filmov
tv
Push vs Pull: Flux Core Edition
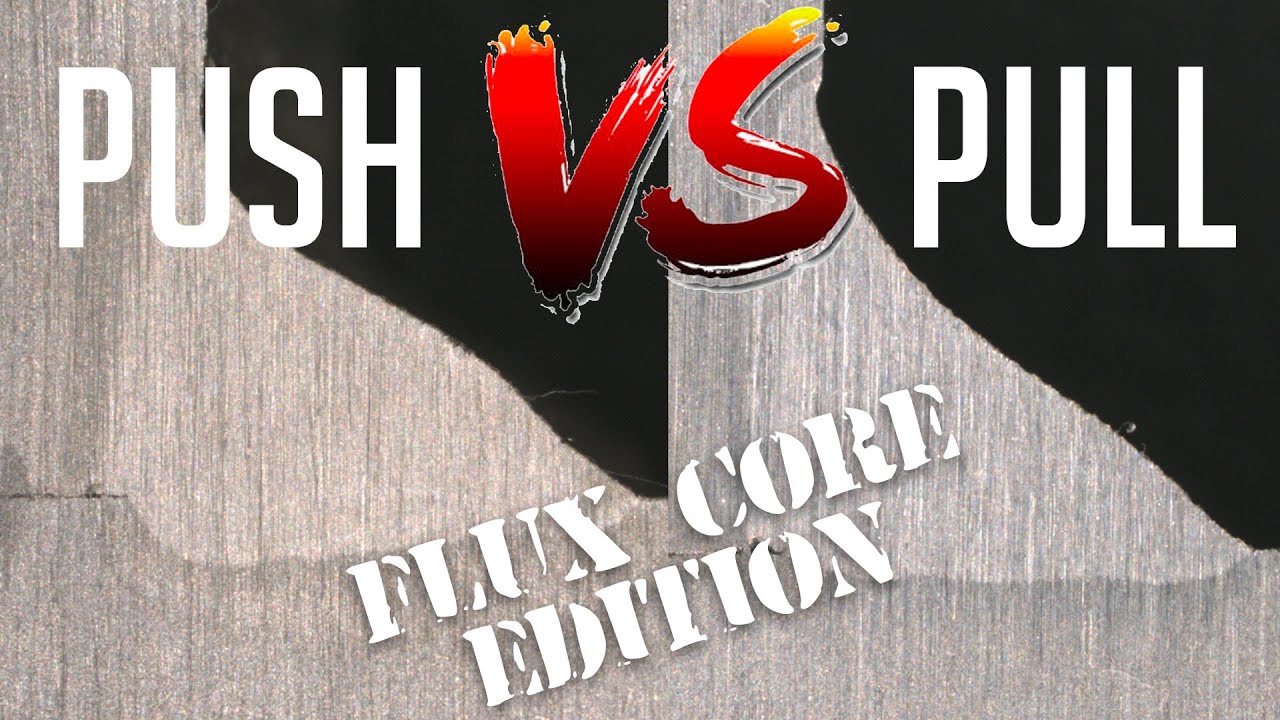
Показать описание
In the last episode we did a push vs pull test with spray arc MIG where we did a cut and etch to examine if the travel angle made a difference. Today we are doing a similar test with Gas shielded flux core welding. We had some comments in the previous video that wanted us to test it at a more drastic angle, so in this video we are raising the stakes and doing both tests at a 25 degree angle.
Talk with Bob, Jason and Mancub!
------------------------------------------------
EQUIPMENT WE LIKE AND USE IN THE SHOP:
VIDEO SCHEDULE:
MONDAY @ 5:30 PM ET
WEDNESDAY @ 5:30 PM ET
FRIDAY @ 5:30 PM ET
#welddotcom
Talk with Bob, Jason and Mancub!
------------------------------------------------
EQUIPMENT WE LIKE AND USE IN THE SHOP:
VIDEO SCHEDULE:
MONDAY @ 5:30 PM ET
WEDNESDAY @ 5:30 PM ET
FRIDAY @ 5:30 PM ET
#welddotcom
Push vs Pull: Flux Core Edition
#1 Way to Get Better Flux Core Welds
Push vs Pull: Metal Core Edition
MIG Welding Techniques: Push vs. Pull
Push VS Pull: Which MIG Welding Technique Gets Better Penetration?
PUSH vs PULL - Which is better for MIG Welding?
Does Flux Core Welding Work for Auto Body?
5 Tips and Tricks to Improve Flux Core Welding
Gasless Flux Core for Beginners #1 BIG Thing
3 REASONS YOU GET WORMHOLE POROSITY!!
Slag you drag ??? #weld #welding #weldernation #weldingschool #gmaw #migwelding #fcaw #fluxcore
Welding Straight VS Weaving Or Wave | Flux Core Welding For Beginners |
Quick Tip: Push vs. Pull
Push VS Pull 🔥🔥 Repost from @vanthefabricator(TT) #shorts
Dual Shield Flux Core Welding Basics
MIG Inductance & Push Vs. Pull Techniques | Welding Tips & Tricks #Welding #MIG #Techniques
PUSH vs. PULL MIG Welding | Cut and Etch
#1 Mistake Made When Flux Core Welding (one simple Trick)
Did you know this about MIG and Flux Core? ✍️😅
Push VS Pull Repost from @vanthefabricator(TikTok) #yeswelder #welding #weld #migwelding #shorts
Flux Core Welding Blind - Here's How to Fix It
#1 Tip and Trick to Improve Flux Core Welding
How Pulsed MIG Welding Works...And do you need it?
Push VS Pull Mig
Комментарии