filmov
tv
Sierra Space’s LIFE Habitat Successfully Completes Ultimate Burst Pressure Test
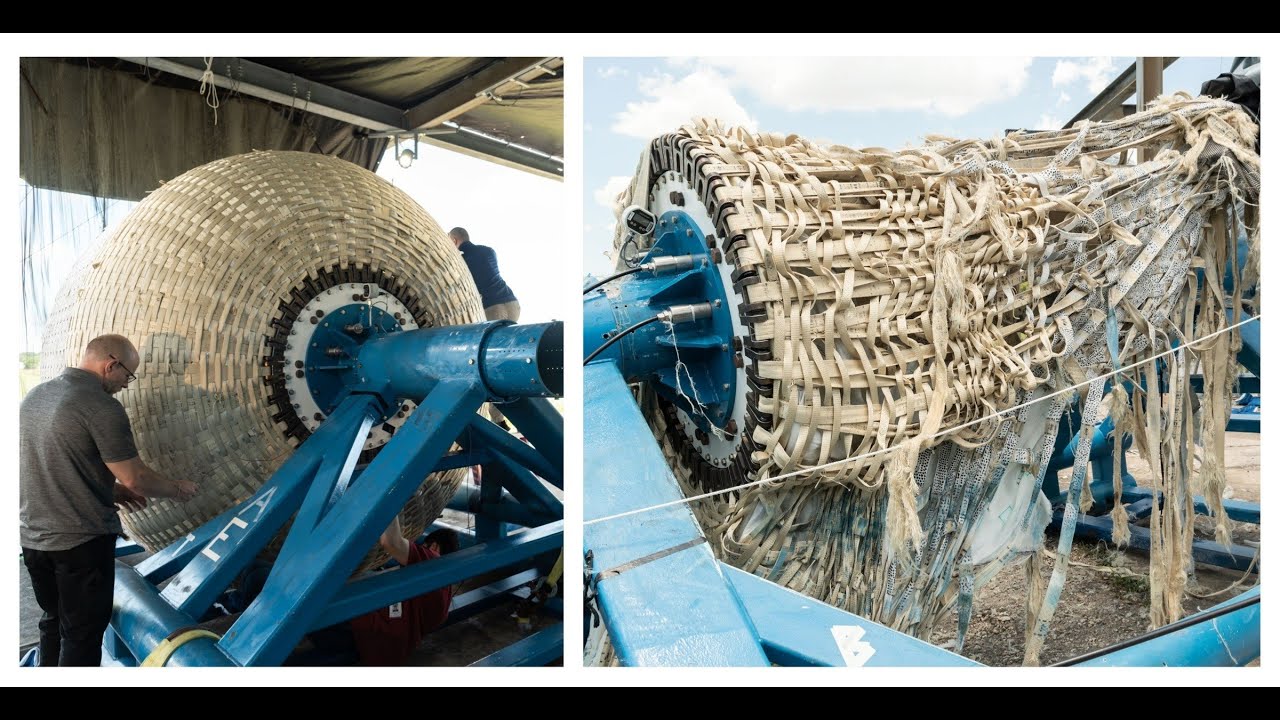
Показать описание
After successful completion of the Ultimate Burst Pressure Test with a one-third scale test article, Sierra Space becomes the only active commercial space company to meet threshold.
The test, which is the first of two sub-scale burst tests scheduled for 2022 in support of Sierra Space’s softgoods certification, used a one-third scale of Sierra Space’s LIFE inflatable habitat – which burst at 192 psi – exceeding the safety requirement of 182.4 psi. As a result, this stress test is among the highest publicly released data points for a softgoods UBP test at any scale.
Connect with us on Social Media:
The test, which is the first of two sub-scale burst tests scheduled for 2022 in support of Sierra Space’s softgoods certification, used a one-third scale of Sierra Space’s LIFE inflatable habitat – which burst at 192 psi – exceeding the safety requirement of 182.4 psi. As a result, this stress test is among the highest publicly released data points for a softgoods UBP test at any scale.
Connect with us on Social Media:
Reinventing the Space Station with LIFE Habitat
Sierra Space’s LIFE Habitat Successfully Completes Ultimate Burst Pressure Test
Sierra Space’s LIFE Habitat Successfully Completes Second Ultimate Burst Pressure Test
LIFE Habitat | Sierra Space Successfully Completes Month Long Creep Test
Sierra Space Has Begun Full-Scale LIFE Habitat Testing!
A Closer Look At The Inside of Sierra Space's LIFE Habitat
Full-scale Sierra Space inflatable habitat explained - Watch it burst in test!
World's First Commercial Space Station Design and Testing Questions Answered | LIFE Habitat Tec...
Sierra Space Is Working On An Even Bigger Inflatable Habitat
Inside Sierra Space's LIFE Habitat: Exploring the Future of Space Living with Giant Space Ballo...
Sierra Space Has Begun Full-Scale LIFE Habitat Testing!
LIFE Habitat | Successful Accelerated Systematic Creep Test for Extended Human Missions
Sierra Space Is About To Begin Full-Scale LIFE Habitat Testing!
Sierra Space Bursts Inflatable Life Habitat
Reasons to Believe | LIFE Habitat for Space Exploration
Sierra Space's LIFE Habitat Is Getting Close To Full-Scale Testing
Advancing Next-Gen Space Station Tech with Sierra Space and NASA
Sierra Space Intro - 30s
Life Inside An Inflatable Space Station!
Amazing! Sierra Space Blew Up its Inflatable Space Habitat
Dream Chaser Spaceplane CRS-2 Mission Profile
Sierra Space: Dreams Worth Chasing
Sierra Space Has Begun Full-Scale LIFE Habitat Testing!
The Real Reason Sierra Space Is About To Take Over
Комментарии