filmov
tv
Fiber-reinforced resin prints - how much STRONGER are they?
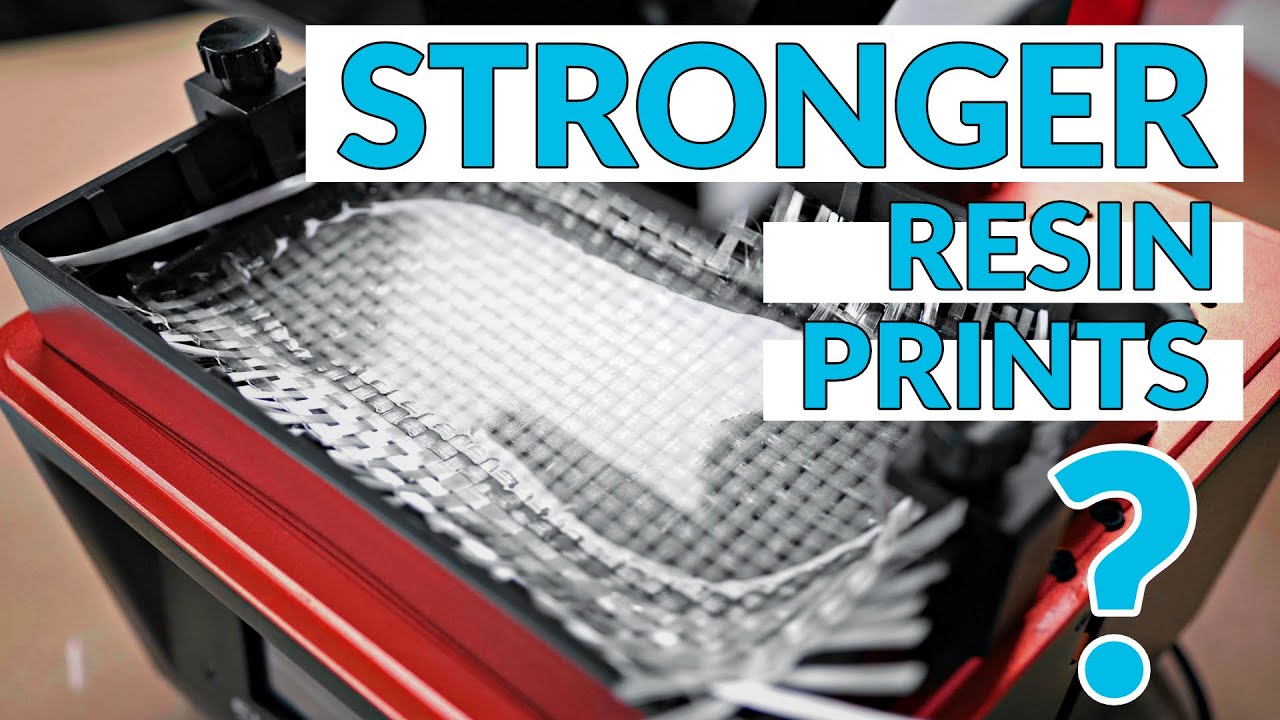
Показать описание
Can we create DIY fiber-reinforced parts on a normal resin printer? What materials other than carbon fiber cloth and glass fibers can we use? Does it make the parts we produce actually stronger? Let's find out!
Products used
Buy Siraya Tech Resins on Amazon
Product links are affiliate links - I may earn a commission on qualifying purchases (at no extra cost to you)
Products used
Buy Siraya Tech Resins on Amazon
Product links are affiliate links - I may earn a commission on qualifying purchases (at no extra cost to you)
Easier Fiber-Reinforced Resin Printing! Stronger and Conductive Resin Prints?
Fiber-reinforced resin prints - how much STRONGER are they?
strengthening prints! #3Dprinting #fiberglass #LearnOnTikTok #TikTokPartner
#10 How to reinforce your 3D prints with carbon fiber. Basics of composites.
How to Fiberglass Your 3D Printed Suit!
Carbon Fiber Parts from 3D Printed Mold Patterns. RC Airplane Rudder. #carbonfiber #aviation
Using Fiberglass Resin with 3D Prints | Boba Fett Part 6
3D Printed Moulds To Make Carbon Fiber Epoxy Resin Tubes – How to Tutorial
Reinforce Your 3D Prints with Carbon Fibers and Epoxy
A few ways to reinforce 3d printed parts.
STRONGER 3D Prints with GLUE? (and CARBON FIBERS)
Carbon Fiber #3dprinting Filaments (& More!)
3D Printed Planetary Gearbox! Resin vs FDM Printing?
Reinforcing 3D Printed Parts with Continuous Fiber Injection Process | Formnext 2023
Hand Laminating a Carbon Fibre Part Directly into a 3D Printed Mould
💰🤨Low-Cost Fiberglass Reinforcement for 3D Printed Parts 🧵 🪡
Electroplating 3D Prints | New Graphite Tutorial
Carbon Fiber 3D Printer Filaments: What Are They Good For?
Carbon Fiber 3D Printing 101 | Why All Carbon Filled Filaments Aren't Equal
3D printed objects coated with epoxy resin - but why?
Does resin strenghten your 3D prints? 🤔
all product fiberglass FRP Fiber Reinforced Plastic all fiberglas resin product
How STRONG is 3d printed CARBON FIBER?
Making Forged Carbon Fiber Parts
Комментарии