filmov
tv
Sharpening End Mills At Home (probably?) - Acute Tool Sharpener Conclusion
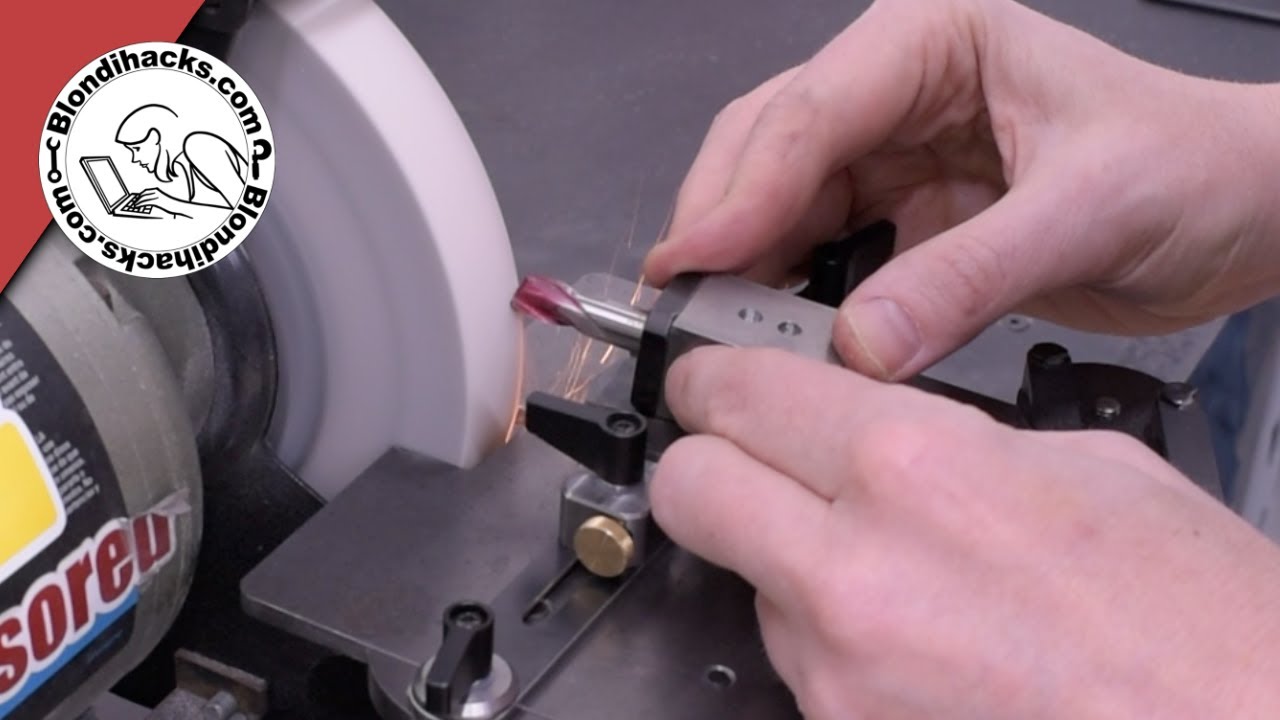
Показать описание
This episode on Blondihacks, I’m working on a tool sharpener! Exclusive videos, drawings, models & plans available on Patreon!
Official Eccentric Engineering videos for this system:
Here are links for many of the tools that you see me using:
(I earn small commissions on these links)
As an Amazon Associate, I earn from qualifying purchases.
Official Eccentric Engineering videos for this system:
Here are links for many of the tools that you see me using:
(I earn small commissions on these links)
As an Amazon Associate, I earn from qualifying purchases.
Sharpening End Mills At Home (probably?) - Acute Tool Sharpener Conclusion
Sharpening End Mills On The Lathe
End MIll End Sharpening, Made Easy
Sharpening the Flutes on a Milling Cutter
End Mill Sharpening Guide : Universal Tool & Cutter Grinder AKA D Bit Grinder
How to Sharpen End Mills on a Surface Grinder Part 1
Cutter Grinder + End Mill Grinder
Endmill Sharpening
How to grind the end mill? Use a end mill sharpener, easy work, fast and accurate
Carbide End Mill sharpening with a DIY sharpening jig.. ok Tony, fixture.
End Mill Sharpening
simple end mill bit sharpening
End mill sharpening first time
End Mill Sharpening
How to Sharpen an End Mill Cutter
How to Sharpening End Mills
End mill sharpening set up 3
How to Sharpen End Mills
End mill sharpening set up 1
How end mill sharpener work?Let us show you!
Homemade Endmill &Slitting saw sharpener
Sharpening end mill cutter using portable grinder
End mill sharpening fixture.
guy sharpening an endmill on tool sharpener with treadmill motor on it
Комментарии