filmov
tv
Waterjet cutter built with a cheap pressure washer
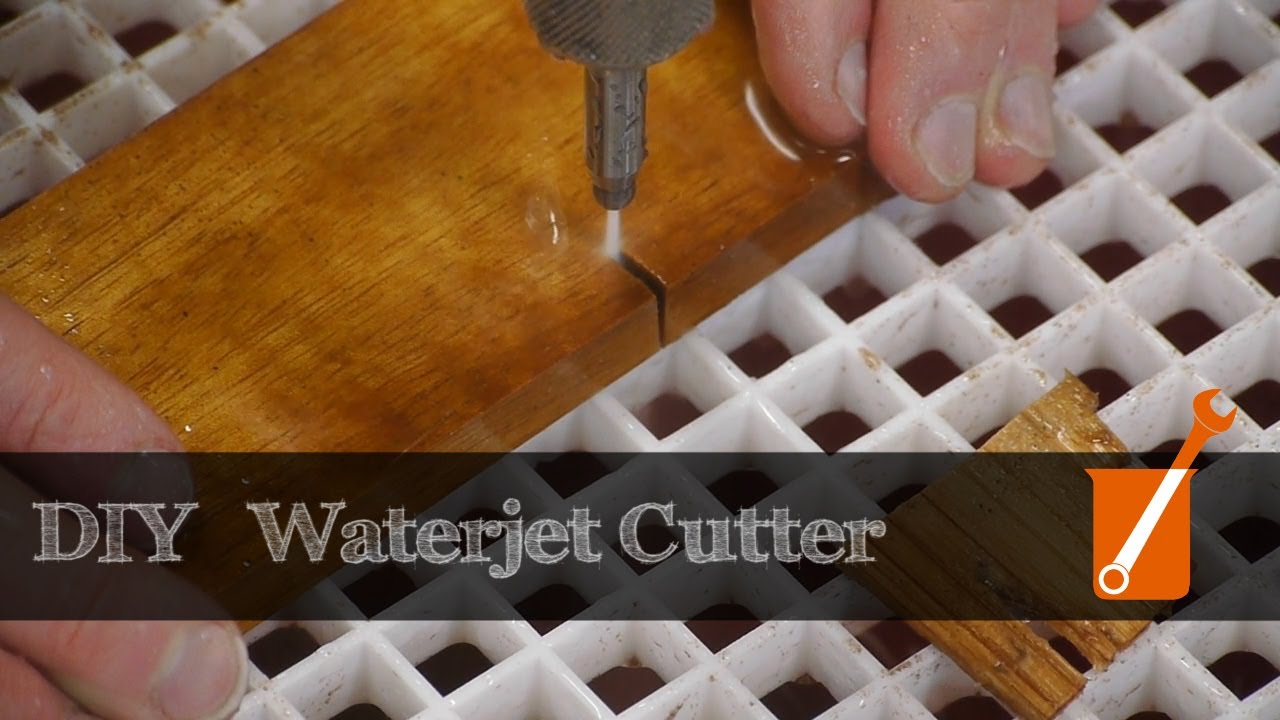
Показать описание
Building an abrasive waterjet cutter with a $150 pressure washer.
80 grit garnet abrasive - ebay
80 grit garnet abrasive - ebay
Waterjet cutter built with a cheap pressure washer
How Does a Waterjet Work? Waterjet 101
Apex 60 The Best 5 Axis Waterjet Ever Built
#waterjet Do you like this water jet cutting method?...
Water Jet Cutter | The most powerful cutter
Water Jet Cutting Vs Dummy Hand 😨
Waterjet Cutting in Action
5-Axis Waterjet Cutting.
What is shim cutter? (brief demonstration)
CNC water jet cutting
Jekran CNC Waterjet Cutting Systems
DIY Waterjet cutter
Custom Waterjet Built with Standard Parts
CAN CUT THROUGH EVERYTHING ? Water jet cutting machine
Desktop Waterjet Cutter. Wazer Waterjet review
Desktop Waterjet cutting a Batarang
Why WaterJet cutting is used?🤯 #shorts #viral
Gas-powered waterjet cutter (follow-up) and other project updates
The First Desktop Waterjet
Waterjet Cutter (How It Works)
5-Axis WaterJet Cutting Like Butter. #cnc #fabrication #5axismachining #waterjet #work
The process of water jet cutting glass holes- Good tools and machinery make work easy
Waterjet Cutting - How It's Made!
9 water jets cutting machines
Комментарии