filmov
tv
When to Use Absolute vs Incremental Coordinates - Quick Machining Tip #22
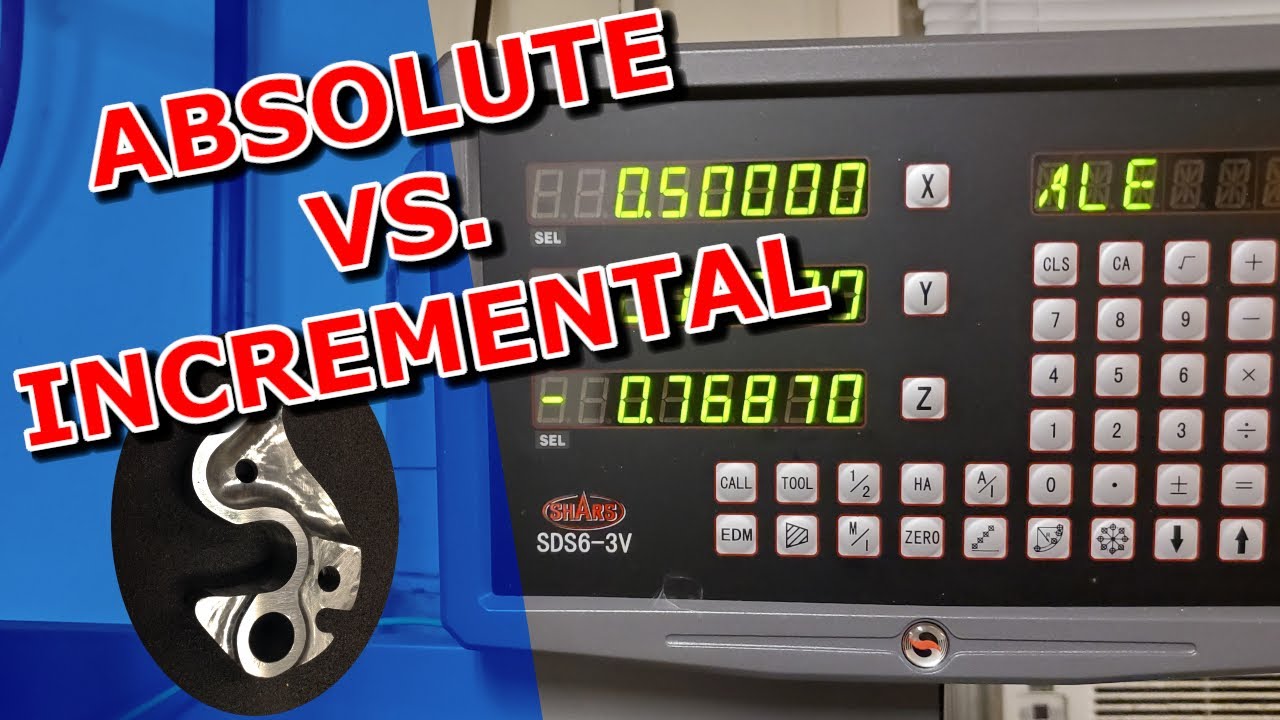
Показать описание
In my video where I discussed machine tool coordinates, G. Tucker asked for examples of when to use absolute and incremental positioning and this is my response. Enjoy!
If you like my videos, please consider supporting my channel on Patreon. You'll get access to gag reels and I'll give you a shout out in my videos.
If you like my videos, please consider supporting my channel on Patreon. You'll get access to gag reels and I'll give you a shout out in my videos.
CSS Absolute vs Relative Position EXPLAINED!
Relative vs Absolute Cell Reference in Microsoft Excel - What's the difference?
Excel Cell Reference: Absolute, Relative or Mixed?
Absolute and Relative Paths
Absolute or relative URLs, which is better?
CSS Positioning: Position absolute and relative explained
Absolute vs. Relative URLs in links
Absolute Advantage vs. Comparative Advantage
What Is the Difference Between Absolute and Relative XPaths?
Absolute vs Relative URLs in HTML
In About a Minute: Relative vs. Absolute Dating
Gauge VS Absolute Pressure | Pressure Monitoring
What is the Difference between Absolute and Incremental Encoders?
Position absolute and responsive layouts
Relative Dating vs Absolute Dating (Updated)
Absolute vs relative positioning | CSS Tutorial | With Live Preview | CSS3 | 2017 Must Watch
Absolute vs Relative Location - Definition for Kids
Excel Relative vs Absolute Cell References
Relative and Absolute Paths - Linux Tutorial 7
Absolute Advantage and Comparative Advantage
🆕what Is absolute path and relative path in linux path top video
Absolute vs. Comparative Advantage in One Minute: Definitions, Explanation, Examples and Comparison
What is the Difference Between Relative and Absolute Paths
Relative vs Absolute risks: Why Relative Risks Are Misleading, and How To Communicate Absolute Risks
Комментарии