filmov
tv
CNC Milling Practice
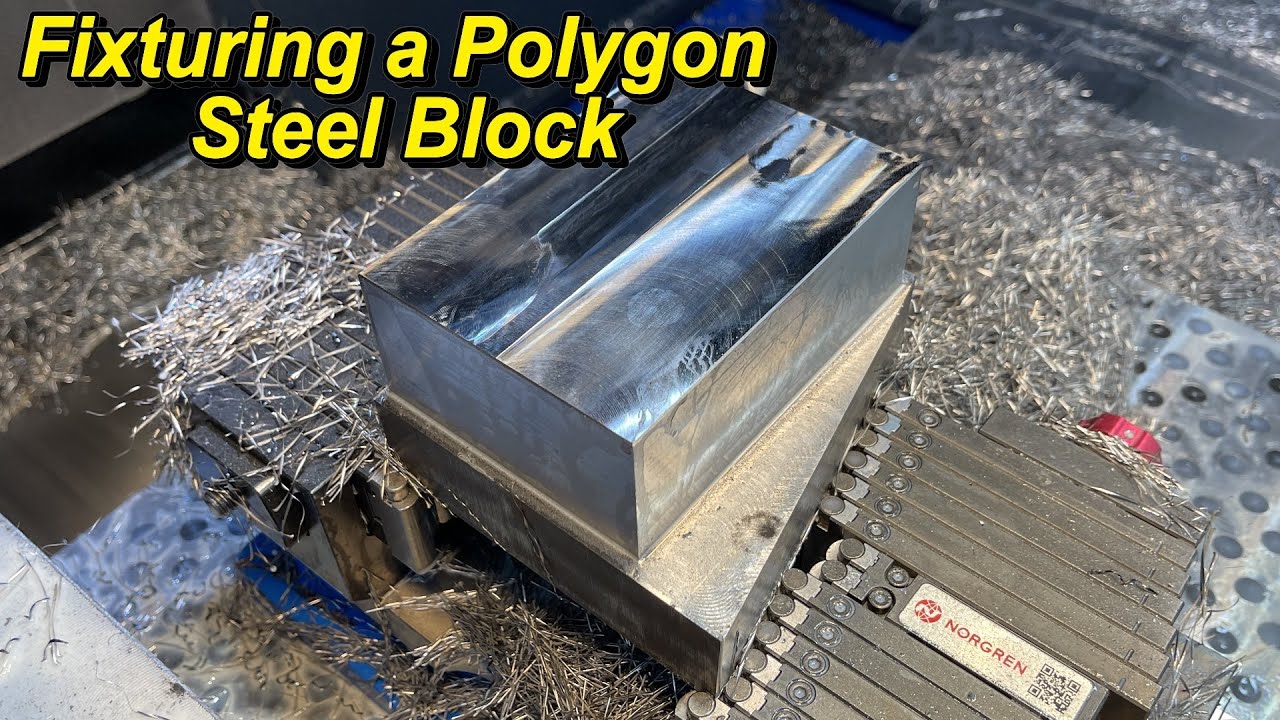
Показать описание
This was a simple practice piece I worked on one day and wanted to share some of the progress.
#abom79 #milltronics #cncmachining
#abom79 #milltronics #cncmachining
CNC Milling Practice
Why Would You Ever Use CONVENTIONAL Milling??? | Climb vs Conventional
CNC Mill Tutorial
CNC milling: how 3 axis, 4 axis, 5 axis working?
The Skill You NEED to Quickly Become a Great Machinist
Understand G code for beginners Part 1
CNC Fundamentals - Ep. 2 - How Machine Side the Bottom Side
CNC milling #cncmachining #cnc #machining
TOP 5 WAYS to EARN $100,000 as a CNC MACHINIST | DN Solutions
Milling machine - Easy job
Challenging milling of big block (cnc milling)
#CNC MILLING MACHINE PRACTICE
CNC Milling 3D Model Training Practice
#CNC MILLING MACHINE PRACTICE
CNC Milling Machine | End Milling Cutter | Practice & Learning | Abhishek Chaurasia
#Box in Ball 🙌 CNC MILLING MACHINE PRACTICE
CNC Milling Part Programming
CNC MILLING MACHINE PRACTICE on wood
Manual Mill Tutorial
CNC Milling Program Hindi | CNC Milling Operation | Milling Operation on CNC Machine Milling Program
Milltronics CNC Lathe Training
Cheap Acrylic Off Cuts for CNC Milling & Engraving Practice
Milling the name of A Country Practice Veterinary Clinic
Lots and lots of chips #cnc #cncmilling #cncmachining
Комментарии