filmov
tv
Supplies 101: Tailoring and Historical Sewing
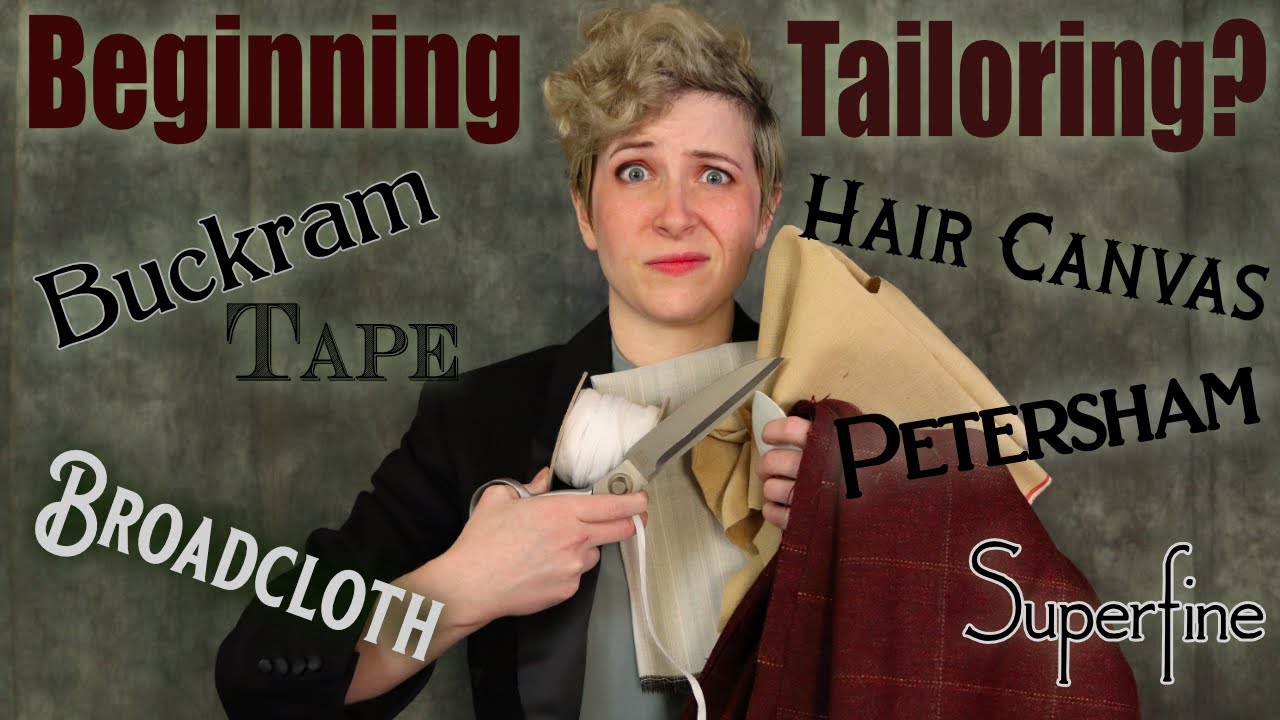
Показать описание
Let's talk tailoring supplies! With all of the weird terms floating around, how do we know what to use where? What weight of wool for a jacket? What type of interfacing for a waistcoat? Is tailors tape the same as twill tape? Do shoulder pads always look like linebackers? The questions seem endless! So, we're going to start today with understanding what some of the basic supplies you'll come across actually look like.
00:00 Intro
01:25 Interfacings
07:58 Padding
10:34 Tapes
13:08 Linings
15:41 Wools
21:40 Threads
24:36 Tools
More fabric/tailoring shops:
00:00 Intro
01:25 Interfacings
07:58 Padding
10:34 Tapes
13:08 Linings
15:41 Wools
21:40 Threads
24:36 Tools
More fabric/tailoring shops:
Supplies 101: Tailoring and Historical Sewing
Linen Fabric 101: Supplies for Sewing
Wool Fabric 101: Supplies for Sewing
Cotton Fabric 101: Supplies for Sewing
Silk Fabric 101: Supplies for Sewing
Tailoring 101: Basic sewing tools and equipment's for beginners
Tailoring 101 with Victorian Waistcoats
10 Essential Sewing Tools to Make Historical Fashion
My best kept sewing pattern secret!
How I make my sewing patterns #sewing #shorts
How to Cut Darts on Paper Patterns | Sewing tips and tricks
NEW CLASS! Hand Sewing Level II: Common Stitches & Where to Use Them
Secrets of a Professional Historical Tailor ft. Tom van het Hof
Pressing: The Tailor's Secret to Perfect Seams | Masterclass feat. Barbara of Royal Black
Don't Skip Learning These Historical Sewing Techniques
everything I made while sewing for 24 hours STRAIGHT
Sewing Tips And Tricks For Beginners
I really like SEWING! #shorts #sewing
A Brief History of Sewing Supplies
All About Fabric: Supplies for Sewing
Learning About Fabrics 1: The Who, What, and How
The War Within 1-100 Tailoring Guide
The Surprising Genius of Sewing Machines
7 MUST-KNOW Hand Sewing Stitches for Historical Fashion
Комментарии