filmov
tv
HOW TO MACHINE A STEAM ENGINE FLYWHEEL - MODEL ENGINEERING FOR BEGINNERS #7
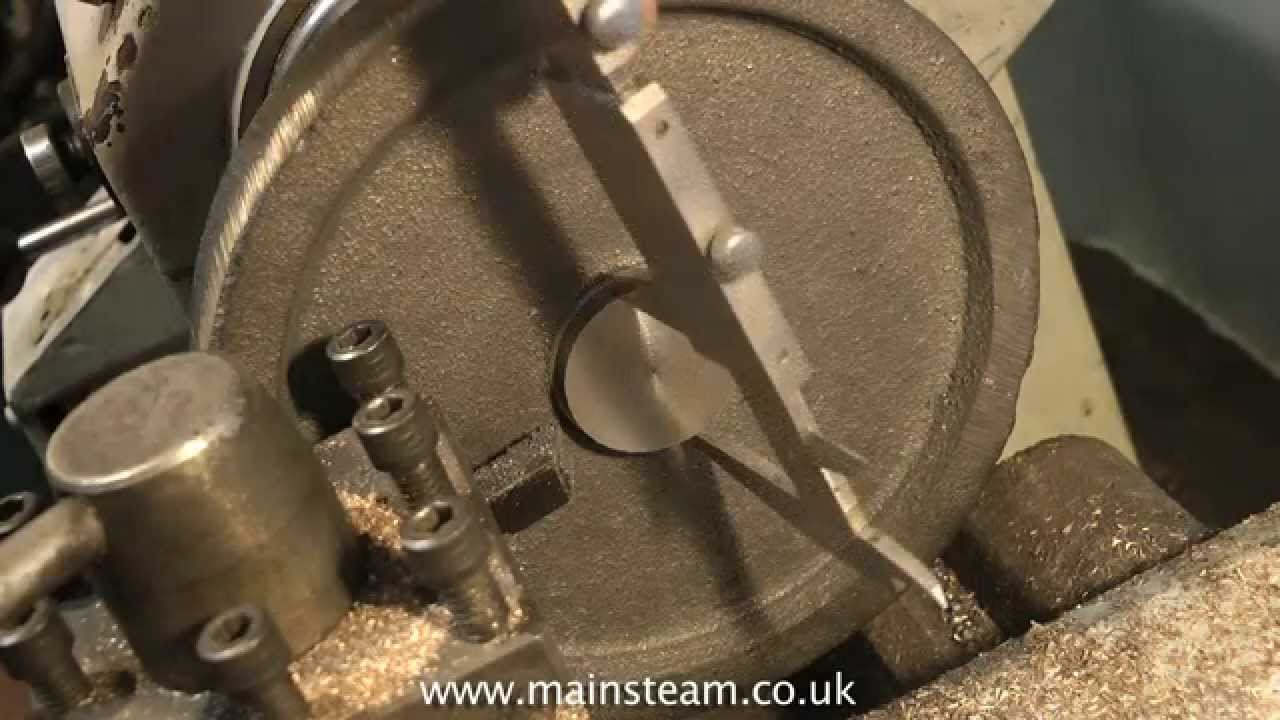
Показать описание
Model Engineering For Beginners #7 shows a quick & easy method to machine a steam engine flywheel.
How to make a steam engine from a car shock absorber
Let's Build A Model Steam Engine - Machining a cylinder casting!
Overtaking with a steam engine.
HOW TO MACHINE A STEAM ENGINE CYLINDER - MODEL ENGINEERING FOR BEGINNERS #5
Steam Engine - How Does It Work
How Does a Steam Engines Work? | Earth Science
Main Cylinder Machining! Big Steam Engine Build, Part 6
What’s Inside Valve’s Prototype STEAM Console?
The BEST Multi-purpose cleaning tool, steam cleaner, #howto #clean #best way.
HOW TO MACHINE A STEAM ENGINE FLYWHEEL - MODEL ENGINEERING FOR BEGINNERS #7
Wir bauen unsere eigene Steam Machine!
Making a Simple Steam Engine
Making Model Steam Engine Castings in the Home Workshop
How Do Steam Locomotives Work - Steam Engines Explained
Let's Build a Model Steam Engine - Machining a Piston!
Make YOUR own STEAM MACHINE in 2024
Historic Threshing Machine powered by Steam Engine
Come and own your own Stirling engine model!#steam #enginemodel #automobile
Machining a Model Steam Engine Cylinder - Part 1
Testing a TWIN & TRIPLE Steam Engine!
Most Common Milk steaming Mistakes/ How to perfectly steam milk for latte art
Have you ever seen a steam engine!
Working of Steam Engine |Animation
Wow🔥💨 #engine #steam #coal #fire #water #machine #short #shorts #shortvideo #youtubeshorts #power...
Комментарии