filmov
tv
Omni-Wheel Balancing Robot?
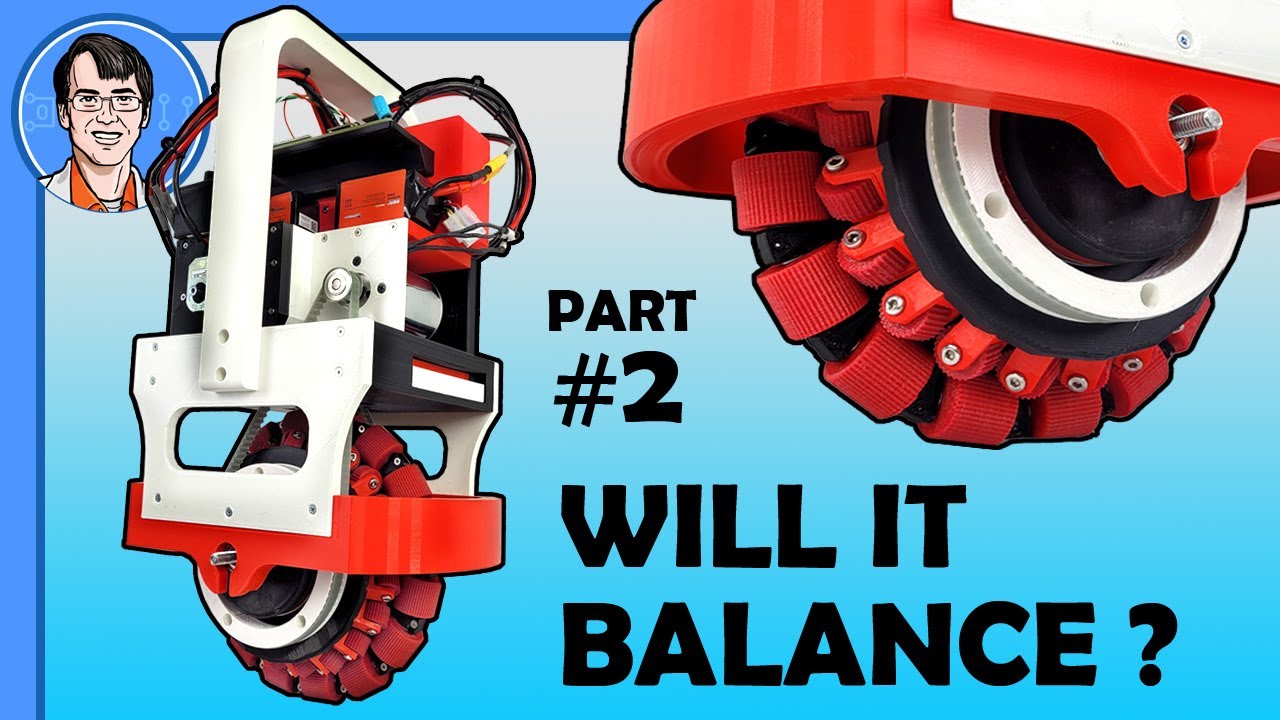
Показать описание
Last time I built an omni-directional wheel which had powered wheels around its circumference which drive in a perpendicular axis to the main drive axis.
I looked at two existing designs for this, the first was OmBURo which uses helical gears to convey motion to the smaller wheels from a motor aligned with the main axis of the wheel. This allows differential drive between two motors, one driving the main axis, and one driving the smaller wheels. This works pretty well and allows the complete machine to balance on one wheel.
I also looked at the Honda U3-X, and the Honda patent for their active omni wheel. This is a very interesting design, using a set of rollers mounted at 45 degrees either side of the small wheels, which cause the small wheels to rotate as the two side mounted hubs are rotated against each other.
I made a couple of changes to this design, mainly adding a central hub to hold all of the small wheels around the circumference in place. The original patent showed them all mounted on a flexible shaft, but this is quite hard to reproduce with no stretch and keeping high torsion resistance.
I used thrust bearings, and ball bearings to keep everything aligned and to keep tension on the central hub.
Even though all my rollers and wheels have straight edges, so they don’t follow a perfectly round contour, I found that the natural flexibility in my wheels helped me out because as force is applied to the top of the wheel, it squashes the wheels against the side rollers at the bottom, and this seems to give us quite consistent traction.
I wanted to improve on this slightly though, and also reduce friction a little, so this time I’ve made new wheels with a rigid hub. These snap into place due to a feature in the middle, and this allows the wheel’s rigid hub to run on the axle rather than the TPU, but still gives us some friction to grip the driving surface. I’ve mounted each axle in a slot shaped feature so it can still move and slide to comply with the rollers on each side as force is applied to the wheel.
That seems to run ok, so the plan is to attempt to make a one-wheel balancing robot with it, just like OmBURo and the Honda U3-X.
Links:
You can support me on Patreon or buy my Merchandise:
***************************
***************************
Affiliate links - I will get some money of you use them to sign up or buy something:
***************************
***************************
Other socials:
***************************
***************************
Huge thanks to my Patrons, without whom my standard of living would drastically decline. Like, inside out-Farm Foods bag decline. Plus a very special shoutout to Lulzbot, Inc who keep me in LulzBot 3D printers and support me via Patreon.
HARDWARE/SOFTWARE
Below you can also find a lot of the typical tools, equipment and supplies used in my projects:
XROBOTS
Former toy designer, current YouTube maker and general robotics, electrical and mechanical engineer, I’m a fan of doing it yourself and innovation by trial and error. My channel is where I share some of my useful and not-so-useful inventions, designs and maker advice. Iron Man is my go-to cosplay, and 3D printing can solve most issues - broken bolts, missing parts, world hunger, you name it.
XRobots is the community around my content where you can get in touch, share tips and advice, and more build FAQs, schematics and designs are also available.
Комментарии