscribers [Code: tech5]
Take a look around and if you like what you see, please subscribe.
In this episode, I demonstrate two projects with geometry that needs to be spot on. Rather than design and print over and over until the fit is perfect, I demonstrate purposely creating pas with too much clearance that can be bolted into the perfect place once in position.
0:00 Introduction
0:43 Scenario 1: Tablet holder
4:49 Scenario 2: Electronic door controller
11:06 Conclusion
Get Quality Resins from 3D Printers Online. 5% off storewide for Teaching Tech subscribers [Code: tech5]
Take a look around and if you like what you see, please subscribe.
Creating sloppy parts to ensure perfect fit - 3D design for 3D printing
How To Clean Up Sloppy Guitar Playing
Better First Layer and Bed Level Fixes on 3D Printers
3 Tips for Customer Service Professionals #1: How To Use Power Phrases in Professional Greetings
Tech Tuesday #10: Troubleshooting the Headset
How to Fix Your Sloppy Guitar Playing
How Sloppy Joes Became a School Lunch Legend
Making Collet Blocks || INHERITANCE MACHINING
New Jersey’s Iconic Sloppy Joe Is Made With Russian Dressing And Cold Cuts | Legendary Eats
Learn the word sloppy in two minutes - Improve your English vocabulary with real world examples.
IMPROVE YOUR POSTURE AND BOOST YOUR HEALTH | SHIVANGI DESAI
Learn the word sloppy in one minute - Improve your English vocabulary with real world examples.
How to Sing Clearly and Stop Swallowing Your Sound | Common Vocal Mistakes
Cleaning up a sloppy roof top unit installation.
What is the Story Behind the All-American Sloppy Joe?
How to fix sloppy steering once and for all #diy
It Leaks Everywhere! - Sloppy Case Backhoe Repairs
How To Fix A Sunken Sidewalk With Spray Foam
How To Fix Sloppy Steering On Craftsman 917 Lawn Tractor.
How to create the perfect Philly cheesesteak
How To Fit Guitars In A Mix
Sloppy Joe Grilled Cheese Sandwich - How to make recipe DIY
Sloppy cards?! - Use the Table Tool to Create Order | Making Boom Cards™
Fixing a sloppy Porsche 996/986 shifter
Комментарии