filmov
tv
Making a 3D Printed Harmonic Drive Using a Timing Belt
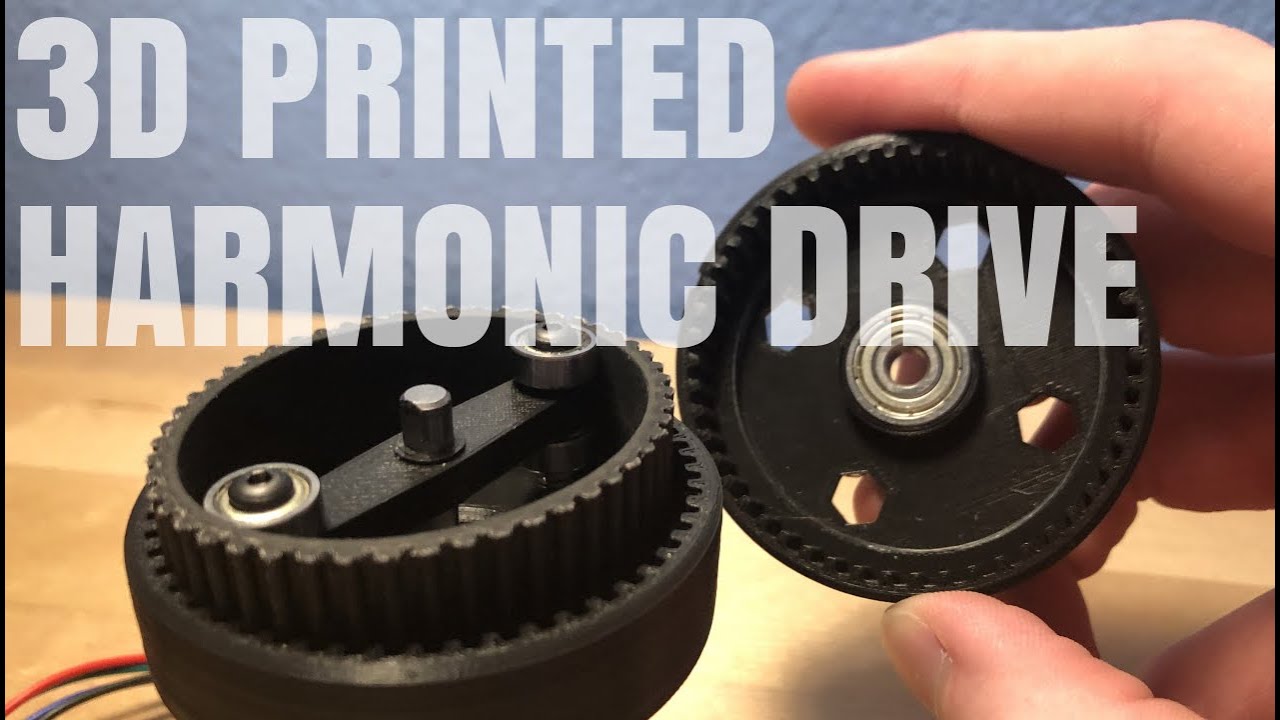
Показать описание
A harmonic drive reduces the RPMs of a motor output shaft and increases the torque proportionally. I created a proof-of-concept harmonic drive using 3D printed parts and a small, closed-loop timing belt.
Disclaimer: I may earn an affiliate commission when items are bought through these links.
Disclaimer: I may earn an affiliate commission when items are bought through these links.
My 3D Printed Harmonic Drive is Surprisingly Powerful!
Compliant Harmonic Drive (3D Printed)
Nema17, 3D Printed Strain Wave Gear (Harmonic Drive)
Harmonic vs Cycloidal Drive - Torque, Backlash and Wear Test
DIY 3D Printed Harmonic Drive (Strain Wave Gearing)
Integrating My Harmonic Drive - 3D Printed 6-Axis Robot Arm
Making a 3D Printed Harmonic Drive Using a Timing Belt
Experimental Harmonic Drive Reducer - 3D Printed
3d printed harmonic drive Wave Generator
3D Printed Harmonic Drive
Nema23, 3D Printed Strain Wave Gear (Harmonic Drive)
Keen-One EQ with modified harmonic drive
Testing a 3D Printed Harmonic Drive till it BREAKS
Inversed Timing Belt transmission
Low profile, 3D printed harmonic drive/strain wave reduction.
Failed 3D printed NEMA17 harmonic drive
3D Printed Harmonic Drive
3D Printed Strain Wave Gear
3D printed Harmonic drive built into a ball bearing
3D Printed - Harmonic Drive
CNC Machined vs 3D Printed Cycloidal Drive
3D printed high torque harmonic drive - strain wave gearbox
3D printed harmonic drive designed by Laplase
3D Printed Planetary Cycloidal Hub Gearbox. How far can it drive?
Комментарии