filmov
tv
Machining Hot Rolled VS Cold Rolled Steel
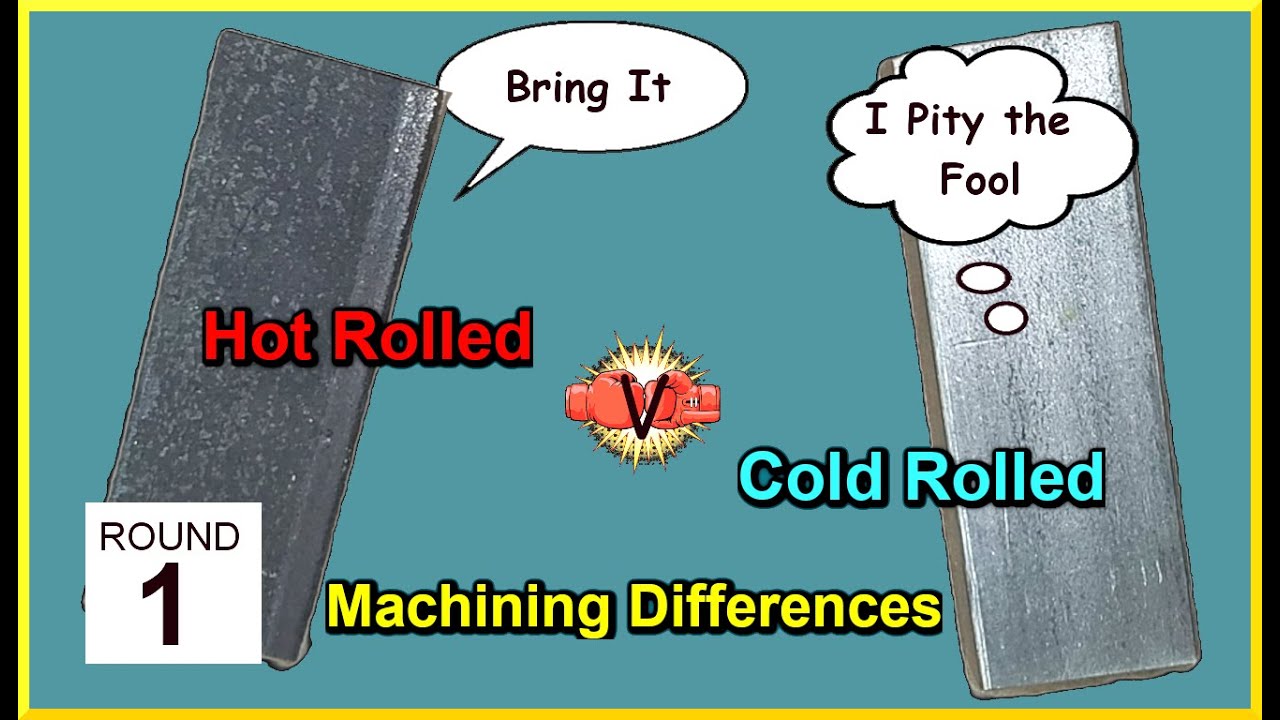
Показать описание
A simple comparison of how 1018 Cold Rolled Steel and 1020 Hot Rolled Steel behave when machining.
Machining Hot Rolled VS Cold Rolled Steel
Cold Roll vs Hot Roll
Cold Rolled Steel | Cold Rolling vs Hot Rolling | Hot Rolled Steel
Hot Rolled Steel Coil Facts #shorts
A Few Things You Should Know About Cold-Rolled Steel
Explore The Extremely Large Capacity Hot-Rolling Mill | Producing Steel Coil And Rebar
What is the difference between cold rolled and cold finished steel?
Machining Cold Rolled Steel, Precision Headaches Guaranteed!
What is the most cold-rolled steel type used in your projects?
How STEEL is Made - From Dirt to Molten Metal
The main process of Cold Rolling production -- Part A
Hot Rolled vs Cold Rolled Steel
Do you know the difference between cold rolled steel and hot rolled steel?
Do you know the manufacturing process of cold rolled strip steel?
More than 5m long, 1 ton of strip steel making process technology !#process #technology #strip #seel
Seamless steel in stock/what's the difference of the hot rolled and cold drawn
steel plate hot rolled and cold rolled
Fully Automatic Small Slitting Machine Galvanized Cold Rolled
hot forging roller #bolt #zhongqiaotech.com # roller mill #hot forging mill .
Hot Rolled Steel/Cold Rolled Steel
How is cold rolled steel plate produced?
Cold Rolled Steel Plate Manufacturing
Cold rolled sheet rolling process#shorts #steel
After the hot-rolled slab is rolled, the final step is coiling
Комментарии