filmov
tv
Overrunning Alternator Pulley simulation using RecurDyn - a multibody dynamics software
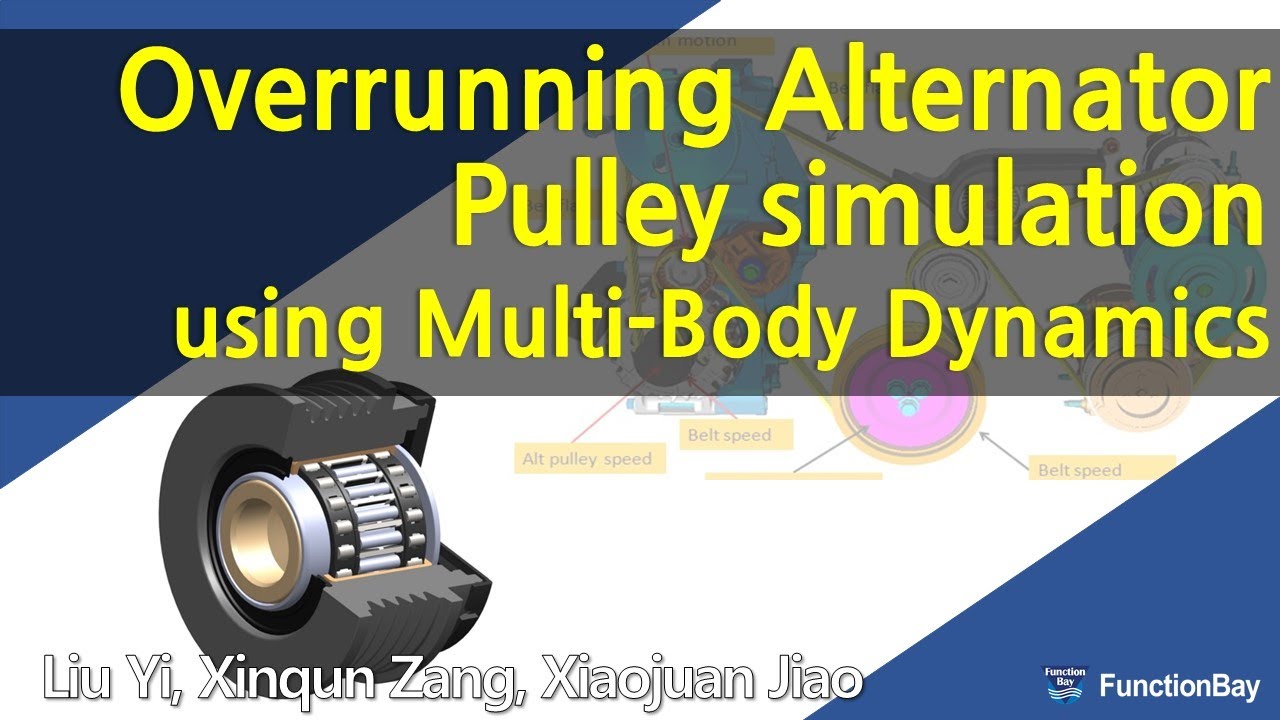
Показать описание
This is a webinar on the multibody dynamics simulation of Overrunning Alternator Pulley using RecurDyn
In order to solve the front-end accessory drive system (FEAD) problem caused by engine speed fluctuations, an Overrunning Alternator Pulley (OAP) was developed and a comparative study of CAE analysis and tests was conducted. Based on the multi-body dynamics theory, a virtual prototype model of the one-way pulley block was established. The model can accurately reflect its operating characteristics. On this basis, the factors affecting the operating characteristics of the OAP were studied, and some useful guiding conclusions were drawn:
(1) When the friction coefficient μ = 0.10-0.15, the wedge time of the needle roller, mandrel and outer ring will change significantly. As the friction coefficient increases, the wedge time is substantially reduced;
(2) The maximum contact impact force occurs at the contact point between the needle roller and the mandrel. The maximum contact force is generally about 4 times the stable contact force at 6000rpm (equivalent to the stable speed of the engine);
(3) Under different friction coefficients, the average contact force between the needle roller and the mandrel and outer ring after OAP wedging does not differ much, but the impact force can be reduced by reducing the friction coefficient;
(4) Selecting the appropriate spring stiffness and spring preload directly affects the wedging characteristics of the OAP during operation.
This presentation was presented at International CAE Conference 2020.
Additional Resources:
#RecurDyn #Particleworks #FSI #MultibodyDynamics #CFD #MBD #MBS #RigidBodyDynamics #MFBD #FMBD #motion #mbd #mbs #simulation #cae #CFDsoftware #DigitalTwin #FluidDynamics #리커다인 #펑션베이 #FunctionBay #ICC2020
In order to solve the front-end accessory drive system (FEAD) problem caused by engine speed fluctuations, an Overrunning Alternator Pulley (OAP) was developed and a comparative study of CAE analysis and tests was conducted. Based on the multi-body dynamics theory, a virtual prototype model of the one-way pulley block was established. The model can accurately reflect its operating characteristics. On this basis, the factors affecting the operating characteristics of the OAP were studied, and some useful guiding conclusions were drawn:
(1) When the friction coefficient μ = 0.10-0.15, the wedge time of the needle roller, mandrel and outer ring will change significantly. As the friction coefficient increases, the wedge time is substantially reduced;
(2) The maximum contact impact force occurs at the contact point between the needle roller and the mandrel. The maximum contact force is generally about 4 times the stable contact force at 6000rpm (equivalent to the stable speed of the engine);
(3) Under different friction coefficients, the average contact force between the needle roller and the mandrel and outer ring after OAP wedging does not differ much, but the impact force can be reduced by reducing the friction coefficient;
(4) Selecting the appropriate spring stiffness and spring preload directly affects the wedging characteristics of the OAP during operation.
This presentation was presented at International CAE Conference 2020.
Additional Resources:
#RecurDyn #Particleworks #FSI #MultibodyDynamics #CFD #MBD #MBS #RigidBodyDynamics #MFBD #FMBD #motion #mbd #mbs #simulation #cae #CFDsoftware #DigitalTwin #FluidDynamics #리커다인 #펑션베이 #FunctionBay #ICC2020
Комментарии