filmov
tv
Animation of 2018 Ethylene Release and Fire at Kuraray America in Pasadena, Texas
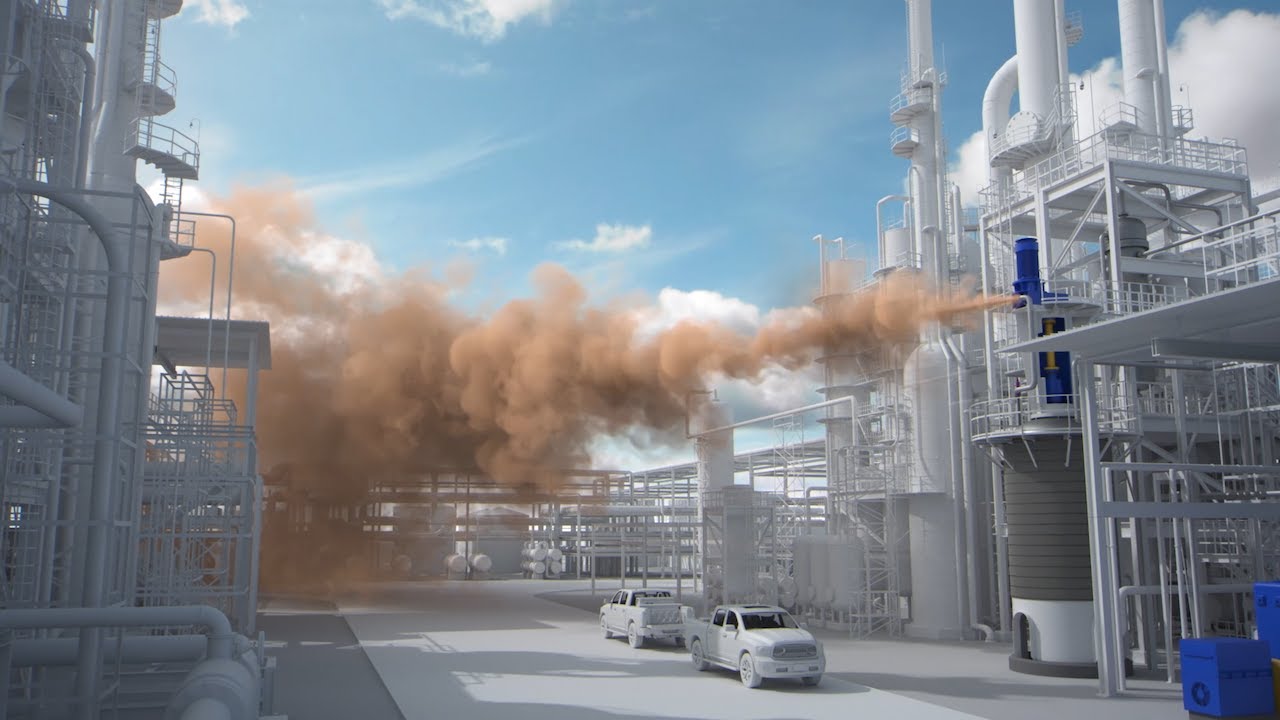
Показать описание
A CSB animation about the 2018 ethylene release and fire that injured 23 workers at the Kuraray America, Inc. EVAL plant in Pasadena, Texas.
Animation of 2018 Ethylene Release and Fire at Kuraray America in Pasadena, Texas
Animation of April 26, 2018, Explosion and Fire at the Husky Energy Refinery in Superior, Wisconsin
Animation of 2015 Explosion at ExxonMobil Refinery in Torrance, CA
HDPE Plant Explosion and Fire
What is Cracking Dow Chemical Builds New Ethylene Production Plant at Dow Texas Operations
Animation of Chemical Release at DuPont's La Porte Facility
Animation of Fire at ExxonMobil's Baton Rouge Refinery
[3D Animation] Ethylene BOG system (Process) Eng.Ver
Interim Animation of Pryor Trust Gas Well Blowout and Fire
ISEC Safety Video & Animation of Ammonia Plant Explosion and Fire Accident at Petrochemical Comp...
EO Sterilization Process
pi to pi star transition
Fire & Explosion due to Ethylene Vapor | Accident Investigation
Technip Energies - Ethylene Decarbonization
Production of Ethylene Dichloride
Ethylene Plant Fire
The Danger of Popcorn Polymer: Incident at the TPC Group Chemical Plant
ISEC Safety Video & Animation of Propane Storage Tank Fire Accident
Animation of Explosion at PCA's DeRidder, Louisiana, Pulp and Paper Mill
Refinery Gas Flare Releasing Huge Fire Mushroom Cloud
Ethylene glycol or antifreeze CHINA MANUFACTURES FACTORY DIRECT
Trying to Cleaning the car radiator with a bottle of water #yearofyou
Ethylene Plant Fire
Ktm duke 200 new model 2023 || New color🎨 duke 200 bs6 2023 || #ktm #duke #duke200 #shorts #ktmduke...
Комментарии