filmov
tv
Homemade Micro Milling Spindle
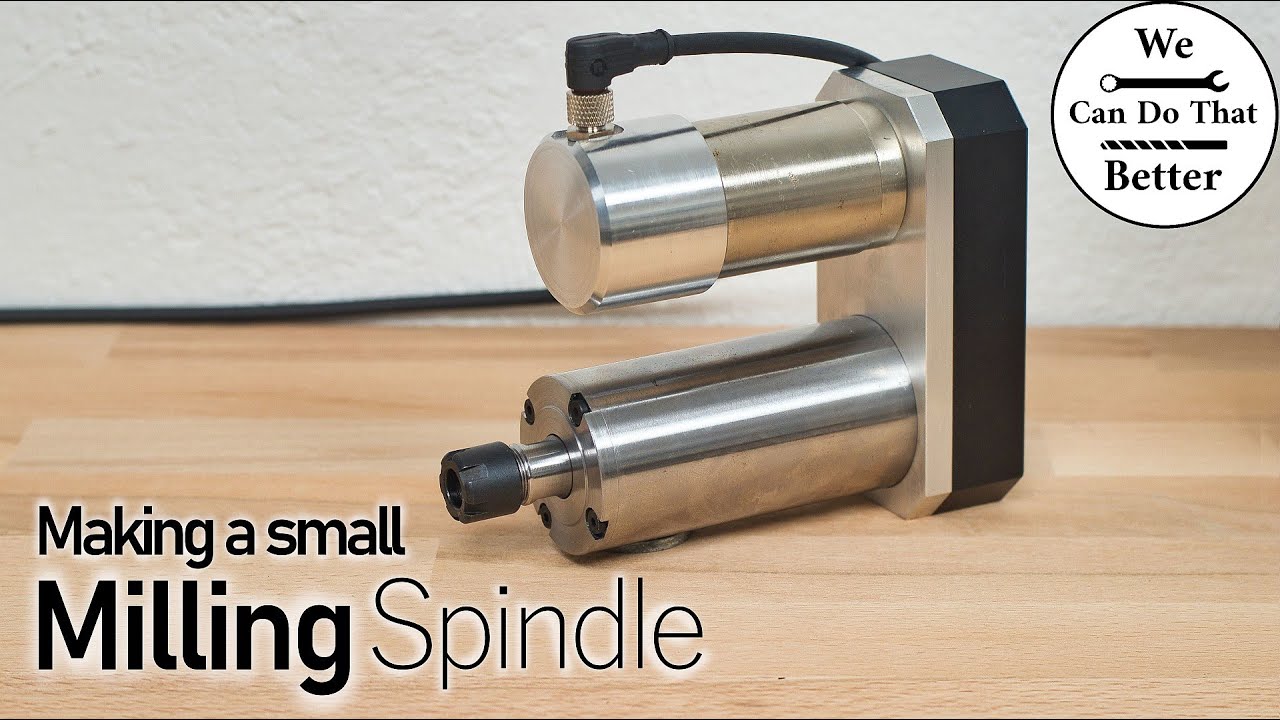
Показать описание
For a futur project I need a small milling spindle. Inspired by the article above I started to build my own one. I used an ER-11 collet extension, 7200 angular contact bearings, a piece of 40mm ground C45 round steel for the spindle housing and an Escap 32V motor for the drive. Unfortunately I could only find the servo version of this motor which has some extra encoder stuff mounted on the rear side. I removed all this but it seems that this was not the best thing for the motor. After the modification it ran not as smooth as before. So if someone has the normal Escap 35NT for me, don't hesitate to contact me :)
After the first tests the spindle seems to work quite fine. I just have to make the poly-V pulleys a little bit smaller as the belt rubs against the inside of the belt cover.
This spindle might also be used as a toolpost grinder. I guess it is not that big of a difference.
I hope you enjoy the build and the video. It is a little bit on the long side.
Let me know what you think about it.
If you have questions or suggestions feel free to comment below.
If you are interested in more DIY toolmaking and machining stuff with budget equipment, consider subscribing to the channel. I really do appreciate your support.
Thanks.
Комментарии