filmov
tv
Investigation on air compressor blow up
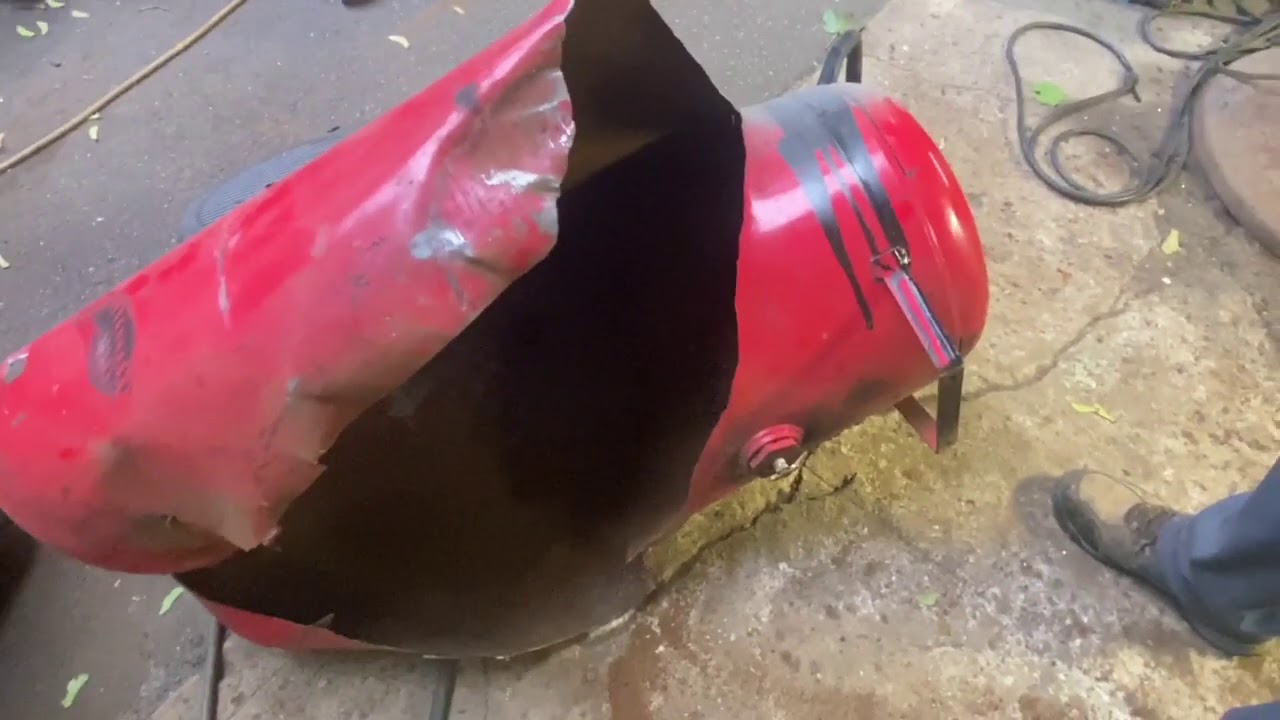
Показать описание
Investigation on air compressor blow up
100 Gallon Air Compressor Takes Flight, Breaks Through Roof Of Denver Home
*AIR COMPRESSOR WARNING*
Khalis made the air compresser blow up!
Blowing up pop bottle with air compressor
Home Air compressor explosion, Blow up, DANGER
En rangeant l’atelier le compresseur explose comme nous !🤣🤣
EPIC ball explosion from Milwaukee air compressor!!!
Air Compressor Explosion Prevention. Hydro Test.
Blown fuse again # 88
air compressor failure.
Air compressor vs bottle making a huge explosion! 💣😂
#diy dropping the air compressor 🥵🥵🤬
How to Hook Up an Air Compressor Hose #shorts
Air compressor motor blow out
Accident (compressor)😱😱 #shorts #safetyfirst
HARBOR FREIGHT COMPRESSOR CRAZY EXPLOSION issues
Compressor rust clean
Air compressor failure
BLOWN Compressor On Our Mercury Optimax Pro XS - Disassembling compressor to investigate
Tank Safety, This video may SAVE YOUR LIFE!
EXPERIMENT: AIR COMPRESSOR VS BOTTLE IN SLOW MOTION 120 FPS
Using Fluke Meter to Test Air Compressor Motor Capacitors & opening up my SIP One Way Check valv...
Man narrowly escapes washing machine explosion caused by charger
Комментарии