filmov
tv
Leaving Fusion might have been a Mistake
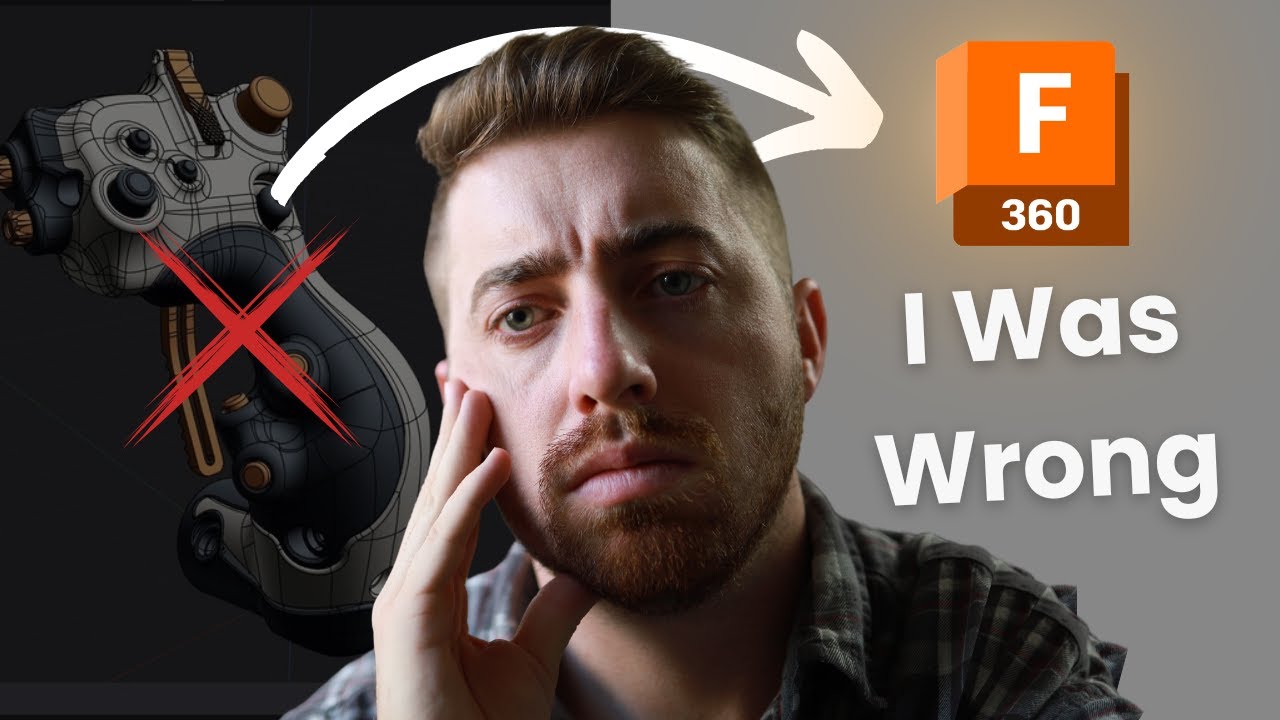
Показать описание
Leaving fusion 360 for plasticity. Here are the 3 features I miss the most.
My Designs:
-------------------------------------------------------------------------------------------------------------------
Disclaimer: Some links in this description may be affiliate links. This means I may earn a small commission if you click them and make a purchase. It's no extra cost to you, but it truly helps keep this channel alive. Thank you!
-------------------------------------------------------------------------------------------------------------------
🎵 Where I got my Music for this video:
Full List of My Gear:
Camera
Lens
Main Microphone
Main Mic Arm
Wireless Mic
Main Light
Light Diffuser
Light Stand
Camera Slider
Compact Fluid Head
Quick Release Plates
Heavy Duty Quick Release
Quick Camera Stand
Desk Camera Stand
Cheap LED Lights
Keyboard
Mouse
Monitor
Computer PC Case
Laptop
My Designs:
-------------------------------------------------------------------------------------------------------------------
Disclaimer: Some links in this description may be affiliate links. This means I may earn a small commission if you click them and make a purchase. It's no extra cost to you, but it truly helps keep this channel alive. Thank you!
-------------------------------------------------------------------------------------------------------------------
🎵 Where I got my Music for this video:
Full List of My Gear:
Camera
Lens
Main Microphone
Main Mic Arm
Wireless Mic
Main Light
Light Diffuser
Light Stand
Camera Slider
Compact Fluid Head
Quick Release Plates
Heavy Duty Quick Release
Quick Camera Stand
Desk Camera Stand
Cheap LED Lights
Keyboard
Mouse
Monitor
Computer PC Case
Laptop
Leaving Fusion might have been a Mistake
He left the audience and judges in panic! #shapeshift #americasgottalent #fusion #skinwalker #agt
Fusion Dancer Girl Leaves a Mark on America’s Got Talent #agt #americasgottalent #gottalent
pvz fusion duck zombie is similar:#pvz #pvzfusion
AI's Vision of Normal plants vs Fusion plants 💫🔥
AI's Vision of Normal plants vs Fusion plants 🥔🔥
pvz fusion flame melon is similar to:#pvz #pvzfusion
AI's Vision of Normal plants vs Fusion plants 🎯💫🔥
pvz fusion snow beast king is similar to:#pvz #pvzfusion
pvz fusion fire lotus is similar to:#pvz #pvzfusion
pvz fusion the ultimate swordsman star peach is similar to:#pvz #pvzfusion
Almost 3 Years As A condo Owner in Miami Beach.. This is pretty normal on a Monday in South Beach
AI's Vision of Normal plants vs Fusion plants : Garlic Family 🧄🌱
pvz fusion magnetic cactus similar to:#pvz #pvzfusion
pvz fusion flame melancholy mushroom is similar to:#pvz #pvzfusion
Escaped inmates from New Orleans jail might have had inside help, says Orleans Parish Sheriff
pvz fusion hyperspace nut is similar to:#pvz #pvzfusion
pvz fusion pumpkin is similar to:#pvz #pvzfusion
pvz fusion mod skins are similar:#pvz #pvzfusion
Try This…You Never Knew Your Wrists Can Feel So Good! Dr. Mandell
pvz fusion magnetic clover is similar to:#pvz #pvzfusion
New plugin for Autodesk Fusion where you can add parts to your cart without leaving the app✔️
AI's Vision of Normal plants vs Fusion plants 🎯🔥
Get back to walking faster after an #anklesprain! Watch 'Tape Your Sprained Ankle' on our ...
Комментарии