filmov
tv
Torsen Differential, How it works ?
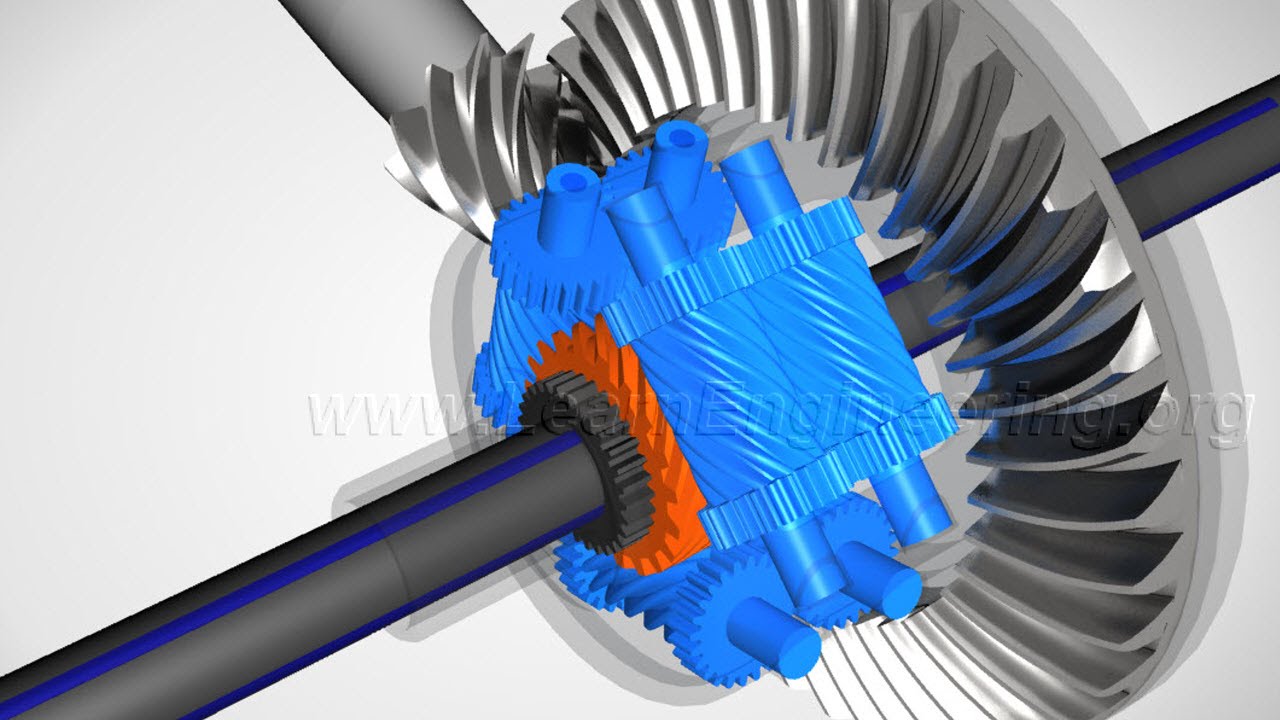
Показать описание
The working of Torsen differential is elaborately explained in this video with help of animation.
Torsen Differential, How it works ?
What's a Torsen limited slip differential?
Torsen differential working with video tutorial
Torsen Limited Slip Differential - Explained
TORSEN vs OPEN DIFFERENTIAL - TORQUE SPLIT simplified animation model
Kenny's Thoughts on Torsen Differentials
16. Torsen differential || how does a gearbox work
How a Differential Works | Types of Differentials Explained
Miata Torsen T-2 limited slip differential assembling
What's a Torsen™ differential? Why is it so cool? #shorts
Diferencial Torsen (Autoblocante) / Self-locking Torsen Differential
How it works TORSEN DIFFERENTIAL || Design 3D || Library
Understanding Limited Slip Differential
Audi Torsen differential - technical animation
Torque Vectoring Differential - Explained
torsen differential full animation
TORSEN DIFFERENTIAL || DISADVANTAGE || ADVANTAGE || WORKING ||
DIFFERENTIALS | How They Work
Differential | How does it work?
Open diff VS LSD conversion set by RacingDiffs | BMW Z4 donuts
Torsen T1 - Torque Bias Ratio test rig
Difference Between Limited Slip Differential And Torsen Differential?
Torsen vs standard differential from LEGO - explained
Audi quattro AWD DIFFERENCES - Torsen vs Centre Differential vs Haldex vs Ultra
Комментарии