filmov
tv
Easier Machining Using the Incremental Mode on your DRO
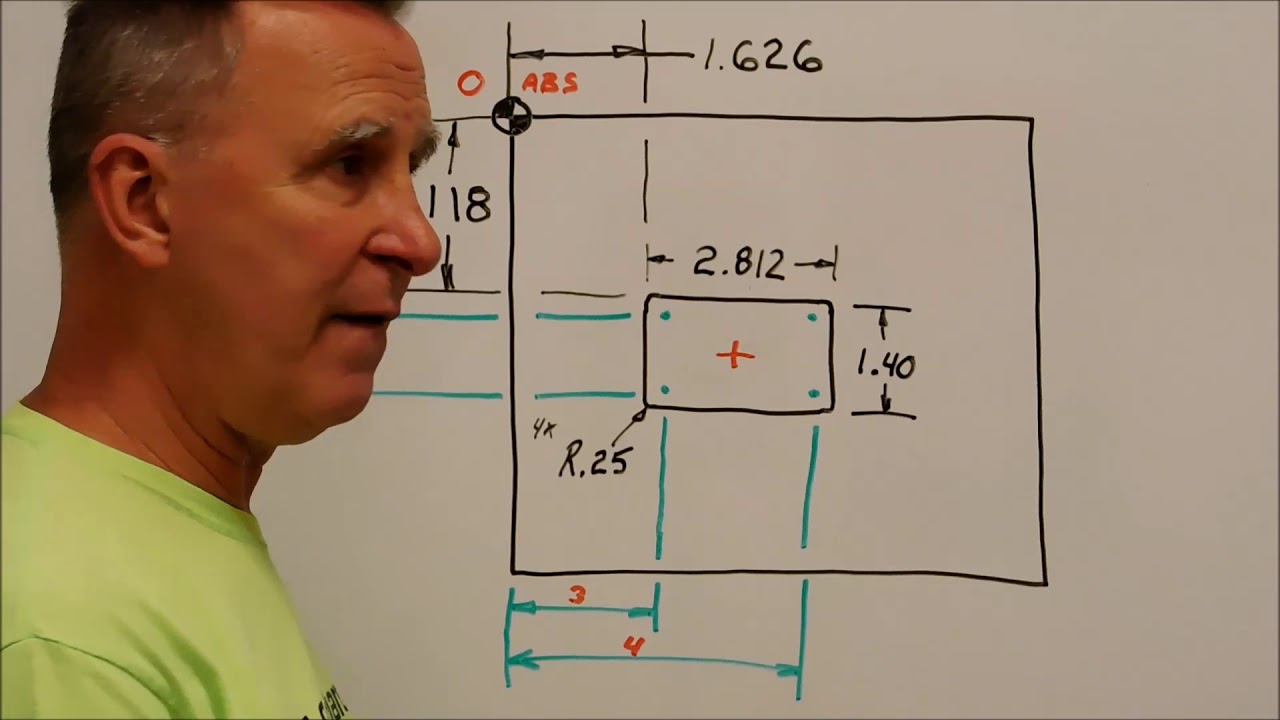
Показать описание
Many of us with DRO's rarely switch over to the incremental mode. Once you see the benefits and possible applications of using it, I bet you use it more often. Take a Look !!
Easier Machining Using the Incremental Mode on your DRO
When to Use Absolute vs Incremental Coordinates - Quick Machining Tip #22
Machina - Incremental Metal Sheet Forming
Workshop Tips #13 - DRO Absolute & Incremental Explained
incremental programe use for jows boring very simple trick
Using G16 Polar On a Fanuc control in Incremental (Mill Hexagon)
Incremental Encoder (Shaft Encoder)- how it works
Incremental & absolute modes of CNC Programming
Incremental Sheet Forming (ISF) Machine
Tutorial 1-Machine Learning Model Retraining Approach-Incremental And Continuous Model Training 🔥🔥🔥🔥...
Using absolute and incremental mode on a digital readout.
G90 vs G91 - The difference between absolute and incremental positioning
How to facing in cnc machine with Incremental programe #shorts #cnc #cncmachine
CNC Programming Tutorials | Absolute & Incremental Co-ordinate System Explained | VMC #1
Incremental loading
Absolute incremental machining modes revisit
incremental and absolute settings
incremental programe use in cnc live practical #shorts #cnc #cncmachine
ESA cnc. How to use incremental movements
How to do step turning with Incremental programe in cnc #shorts #cnc #cncmachine
CNC Router Programming using G-Code and the incremental G91 system.
How To Do Incremental Learning in Machine Learning | Machine Learning | Data Magic AI
incremental program in cnc jow boring #shorts #cnc #cncmachine
CNC Engraving Made Easy Using G47 – Part 1 – Haas Automation Tip of the Day
Комментарии