filmov
tv
Nickel Electroplating in the Home Shop - A Shocking Way to Prevent Rust!
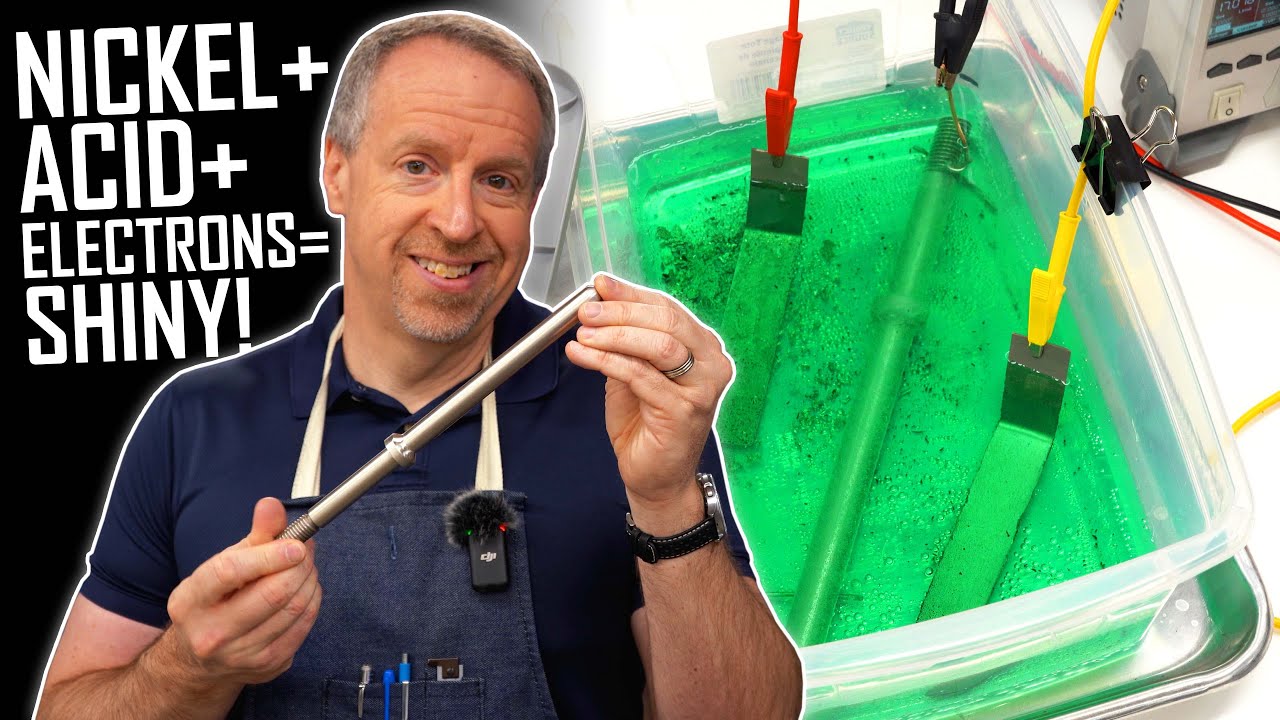
Показать описание
Today, we're trying out nickel electroplating for the first time in the home shop. We're going to nickel plate the mild steel rack storage pins we made in a previous video so they won't rust, tarnish, or corrode in the coming years. Nickel Electroplating turns out to be a very simple process, involving vinegar, salt, nickel, and electricity. For a total amateur, it turned out great.
Tools used in this video:
*This site contains affiliate links for which I may be compensated
00:00 Intro
01:18 What is electroplating?
02:18 Making the nickel acetate solution
06:29 Test plating a wire
07:58 Preparing parts for plating
08:54 Electroplating steel parts
10:11 Initial results
11:26 Buffing the plated parts
12:11 Examining the results
12:57 Conclusions
Licensed under Creative Commons: By Attribution 3.0 License
Tools used in this video:
*This site contains affiliate links for which I may be compensated
00:00 Intro
01:18 What is electroplating?
02:18 Making the nickel acetate solution
06:29 Test plating a wire
07:58 Preparing parts for plating
08:54 Electroplating steel parts
10:11 Initial results
11:26 Buffing the plated parts
12:11 Examining the results
12:57 Conclusions
Licensed under Creative Commons: By Attribution 3.0 License
Nickel Electroplating in the Home Shop - A Shocking Way to Prevent Rust!
Nickel Electroplating Steel In The Home Workshop
How to Nickel Electroplate at Home | bit-tech Modding
Electroplating - Easy DIY Nickel, Copper, Zinc Plating
How to: Make A Nickel Plating Solution At Home … It’s Easy!
Copper Plating At Home / Electroplating of Copper / Easy Copper Plating Process #shorts
Nickel Plating - Step by step guide
Simple Nickel Plating Set Up Final cut
DIY electroplating - Bright nickel plating at home
How to: Nickel Plating At Home…. How Easy!
Easy nickel plating on metal
Acid copper plating technology
How to nickel plate at home - a detailed DIY guide to simple electroplating restoration.
Simple electroless nickel plating process, bright coating#electroplating #electroplated #nickel
Easy DIY Nickel Electroplating - Electro Plating Made Easy
⚡ Nickel plating at home ⚡
Electroless nickel plating process for cast iron#electroplating #plating #nickel #plating
Easy DIY Nickel Plating - Electroplating setup for beginners - nickel plating at home
Nickel Plating at Home - Easy Electrolysis & Electroplating
Can you electroless nickel plating
Ni 117 Nickel Plating Brightener
Electroless nickel plating process that can be produced at home.#electrolessnickelplating
Black electroless nickel plating on stainless steel#shorts #stainlesssteel #nickel #electroplating
Straight up nickel plating process for iron and steel parts, 5 minutes quick light Ni-809
Комментарии