filmov
tv
Easy Metal Casting - Pouring Liquid Pewter into a Silicone Mold
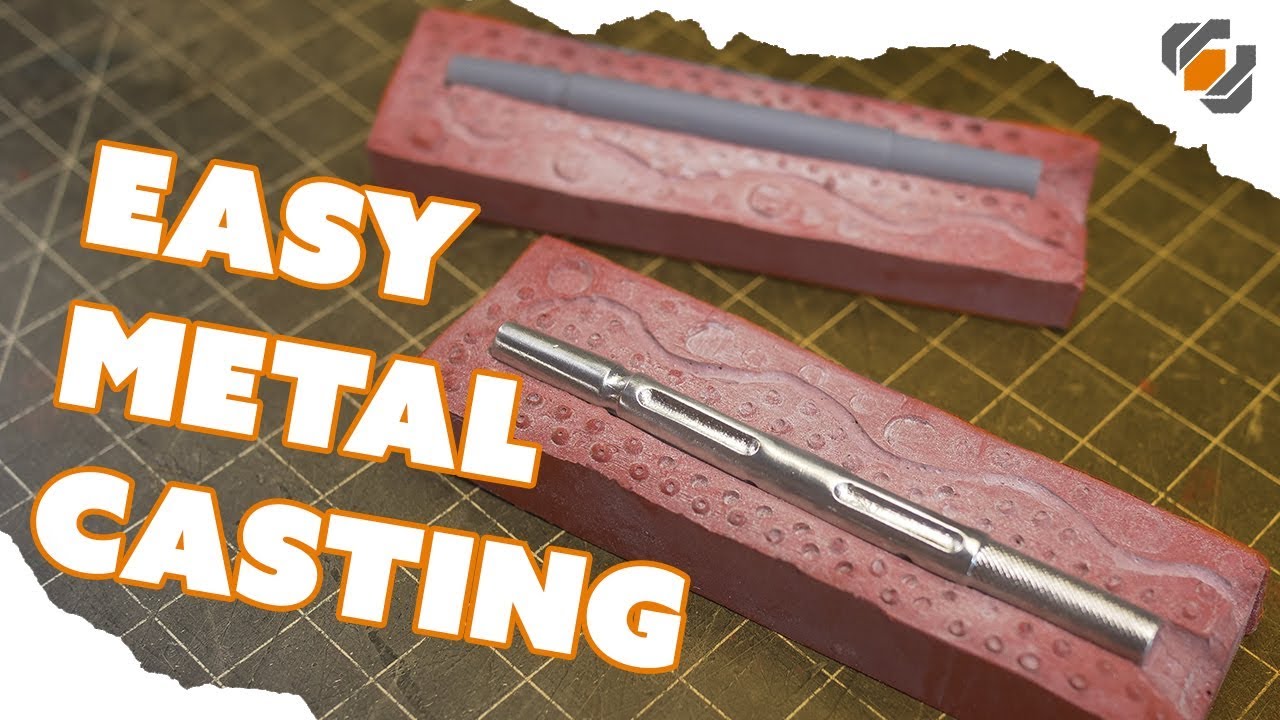
Показать описание
We've done pewter casting in the past, but we're really starting to get a lot better at it. Check out our new, improved techniques PLUS some testing with lower heat resistance silicone.
Links
RAC Props Blade Runner Kit Playlist
Original Kit by RAC Props
Tools & Materials
Mold Max 60 Heat Resistant Silicone - Amazon
Mold Max 30 - Amazon
Laser Thermometer - Amazon
Hot Plate/Burner - Amazon
Pewter Ingot - Amazon
123 Blocks - Amazon
Aluminum Tape - Amazon
Form 2 3D Printer - Formlabs
We release new videos every month!
Fun ways to help our channel:
Share your projects with us on twitter!
#PunishedProps
Links
RAC Props Blade Runner Kit Playlist
Original Kit by RAC Props
Tools & Materials
Mold Max 60 Heat Resistant Silicone - Amazon
Mold Max 30 - Amazon
Laser Thermometer - Amazon
Hot Plate/Burner - Amazon
Pewter Ingot - Amazon
123 Blocks - Amazon
Aluminum Tape - Amazon
Form 2 3D Printer - Formlabs
We release new videos every month!
Fun ways to help our channel:
Share your projects with us on twitter!
#PunishedProps
Easy Metal Casting - Pouring Liquid Pewter into a Silicone Mold
easy metal casting ,pouring liquid pewter into sand mold
Easy lost PLA metal casting │ How to turn a 3d print into metal │ ASMR
Casting Silver at Home (Easy DIY Jewelry)
How to Make a Free Aluminium Melting Furnace
Aluminium Casting Process||aluminium die casting metal pouring||Automobile Component Making Process
Pouring Molten Aluminum - Metal Casting at Home
Turn Styrofoam cups into METAL - Experimental metal Casting - Lost foam casting
I made my own SILVER COINS! - Making custom silver rounds - 3d printing to metal casting
Pouring molten metal inside a seashell - WHAT HAPPENS? - Experimental metal casting at home - DIY
Pouring Molten Aluminum - Metal Casting #shorts #youtubeshort #video
Metal Casting Play Sand - TKOR Shows You How To Make Green Sand, Sand Casting And More!
Craft of metal smelting and pouring in sand casting
Craft of aluminium metal smelting and pouring in sand casting
More aluminium pouring #sandcasting #furnace #diy #workshop #metalcasting #aluminium
Casting a Metal Mushroom - pouring Molten Aluminum - ASMR metal melting
Pouring Liquid Copper into Casting Molds #shorts #youtubeshorts
Pouring Molten Metal on Kinetic Sand - Casting Pewter
Molding & Casting Small Urethane Resin Parts with two part silicone molds
Pouring Molten Metal into Greensand Mold
Basics of Lost Wax Casting - Under 20 Minutes
Pouring Molten Metal on Kinetic Sand
Pouring Molten - Metal Casting
🔥Amazing Metal Casting😱🔥 #silver #pouring #melting
Комментарии