filmov
tv
EEVblog #1353 - WHY Are These Pins Shorted?
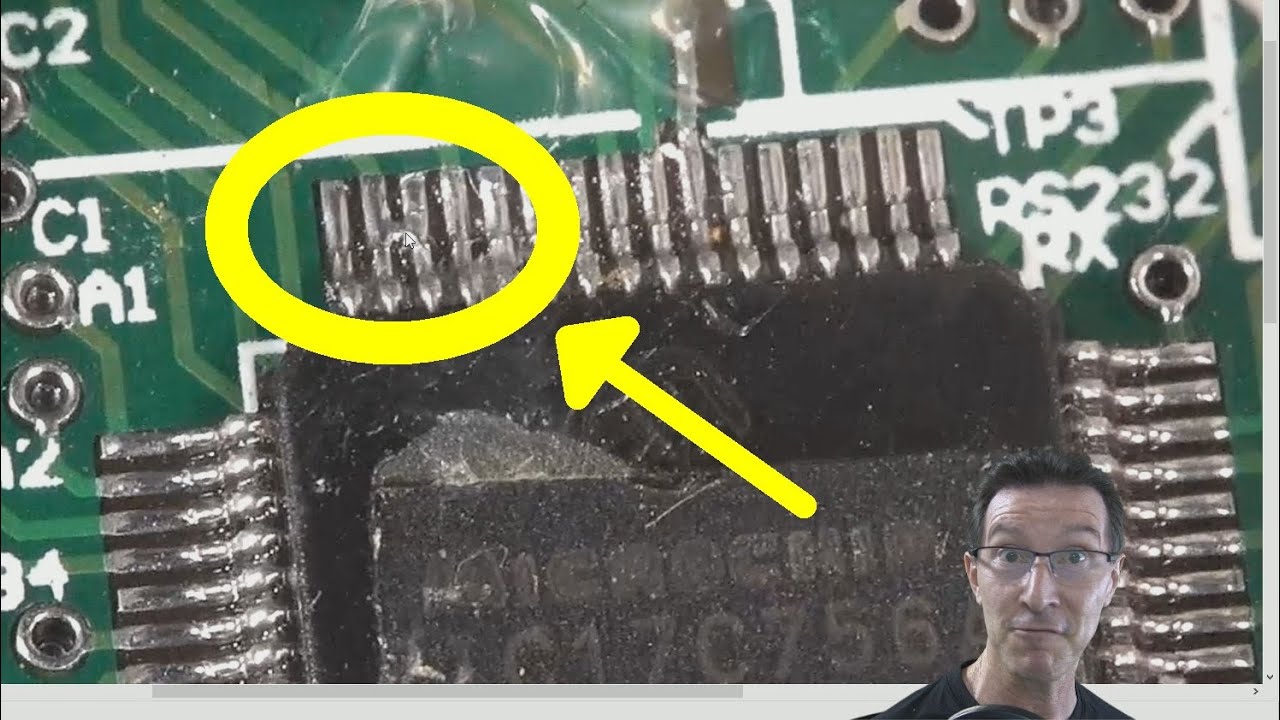
Показать описание
Eagle eyed viewers spotted a short between two pins on a TQFP chip in the previous teardown video. This isn't a dodgy assembly issue, it's a deliberate design short, Dave explains how and why.
Solder masks and snap grids.
Buy anything through that link and Dave gets a commission at no cost to you.
Donate With Bitcoin & Other Crypto Currencies!
#PCBdesign #Manufacture #Soldering
Solder masks and snap grids.
Buy anything through that link and Dave gets a commission at no cost to you.
Donate With Bitcoin & Other Crypto Currencies!
#PCBdesign #Manufacture #Soldering
EEVblog #1353 - WHY Are These Pins Shorted?
EEVblog #1355 - NEW Siglent SDS1104X-U $399 4CH Oscilloscope Teardown
EEVblog #1370 - Kindle Paperwhite REPAIR
EEVblog #1347 - SMD Thermal Jumpers could be GAME CHANGING!
EEVblog #1369 - Xiaomi Mi Air Wireless Charging BUSTED!
EEVblog #1371 - A 10,000hr Battery Life Bench Multimeter?
EEVblog #1359 - My SUPER PORTABLE Vlogging Kit!
EEVblog #1367 - 5 Types of Oscilloscope Passive Probes COMPARED
EEVblog #1357 - Dumpster Diving Santa PC
EEVblog #1151 - Dumpster Dive Yamaha Receiver
EEVblog #1348 - World's First IBM Compatible PC - The Compaq Portable
EEVblog #1350 - Fake Energizer Batteries?
EEVblog #1365 - Viewer PCB & Circuit Design Review
EEVblog #1285 - How to do Design By Inspection
EEVblog #1123 - EEVblog Meetup 2 Electric Boogaloo
EEVblog #1354 - Compaq Portable Repair - Part 2
EEVblog #254 - KiCAD PCB First Impressions
EEVblog #1343 - DEAD Deck Cree LED's
EEVblog #1351 - Mailbag
Home Solar Upgrade Power Consumption
EEVblog #1361 - Dodgy Tactile Switch TEARDOWN
Dumpster Diving 27' iMac Upgrade
EEVblog #1349 - Energizer Battery Leakage - MADE IN USA!
#1353 HP 3465B Multimeter Repair (part 3 of 3)
Комментарии