filmov
tv
5 Reasons NOT to 3D Print your Design
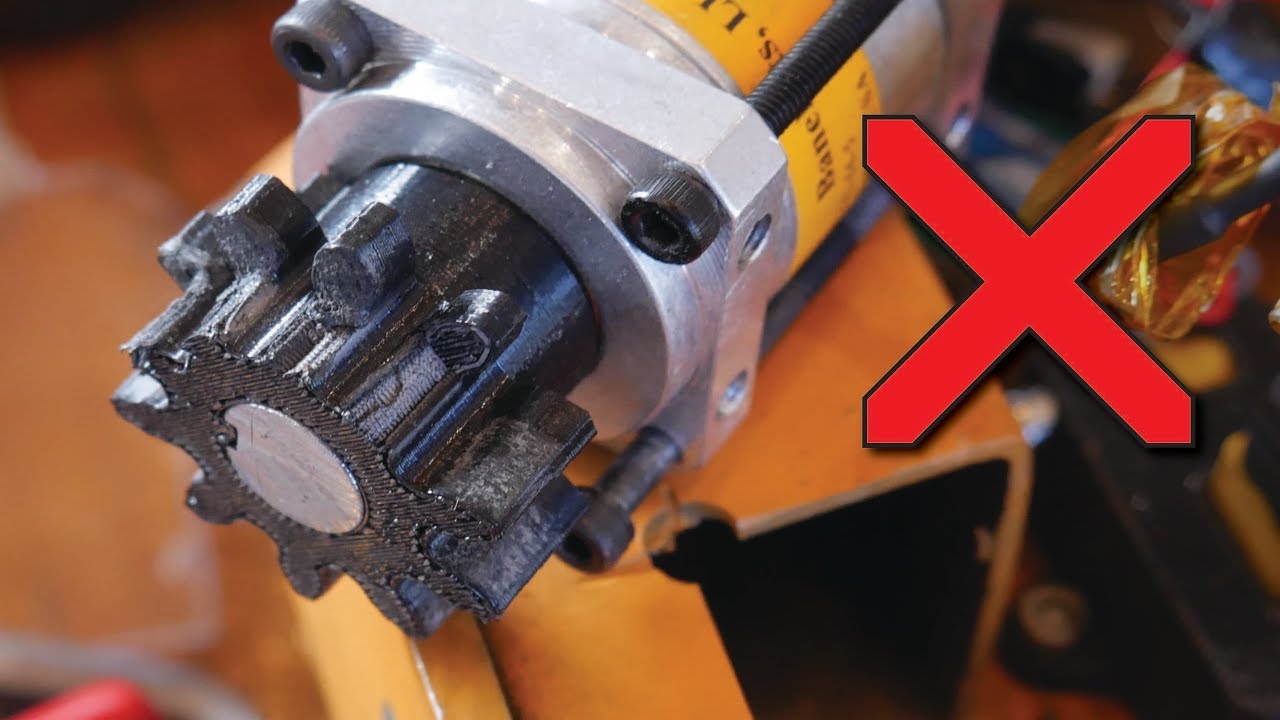
Показать описание
3D Printing is an incredible technology, but it's not magic. In this video we'll discuss 5 reasons why you might not want to use 3D Printing for the manufacturing of your design or invention.
This video is more aimed at industry and those who don't already have a 3D Printer and are considering using the technology, rather than those who have 3D Printing available at home.
Support Maker's Muse on Patreon
This video is more aimed at industry and those who don't already have a 3D Printer and are considering using the technology, rather than those who have 3D Printing available at home.
Support Maker's Muse on Patreon
Why you should NOT get a 3D printer
5 3D Printing Mistakes you WILL make - and how to avoid them! 3D Printing 101
5 reasons 3D printing is useful - My favourite practical prints
Failed 3D print (Lost adhesion to print bed)
Don't throw away all your 3D printing filament ends! Do this!
Have your 3D Prints started to suck? Watch this!
5 Reasons Why You Should Get A 3D Printing Pen
Better First Layer and Bed Level Fixes on 3D Printers
The 'Otherworldly Charm' of Overworld Pokemon Sprites
5 Big Mistakes Beginners Make with Resin 3D Printing
3D Print Not Sticking? 9 Ways to Get Perfect Bed Adhesion
6 things that made me hate 3d printing less
Understand WHY 3D prints WARP - Simple explanation with experiment!
Stop Worrying About Settings and Build Your 3D Printer Right! #Shorts
How Food Turns Into Poo | 3D Animation #Shorts
Creality Ender 3 V2 - Simple Tips for Super Clean 3D Prints
This Is What Happens During Vomiting | 3D #Shorts
Revised: 3D Printing - 13 Things I Wish I Knew When I Got Started
My Genshin sword took 150h to 3D print! ⚔️ #diycrafts #cosplay
Why you should get a 3D printer NOW
3D Printing is SLOWWW😩
How to connect 3D Printed Parts!
3D Printing Myths I used to believe...
I Bought the 5 Cheapest 3D Printers on Amazon
Комментарии