filmov
tv
Is Voron TAP Really 'ALL THAT' ? A Semi-Scientific Analysis
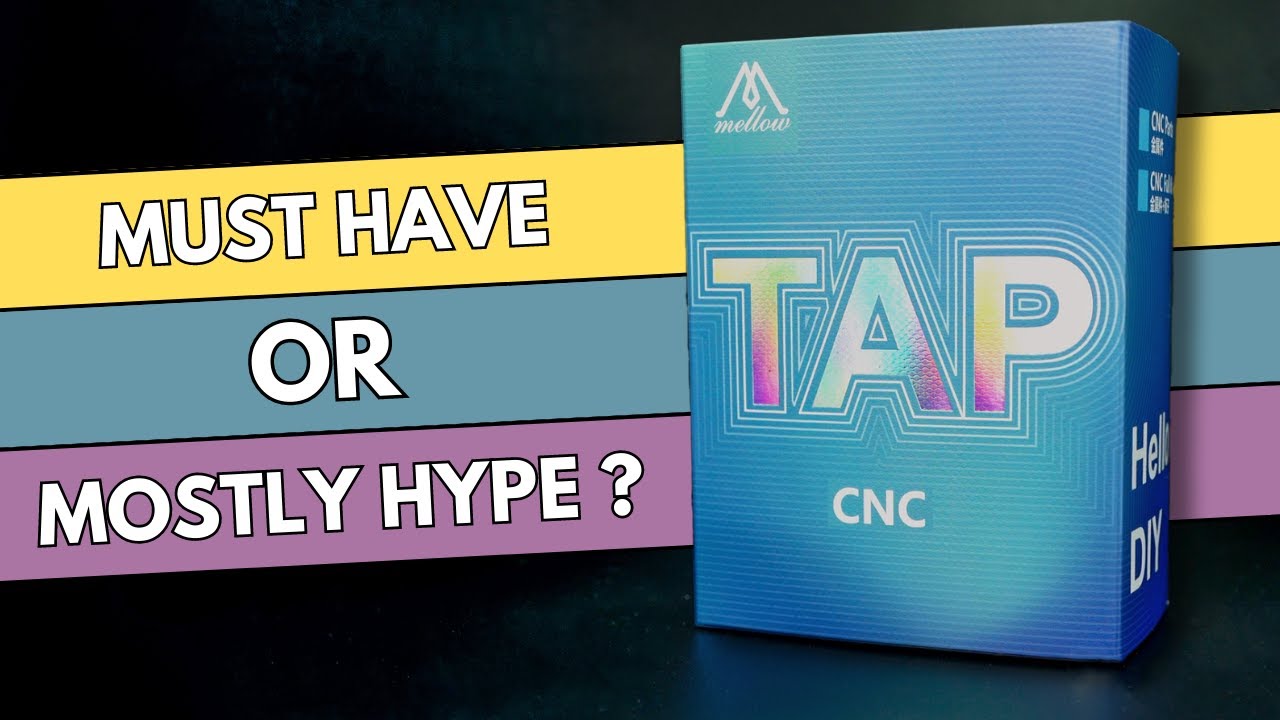
Показать описание
Voron Tap is the 3D printer bed probing solution everyone is talking about, and for good reason. It eliminates the need to recalculate the z offset when changing nozzles or build surfaces. In this video I compare and contrast some of the most popular Tap variants, including both plastic (DIY and pre-assembled) and CNC options (Mellow and Chaotic Labs).
Is Voron TAP Really 'ALL THAT' ? A Semi-Scientific Analysis
Is VORON 2.4 as GOOD as people make you believe? (vs Bambu X1C)
Voron TAP Install and Setup - #3dprinting
Voron VT, sensorless homing and TAP on RFF!
Voron TAP - tap as much as you like
Voron TAP Homing Procedure
Tapchanger vs Voron Tap
Trying Chaoticlab CNC Voron Tap v2.0
Is Your Tap Too Cool to Extrude?
🧪New Channel : CNC VORON TAP V2
Voron TAP build, install, configuration, tips & tricks, final thoughts.
INSANE PRINT of a COMPLEX PART on a tuned Voron - 247zeroB2
Updated! Voron TAP R8
Voron TAP!
Voron TAP
Voron TAP Unklicky with Orbiter
Voron-Tap ist offiziell! https://github.com/VoronDesign/Voron-Tap
Voron TAP with microswitch
BIGTREETECH Eddy V1.0 vs Voron Tap! Speed Battle of the Levelers! #bigtreetech #3d #Eddy #voron #diy
Level The Voron 2.4R2 in 5 seconds, using TAP!
Tap, tap, tap with Voron TAP.
The BEST Voron Mods I've Done! (so far)
Printing a Voron is MUCH easier on a Voron
Voron Tap installed!
Комментарии