filmov
tv
Testing the BIG Boring Bar | Shop Made Tools
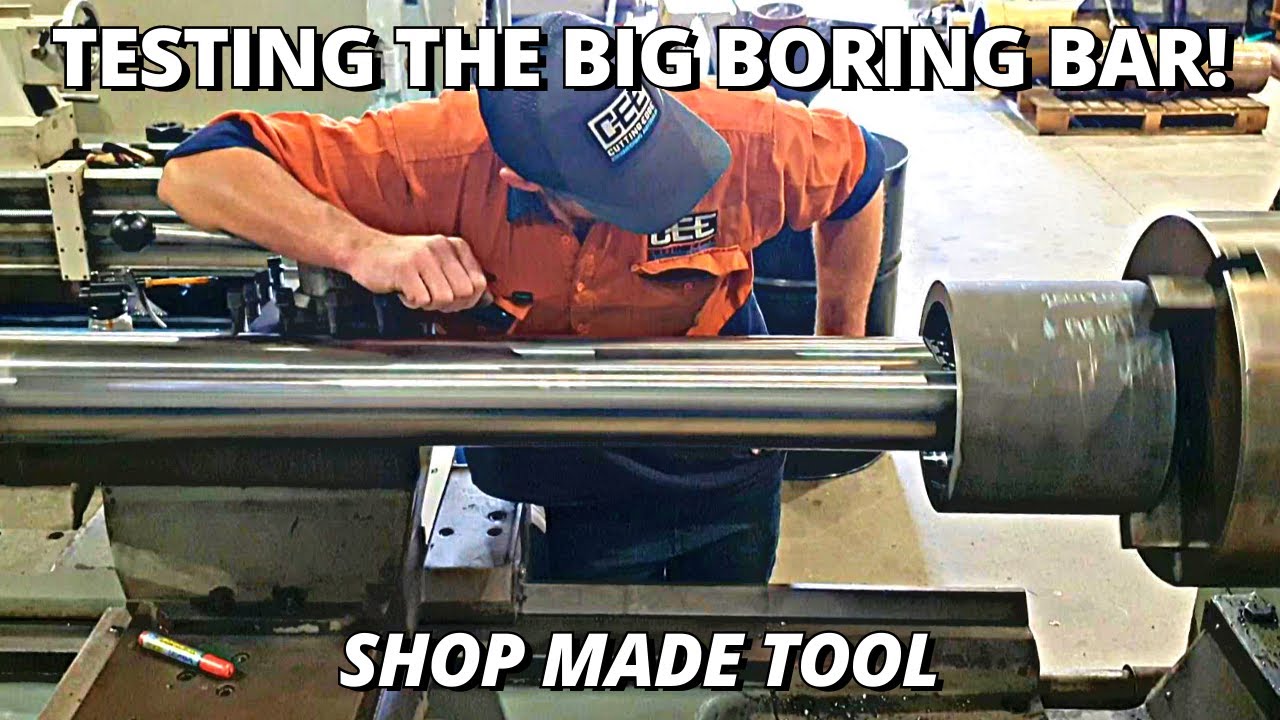
Показать описание
In this video we are using:
- LZMT CW6280D Lathe
In this video we are using:
- TM-26120G Centre Lathe
- WIA 500i Weldmatic welder
- HMP-150T Hydraulic press
- BM-63VE Milling machine
Join our channel:
To see more follow us on online here:
Check out our AMAZON store and explore our favourite finds that we use in the workshop:
About Us:
Our channel is all about showing you real life machining work from our workshop on the Gold Coast Australia. We specialize in manual machining, hydraulic repairs and heavy fabrication for the earth moving, mining and civil construction industries. So if you're a machinist that wants to see some big gear in action be sure to subscribe to our channel right now. We upload new videos every week that show lathe machining, milling, welding and all the good stuff that comes from a machining workshop. If that sounds like something that you would enjoy seeing, then make sure to join us by subscribing!
#australianmachinist #shopmadetools #machinist
Комментарии