filmov
tv
The Logistics of Natural Gas
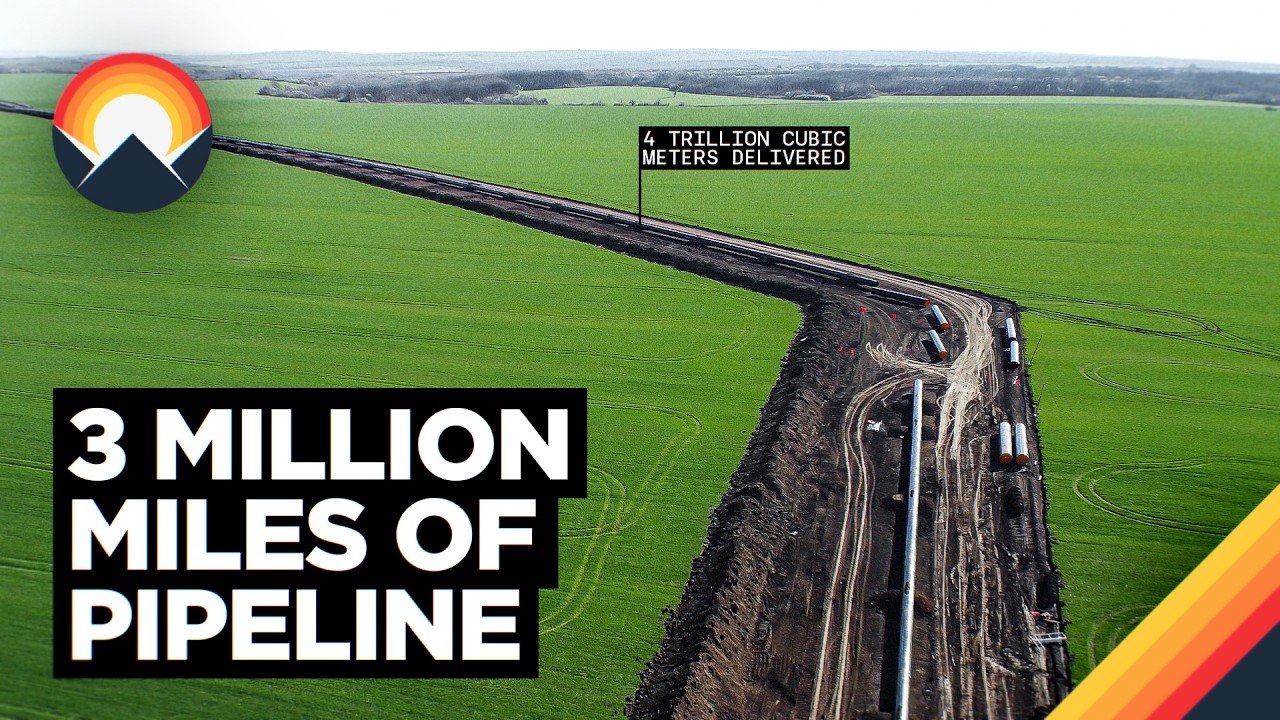
Показать описание
Writing by Sam Denby and Tristan Purdy
Editing by Alexander Williard
Animation led by Max Moser
Sound by Graham Haerther
Thumbnail by Simon Buckmaster
The Logistics of Natural Gas
Natural Gas 101
Natural Gas Logistics
Gas supply in Europe: Gas Logistics & Transport
Liquified Natural Gas: From Treatment To Transport | ExxonMobil
How GAS PIPELINES and Compressor Plants work, maintenance with Smart Pig
The Logistics of Natural Gas | Engineer Empire Reacts
Why LNG is the Future of Shipping: The Natural Gas vs Diesel Debate
Gagavuzlar, Moldova, 3 Deniz Girişimi ve Karadeniz’de Yeni İstikrarsızlık Cepheleri - Cem GÜRDENİZ...
Oil & Gas Supply Chain | Oil and Gas
How LNG Carriers (Gas Tankers) Work - Design Types, Loading & Discharge
LNG / Liquefied Natural Gas | LONG HAUL TRUCK | 🟢 Line | Alternate ⛽ | This NOT ❌CNG TANK | Pov |...
Battling Pipelines: Inside A Family's Fight For Their Home | AJ+
Gas supply in Europe: Liquefied Natural Gas (LNG)
Oil and Gas - Supply Chain and Logistics
Pipelines for Beginners - How does an oil pipeline work?
Why Natural Gas Tankers Are Lining Up Off Europe's Coast | WSJ
Transportation Options: Natural Gas
Powering Our Supply Chain with Natural Gas
Optimizing LNG Operations - Liquefied Natural Gas | DELMIA
Animated map of the major oil and gas pipelines in the US
The Hidden Value of LNG - Liquefied Natural Gas | DELMIA
'LNG Carriers: Powering the Future of Energy | Hartford International Logistics & Services&...
The Impact of LNG as Fuel on Shipping: Cost vs. Emissions
Комментарии