filmov
tv
This project nearly broke me... Building a 1kW Subwoofer from Hempcrete!
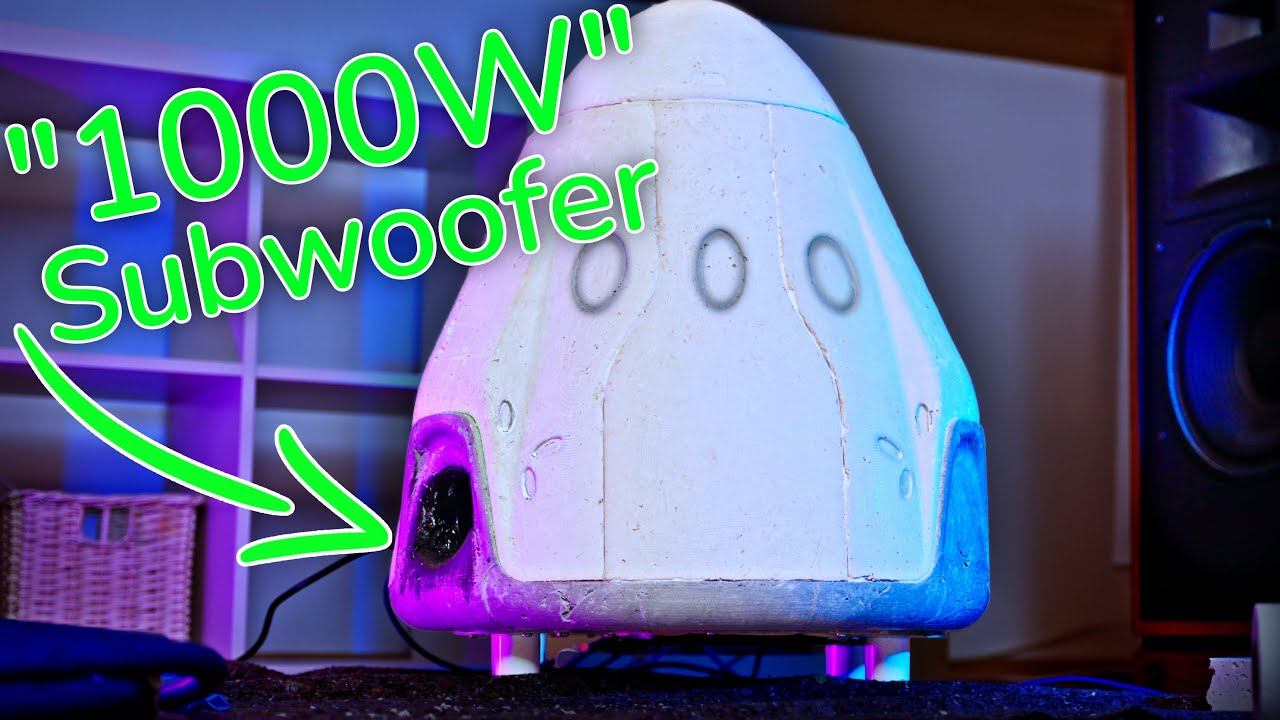
Показать описание
Inspired by the design of the SpaceX Dragon capsule, I set out to mold its shape into a highly functional subwoofer, made with eco-friendly materials!
Product links are affiliate links - I may earn a commission on qualifying purchases (at no extra cost to you)
Product links are affiliate links - I may earn a commission on qualifying purchases (at no extra cost to you)
This project nearly broke me... Building a 1kW Subwoofer from Hempcrete!
Making Mordor nearly broke me...
Picture Frame Project that nearly broke me 😳
Making - a PSYCHEDELIC Guitar from 1000s of DVDs.. This one nearly broke me!
This Project Almost BROKE Me!! [Final Fantasy VII Reactor Boss Diorama]
This Paint Job Nearly Broke Me! - Making the Ocean Oracle from Ninja Must Die!
This 'cheap' repair almost BROKE me.
Making Fortnite IRL nearly broke me...
Project Playtime is the most broken game of the year. ft. AstralSpiff
PS3 #2: Ressurecting the impossable! | EPIC rollercoaster repair that nearly broke me.
The Diorama that Almost Broke Me... (W/ Waterfall Tutorial)
You may want to cry now... | Love Live Edit #lovelive #sad #shorts #freaks
Project Zomboid has officially broke me.
6 Week MINI REFIT 😬⛵The Projects that Nearly Broke Us - Sailing Vessel Delos Ep. 310
6 Months of Org Mode Nearly Broke Me (Emacs Life)
Tanjiro Kamado [AMV/Edit] - Broke me first
The Hearts Of Iron 4 Achievement That Broke Me
The Man Hangs The Woman In Mid-air.#shorts
The Craft Kit That Almost Broke Me
Miles Away - Bring Me Back (Lyrics) ft. Claire Ridgely
How Medical Staples Work 🤔
This Model Almost Broke Me - SPz Puma (RFM 1/35)
This Viewer Level Broke Me
I love these books🫶🏻 #booktok #booktube #books #bookreview #bookhaul #bookrecommendations #fyp
Комментарии