filmov
tv
EEVblog #440 - Atten PPS3205T-3S Triple Output Power Supply Teardown
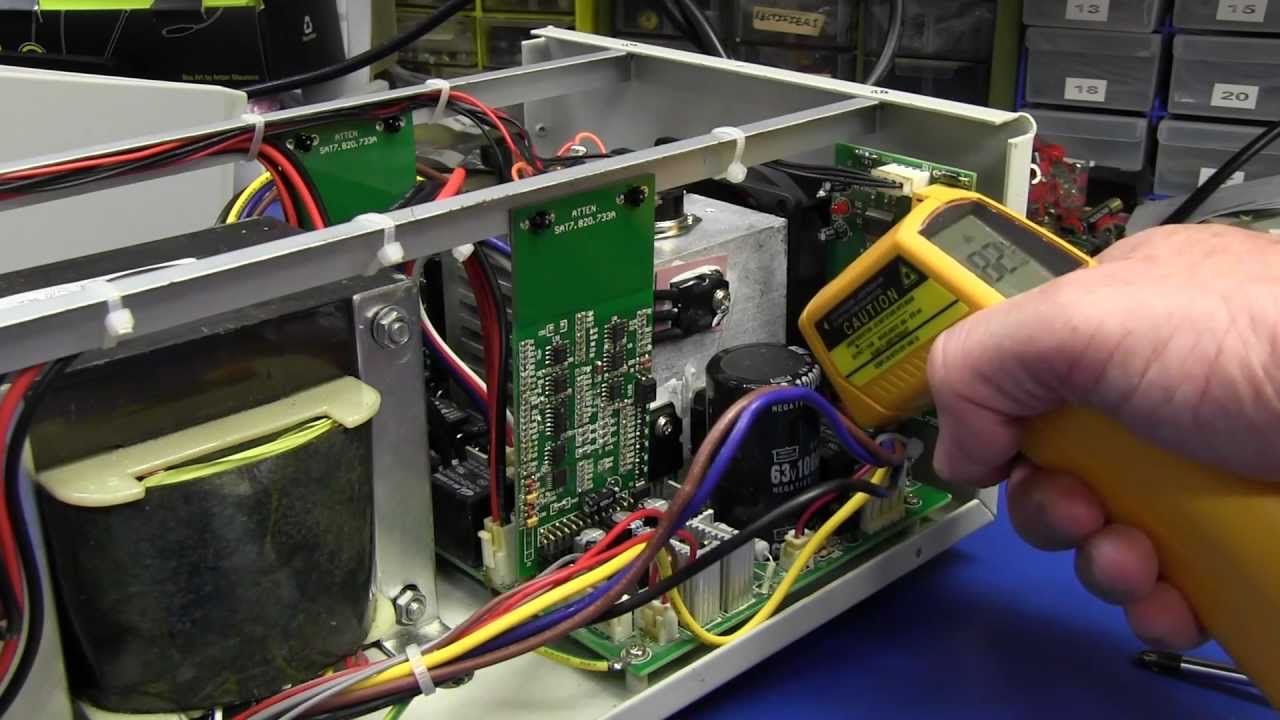
Показать описание
Inside the Atten PPS3205T-3S 3 output precision laboratory bench power supply.
EEVblog Main Web Site:
EEVblog Amazon Store:
Donations:
Projects:
Electronics Info Wiki:
EEVblog Main Web Site:
EEVblog Amazon Store:
Donations:
Projects:
Electronics Info Wiki:
EEVblog #440 - Atten PPS3205T-3S Triple Output Power Supply Teardown
EEVblog #439 - Atten PPS3205T-3S Triple Output Power Supply Review
EEVblog #540 - HP35670A DSA Repair - Part 3
EEVblog #272 - Manson 9400 40A 3-15V Switchmode PSU Teardown
EEVblog #166 - HP Agilent E3610A Lab Power Supply
EEVblog #449 - Absopulse VFC500 Variable Frequency Converter Teardown
EEVBlog - Bits und so #451
EEVblog #828 - Siglent SPD3303X Precision Lab PSU Teardown
Atten PPS3005S DC Power Supply Fix
EEVblog #357 - USB Supply Power-up Testing
EEVblog #404 - Korad PSU Followup
EEVblog #400 - 400th Live Show
EEVblog #649 - Power Designs 2005 PSU Teardown
EEVblog #445 - Fluke Contest Draw
EEVblog #435 - 3D Rocker Teardown
KORAD KA3305D Digital control dc power supply psu teardown + failure + troubleshoot
EEVblog #511 - Rigol DP832 Power Supply Teardown
EEVblog #814 - Keysight N8762A 600V 5100W PSU Teardown
EEVblog #509 - Rigol DP832 Lab Power Supply
EEVblog #419 - Thermocouple Tutorial
ITECH IT6322 Triple-power supply review
Breaking Down Medical Equipment Part 1 - ASMR - Scrap Breakdown - Recycling
BK Precision 0-30v 3amp Bench DC Power Supply Review
Club Jameco Dual Adjustable Power Supply Kit
Комментарии