filmov
tv
Makera Carvera Auto Tool Changer Benchtop CNC machine, In-depth review, aluminum cutting stress test
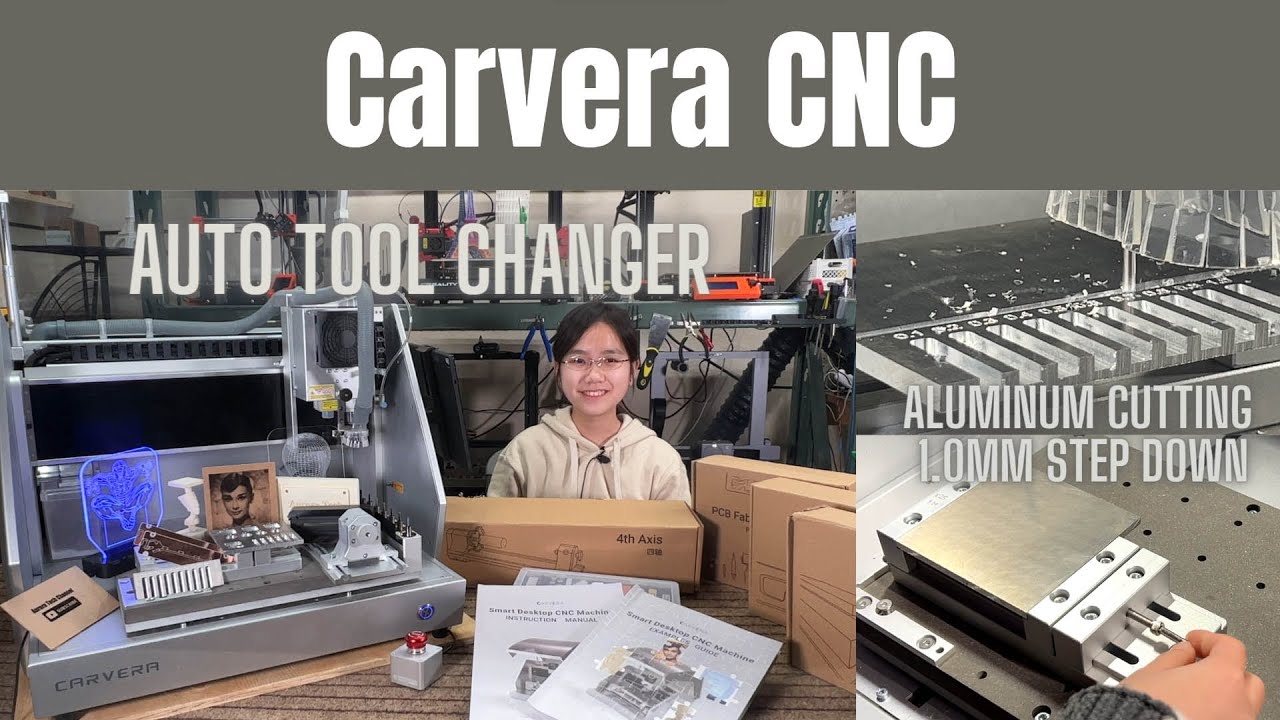
Показать описание
00:00 Intro
03:06 Unboxing
04:45 Software setup
05:58 Hardware testing, tool setup
07:13 Example job: PCB engraving, drilling, and cutting
12:00 Example job: ABS base cutting
14:49 Example job: Aluminum cutting
15:56 Example job: Acrylic engraving and cutting
17:44 Example job: Laser engraving (photo)
18:10 Example job: 4th axis test job
20:14 Fusion 360 Setup
21:06 Epoxy milling and cutting using Fusion 360 CAD & CAM
25:32 Aluminum cutting using Fusion 360 CAD & CAM (push the machine to it's limit)
33:03 Laser engraving using LaserGRBL
33:57 Pros and Cons
38:21 Conclusion
Welcome back to Aurora Tech Channel. Today, I will be reviewing this Carvera Benchtop CNC from Makera. Let’s take a look at the features of this machine. It has a 6-bay auto tool changer and a 200W brushless spindle with a hall sensor that provides feedback to the controller software. For the motion system, the X, Y, and Z axis all use 12mm ball screws instead of the lead screws you see on other budget CNCs and 3D printers. The X and Z axis use 15mm linear rails and the Y-axis use 25mm linear rods. The stepper motors on all axes are 30W closed-loop servo motors. The machine weighs around 110 pounds and the structure of the machine is made by CNC using solid aluminum and sheet metal. The bed is a 10mm thick aluminum bed with a replaceable water-resistant MDF bed on top. The working area is 360 by 240 with a 140mm Z height. You can pay an extra $300 to get a 4-axis, which I will also test out in this video.
As for the other features, this machine comes with both a manual probe and auto probe sensor, which supports auto leveling. There is a built-in vacuum, a dust bin, as well as a 2.5W laser module for some light engraving jobs.
At the price of $4000, I can’t see any direct competition for it in the market. The closest machines I can find are the Carbide 3D Nomad 3, which costs around $3000, but it doesn’t come with an auto tool changer. There is no dust collection system, no laser module, no auto probe or auto leveling, and it just uses lead screws and linear rods instead of ball screws and linear rails, and by default, it only comes with a 70W spindle. The working area is also much smaller at 200x200 with a 80mm Z height.
Another machine that is similar to the Nomad 3 is the Bantam Tools Desktop CNC, which costs $6500. It comes with a slightly more powerful 250W spindle, but it has no auto tool changer, no auto probe or auto leveling, no dust collection, no laser module, and it just uses regular lead screws and linear rods. The working area is also smaller at 178x229 with a 83mm Z-height.
The only desktop or benchtop CNC that comes with an auto tool changer that I can find is the Roland MDX-50, which costs over $10,000 but only comes with a 50W spindle that is mainly used for PCB milling. If you need a 4th axis on this machine, it costs another $4000, which is the same price as this Carvera CNC machine.
Overall, I am really excited to test this out. I would like to thank Makera for sending me this machine to review, and with that, let’s get started.
Affiliate links:
Makera Carvera Auto Tool Changer Benchtop CNC machine
Low profile CNC Vise
Super cheap used Creality Printers ($69):
Maybe in bad condition, but if you know how to fix some common issues of a 3D printer and have spare parts to replace by yourself, that could be an amazing deal:
Refurbished Creality Printers (SAVE UP TO 50%):
03:06 Unboxing
04:45 Software setup
05:58 Hardware testing, tool setup
07:13 Example job: PCB engraving, drilling, and cutting
12:00 Example job: ABS base cutting
14:49 Example job: Aluminum cutting
15:56 Example job: Acrylic engraving and cutting
17:44 Example job: Laser engraving (photo)
18:10 Example job: 4th axis test job
20:14 Fusion 360 Setup
21:06 Epoxy milling and cutting using Fusion 360 CAD & CAM
25:32 Aluminum cutting using Fusion 360 CAD & CAM (push the machine to it's limit)
33:03 Laser engraving using LaserGRBL
33:57 Pros and Cons
38:21 Conclusion
Welcome back to Aurora Tech Channel. Today, I will be reviewing this Carvera Benchtop CNC from Makera. Let’s take a look at the features of this machine. It has a 6-bay auto tool changer and a 200W brushless spindle with a hall sensor that provides feedback to the controller software. For the motion system, the X, Y, and Z axis all use 12mm ball screws instead of the lead screws you see on other budget CNCs and 3D printers. The X and Z axis use 15mm linear rails and the Y-axis use 25mm linear rods. The stepper motors on all axes are 30W closed-loop servo motors. The machine weighs around 110 pounds and the structure of the machine is made by CNC using solid aluminum and sheet metal. The bed is a 10mm thick aluminum bed with a replaceable water-resistant MDF bed on top. The working area is 360 by 240 with a 140mm Z height. You can pay an extra $300 to get a 4-axis, which I will also test out in this video.
As for the other features, this machine comes with both a manual probe and auto probe sensor, which supports auto leveling. There is a built-in vacuum, a dust bin, as well as a 2.5W laser module for some light engraving jobs.
At the price of $4000, I can’t see any direct competition for it in the market. The closest machines I can find are the Carbide 3D Nomad 3, which costs around $3000, but it doesn’t come with an auto tool changer. There is no dust collection system, no laser module, no auto probe or auto leveling, and it just uses lead screws and linear rods instead of ball screws and linear rails, and by default, it only comes with a 70W spindle. The working area is also much smaller at 200x200 with a 80mm Z height.
Another machine that is similar to the Nomad 3 is the Bantam Tools Desktop CNC, which costs $6500. It comes with a slightly more powerful 250W spindle, but it has no auto tool changer, no auto probe or auto leveling, no dust collection, no laser module, and it just uses regular lead screws and linear rods. The working area is also smaller at 178x229 with a 83mm Z-height.
The only desktop or benchtop CNC that comes with an auto tool changer that I can find is the Roland MDX-50, which costs over $10,000 but only comes with a 50W spindle that is mainly used for PCB milling. If you need a 4th axis on this machine, it costs another $4000, which is the same price as this Carvera CNC machine.
Overall, I am really excited to test this out. I would like to thank Makera for sending me this machine to review, and with that, let’s get started.
Affiliate links:
Makera Carvera Auto Tool Changer Benchtop CNC machine
Low profile CNC Vise
Super cheap used Creality Printers ($69):
Maybe in bad condition, but if you know how to fix some common issues of a 3D printer and have spare parts to replace by yourself, that could be an amazing deal:
Refurbished Creality Printers (SAVE UP TO 50%):
Комментарии