filmov
tv
Makera Carvera Desktop CNC: Great for (wealthy) Beginners ?
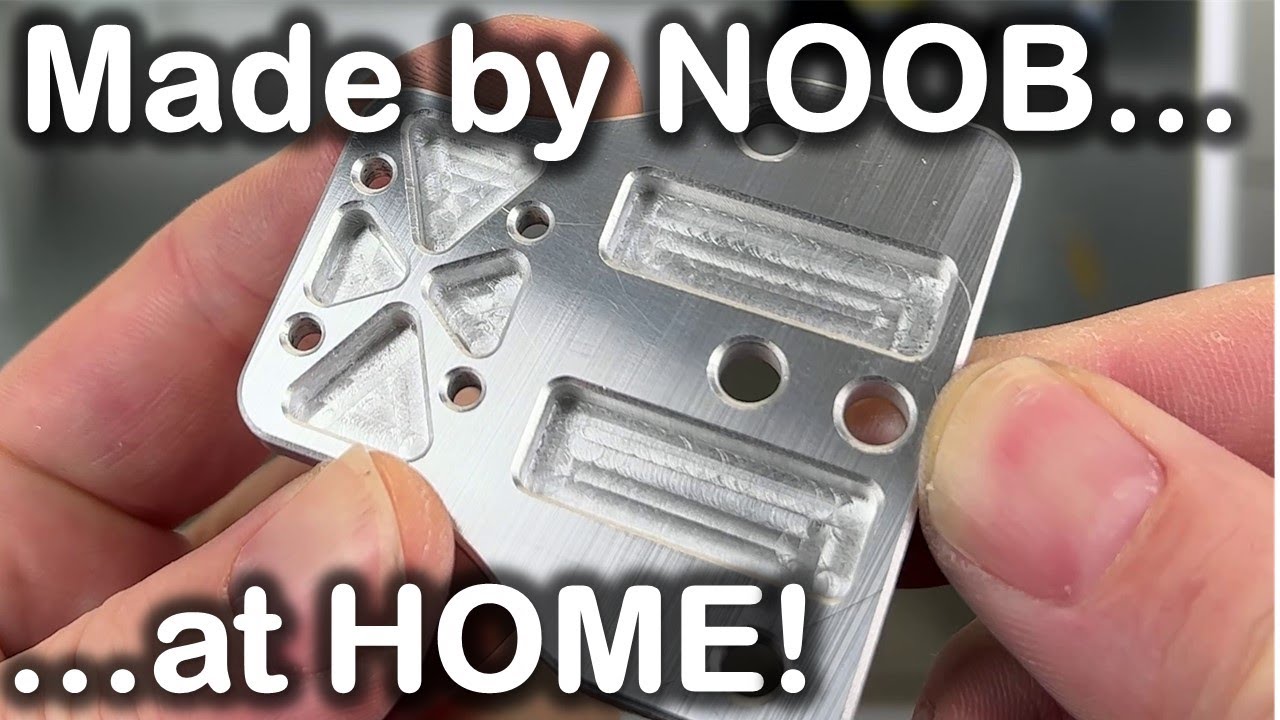
Показать описание
Black Friday! Get the discounted Carvera here* and use code "247" for another 100USD discount:
The Makera Carvera is the first CNC mill I ever had my hands on before.
As a 3D printing guy, I honestly had quite some doubts and anxieties about getting into CNC machining.
But, oh boy… ball screws driven by servo motors, automated levelling, automated tool changing… and there is way more to discover on that modern cnc machine. Sounds too good to be true for beginners and even advanced users, right?! Join me, a total CNC noob, doing my first steps in CNC milling and getting my first project milled out of aluminium!
Support my work on PATREON:
Additional Links
--------------------------------
Chef's Menu:
----------------------------
00:00 Intro
01:29 What you get and Setup
06:39 Sponsor PCBWay
07:25 First Steps and Example Projects
13:25 My First CNC Alu Project
14:44 CAM: Getting started
18:26 First time milling an Aluminium part
22:10 Lessons leaned
24:51 Negatives on Carvera and Conclusion
*Affiliate link at no extra cost - thanks for supporting!
#cncmilling
Комментарии