filmov
tv
Fusion 360 — What can you really do with the Sheet Metal — #LarsLive 85
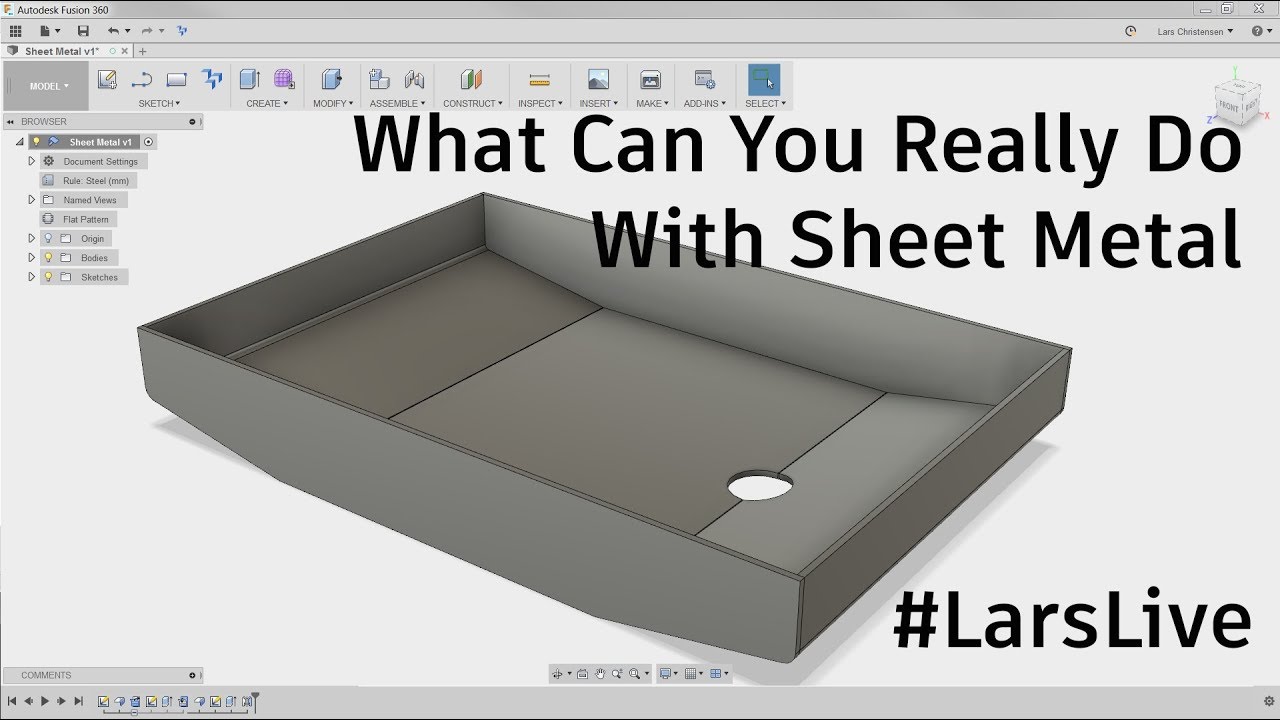
Показать описание
Live Stream — Time to go a little deeper into the sheet metal tools and see what you can do. This is Fusion 360 AND we will chat about your comments and questions.
Style: Casual
Time: About 15-30 minutes (We all have other things to do :-)
Understand K-Factor:
My email:
Want to learn more about Fusion 360? Check out this link:
Free CNC Handbook:
SUBSCRIBE!
LET'S CONNECT:
Style: Casual
Time: About 15-30 minutes (We all have other things to do :-)
Understand K-Factor:
My email:
Want to learn more about Fusion 360? Check out this link:
Free CNC Handbook:
SUBSCRIBE!
LET'S CONNECT:
Efficiency made SUPER easy using Fusion 360!
Solidworks vs fusion 360 which one is Better
What is Fusion 360?
Fusion 360 vs inventor which is Better
What is Fusion 360
Day 1 of Learn Fusion 360 in 30 Days for Complete Beginners! - 2023 EDITION
Fusion 360: Modelling a Coke Can
Fusion 360 VS Rhino, which is better
Autodesk Fusion 360 13 - Sketch Text (straight or on a curved path)
10 tips for Fusion 360 that I wish someone told me sooner.
What is Fusion 360
Bodies vs Components | Fusion 360 Core Concept
Getting Started with Fusion 360 Part 1 - BEGINNERS START HERE!
REAL ENGINEER tries Fusion 360 for the first time
Can't Stop Talking About Fusion 360 | Autodesk Fusion 360
3D Voronoi Studio for Autodesk® Fusion 360™ - Voronoi Vase Tutorial 3
Fusion 360 Tutorial for Absolute Beginners (2020)
Fusion 360 on Apple Silicon M1 MacBook Pro
How to use Fusion 360 with a Wacom pen
Autodesk Fusion 360 | Tutorial: Bodies vs Components
Intro to SHEET METAL in Fusion 360 - Sheet Metal Beginners Start Here!
Getting Started with Fusion 360 Part 2 - How to Create 3D SHAPES!
How to Sculpt in Fusion 360 | Beginner Concepts Explained
3D Scan: Repair and Modify in Fusion 360
Комментарии