filmov
tv
The EASIEST and CHEAPEST way to build with aluminium extrusion - Acrobot
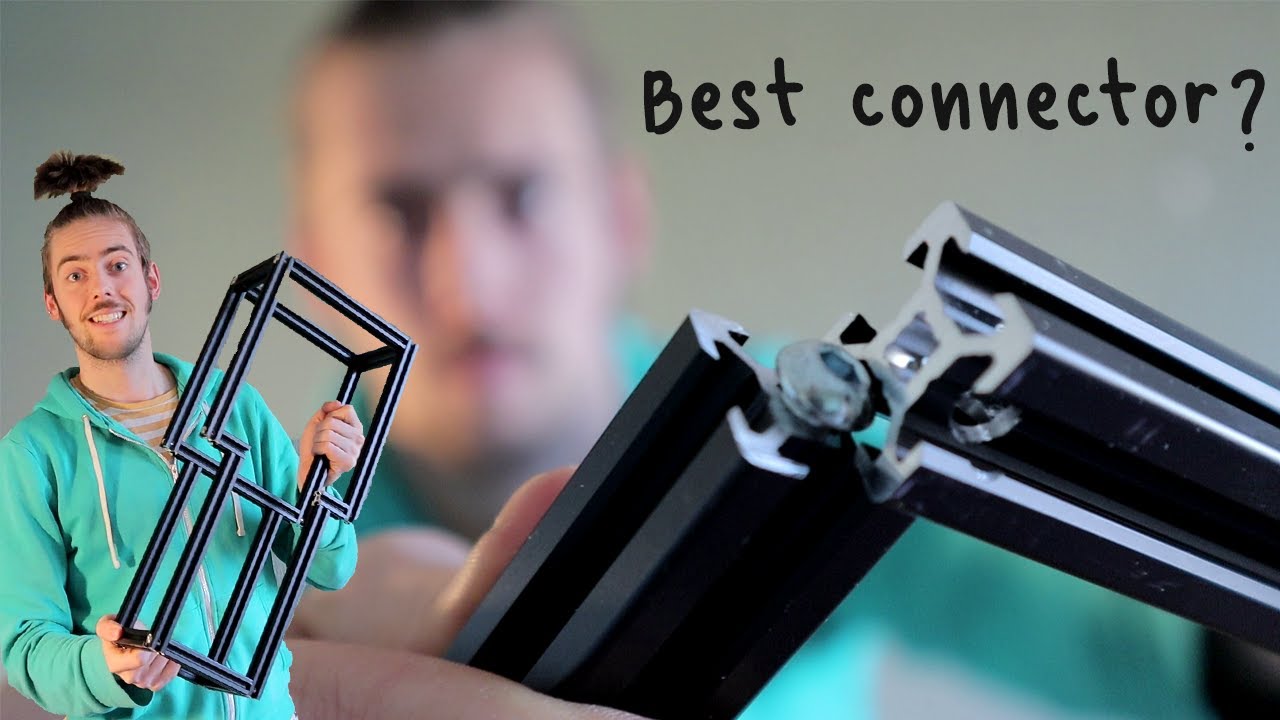
Показать описание
I used aluminium extrusion 2020 for the robot frame that I designed together with Basti Kuhz.
Picking the right connector is difficult, and you only realise the best choice after you've already made yours! Hopefully this video can help others make better decisions.
This is part of my Acrobot project, find more info about it here:
And subscribe for future updates!
Picking the right connector is difficult, and you only realise the best choice after you've already made yours! Hopefully this video can help others make better decisions.
This is part of my Acrobot project, find more info about it here:
And subscribe for future updates!
HOW TO: THE EASIEST AND SIMPLEST WAY TO CREATE A MONTHLY BUDGET! 6-MINUTES PROCESS
THE EASIEST AND CHEAPEST WAY TO PREVENT WATER SPOTS WHILE WASHING YOUR CAR.
How to Make a Gravel Path / The Easiest and Cheapest Way
The Easiest Ways to Add HP to YOUR Car
CHEAPEST And FASTEST Way To Get Your Private Pilot License | Less Than 5K?
“This Will Be The Fastest Way To Get Rich In Human History” | Raoul Pal
Easiest Way To Make Money Online With Your Phone (No Skills Required)
Simple ways to budget and save money | ABC News
500 SERIES EXPLAINED: Easiest and Cheapest Way to Add Analog Sound
THE CHEAPEST and EASIEST WAY TO TRY radio controlled (RC) FLYING ! (EASY TO FLY Volantex Trainstar)
Got 5 Minutes? EASIEST Way To Make Money Online NOW ($300/Day) For Beginners
Is This the Easiest Way to Elevate Your Style?!
I Bought The Fastest Police Car Ever Made & The Cheapest Way To Buy A Modern LS CAR! 4-Door Cama...
The Fastest Way You Can Live Off Dividends! ($2900 / month)
How To: Easiest and Cheapest Way to Metal Glitter Flake a Guitar or Anything Step by Step
Fastest Way to ● Chill A Beverage ( this actually works ! )
6 Easiest & Fastest Ways To Move To Canada 😲
How to Clean a Glass Pipe the CHEAP and EASY Way
How to Polish a Car Polish THE EASY WAY without a Machine Polisher?
easiest way to curl hair!!
EASIEST & CHEAPEST way to Highlight/ Lowlight Hair AT HOME using Loreal Bleach/Permanent Hair Co...
How To: Clean Makeup Brushes | Easiest & Cheapest Way!
The easiest way to get $115 💸🤩😂
STOP WEEDS INSTANTLY the EASY WAY - Grampa's Weed Puller Review
Комментарии