filmov
tv
Making real Carbon Fiber parts (at home)!
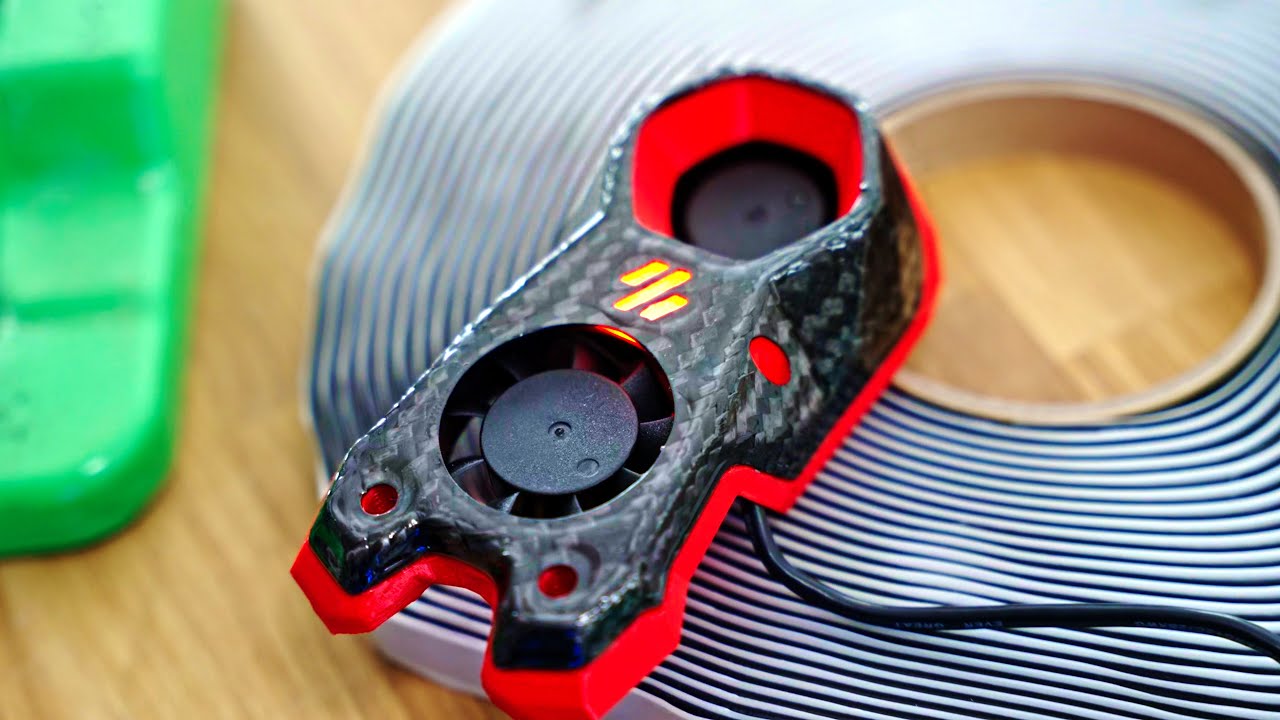
Показать описание
I'm upgrading my Voron - with carbon fiber! The Stealthburner toolhead has never looked better.
Product links are affiliate links - I may earn a commission on qualifying purchases (at no extra cost to you)
Product links are affiliate links - I may earn a commission on qualifying purchases (at no extra cost to you)
Making real Carbon Fiber parts (at home)!
CHEAPEST way to make CARBON FIBER. No specialist tools. Hand laminating [DIY] EPOXY RESIN
How to make DIY carbon fiber parts at home with wet lay
Making Forged Carbon Fiber Parts
How to make a carbon fiber part in under 1 minute.
100% Real Carbon Fibre (Fiber) KTM Brake Pump Cover
How Carbon Fiber is Made in Factories | HOW IT'S MADE
Difference between WET carbon (1) and DRY carbon fiber (2)
BMW X5 F15, F85 M Carbon fiber center console trim from NVD Autosport #nvdautosport #bmw #carbon
Making carbon fiber parts at home
How to Make a Carbon Fiber Part - Disc Brake Cover for HONDA motorcycle
DIY Carbon Fiber Skinning: Make Custom Motorcycle Parts for less!
Tow to Make Real Carbon Fiber Trim for BMW e90
Making a Mold of a Plastic Part to Turn Into Carbon Fiber- step by step
Composites Basics | Make Your Own Carbon Fiber Parts NOW!
How to Make Carbon Fiber Parts (Including the Mold)
Make Forged Carbon Fibre Parts Using Compression Moulding
HOW TO DO REAL CARBON FIBER ON BMW TRIM - PART 1 - BMW E90 335 TRIM IN RED REFLECTIVE CARBON
Make Professional Quality Carbon Fibre Parts Using Resin Infusion
Using 3D Printers To Build A Car Out Of Carbon Fiber | Part 1 | The Legacy (11)
How to make a Carbon Fibre cover. OFFSET MOULD Using Sheetwax (Carbon Fiber)
Carbon Fibre Reinforcement Weights and Weaves Explained
Making Complex Carbon Fibre Tubes Using a Split-Mould
MAKE YOUR OWN Race Car Parts | Carbon Fiber DIY KIT
Комментарии