filmov
tv
Exploring the Design Changes of my PrintNC CNC Machine
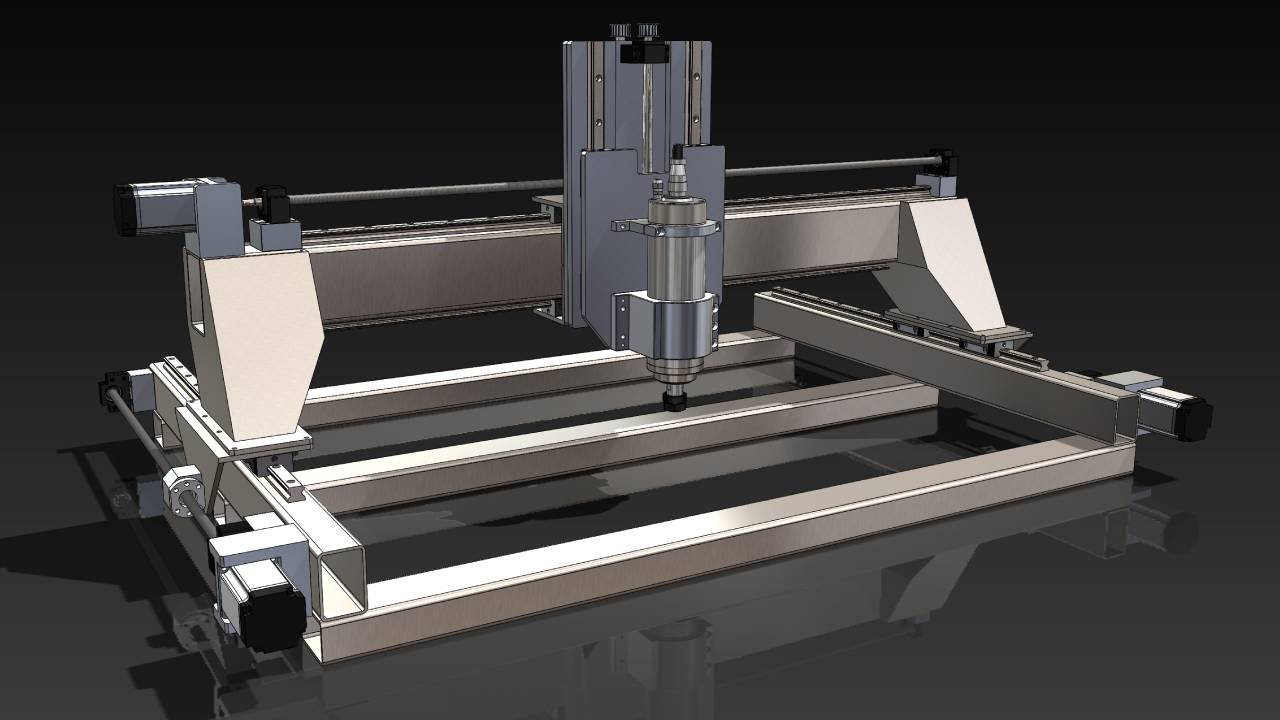
Показать описание
#CNCMachine #PrintNC #design #CAD #Zassembly #gantryrisers #weldedgantry #steelwelding #updates #iteration #inaction
If you enjoy my DIY CNC projects, consider supporting the channel on Patreon. Your support helps me create more content and improve the channel. Thank you!
Exploring the Design Changes of my PrintNC CNC Machine
Explore the Future of Retail Design with Steve Barnes
NEOM City: Saudi Arabia's $500 Billion Futuristic Mega Project #NEOMCity #TheLine #SaudiArabia
THE BETA VERSION OF GTA SAN ANDREAS | WHAT COULD'VE BEEN! 🔍 #gta #gtasanandeas
Explore the Classic Elegance of This 60-Year-Old House in Baguio City | Unique Homes | OG
UDL Talk: Exploring Design and Systematic Change
Engineering Excellence: Exploring Lucid Air's Incredible Efficiency
Discover Architectural Marvels | 🔥 Explore the Essence of Design and Innovation!
Nail Art Inspiration That Will CHANGE Your Style!
WWDC24: A Swift Tour: Explore Swift’s features and design | Apple
Exploring the Intersection of Technology and Design in Luxury Living, Episode 5
Evolution of Style | Exploring the Design Changes in Each Generation of Hyundai Creta
EXPLORE the New Anime Clothing Collection That's About to Change Everything!
2H Webinar | Exploring Efficient Design for Jacket Platform Conductors
Evolution of Tanks in GTA games #shorts #gtaonline
Design for change: Exploring the future of work
The Soul of Design: Exploring the Neuroscience of Beauty
Exploring the design details of the nike air max 1
Design changes #graphicdesigner #graphicdesign #creative #trending #comedy #explore
Exploring the Tech and Design of Noita
Beyond Design: Exploring the Frontiers of Design Technology (GDSC Unilorin)
Sagwaan Mandir Design #woodentemple #poojamandir #explore #goviral #ytshort #reels #aarsun
An old party trick and a wonderful new technique #shorts
Future By Design: exploring the Architecture of climate crisis
Комментарии