filmov
tv
This Genius Propeller Will Change Transport Forever
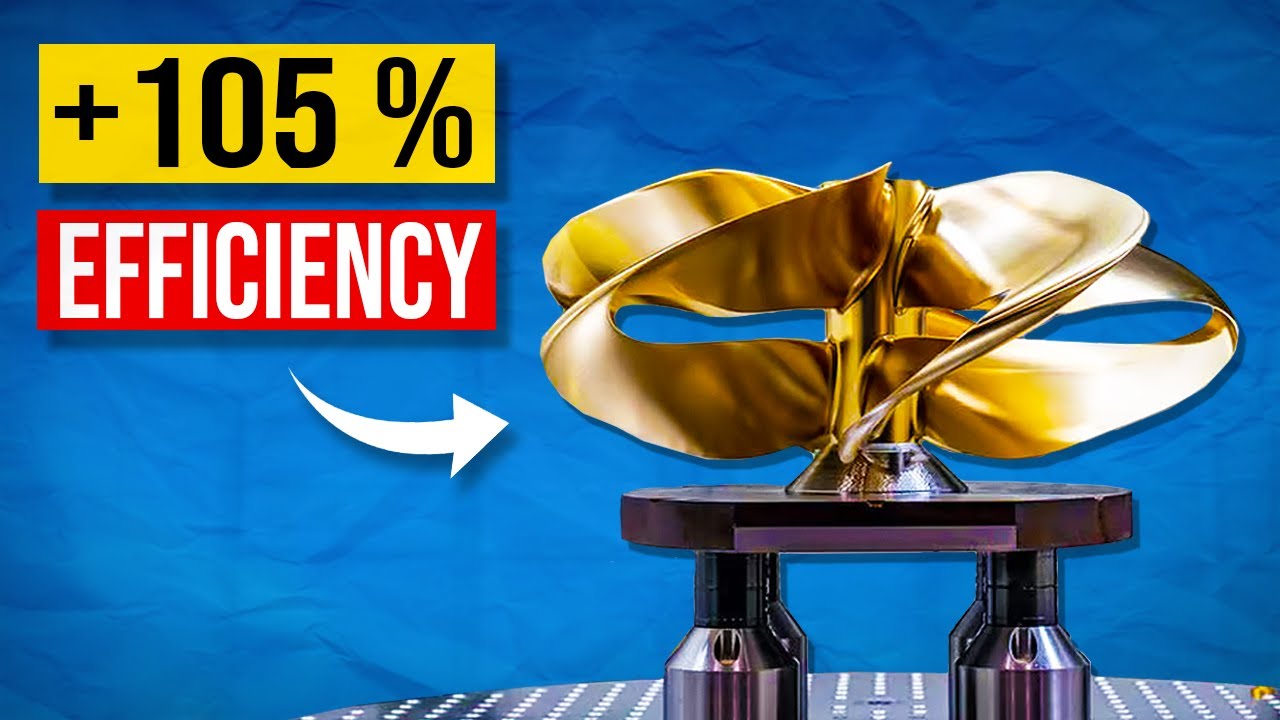
Показать описание
Sharrow and MIT have both been working on toroidal propellers which have shown incredible results.
In this video we look at a new design of propellers known as toroidal propellers. These have been shown to increase efficiency, thrust, and reduce the noise of both boats and drones. There could be many applications for this, such as cargo ships, electric flying taxies, and even computer fans.
Sources:
#breakthrough #drones #boats
In this video we look at a new design of propellers known as toroidal propellers. These have been shown to increase efficiency, thrust, and reduce the noise of both boats and drones. There could be many applications for this, such as cargo ships, electric flying taxies, and even computer fans.
Sources:
#breakthrough #drones #boats
This Genius Propeller Will Change Transport Forever
This Genius Propeller Will Change Aviation Forever
This Genius Propeller Will Change Transport Forever
Genius Propeller Is About to REVOLUTIONIZE Ships, Here's Why
How This Genius Propeller Will Change Aviation Forever!
This ULTIMATE Propeller Design Will Change the Future of Transportation
Why This Propeller will Change Transportation Forever
How This Propeller Will Change Our Transport
This Genius Airplane consumes Less Fuel than SUV
Testing MIT's Toroidal Drone Propeller Design & Sound #shorts
This Propeller will Change Aviation Forever!
Propeller of the future?!
Propeller Effects. #aviation #propeller #pilot
This Propeller will Change Aviation Forever!
This New Propeller Design Will Change the Aviation Industry Forever!
The Genius Propeller that will alter travel forever!
How This Propeller will Change Transportation Forever
Revolutionary Propeller Design: Unmatched Efficiency Revealed!
BOAT PROPELLER REPAIR!
This MIT Propeller Is Going To Change Aviation Forever
Toroidal propeller 🤩🤩
Aeroplane Propeller Changes Spin Direction Mid Flight!??! #shorts
toroidal propeller, just one wing.
How This Propeller Will Change Our Transport
Комментарии