filmov
tv
SHOULD CWI’s HAVE WELD EXPERIENCE?
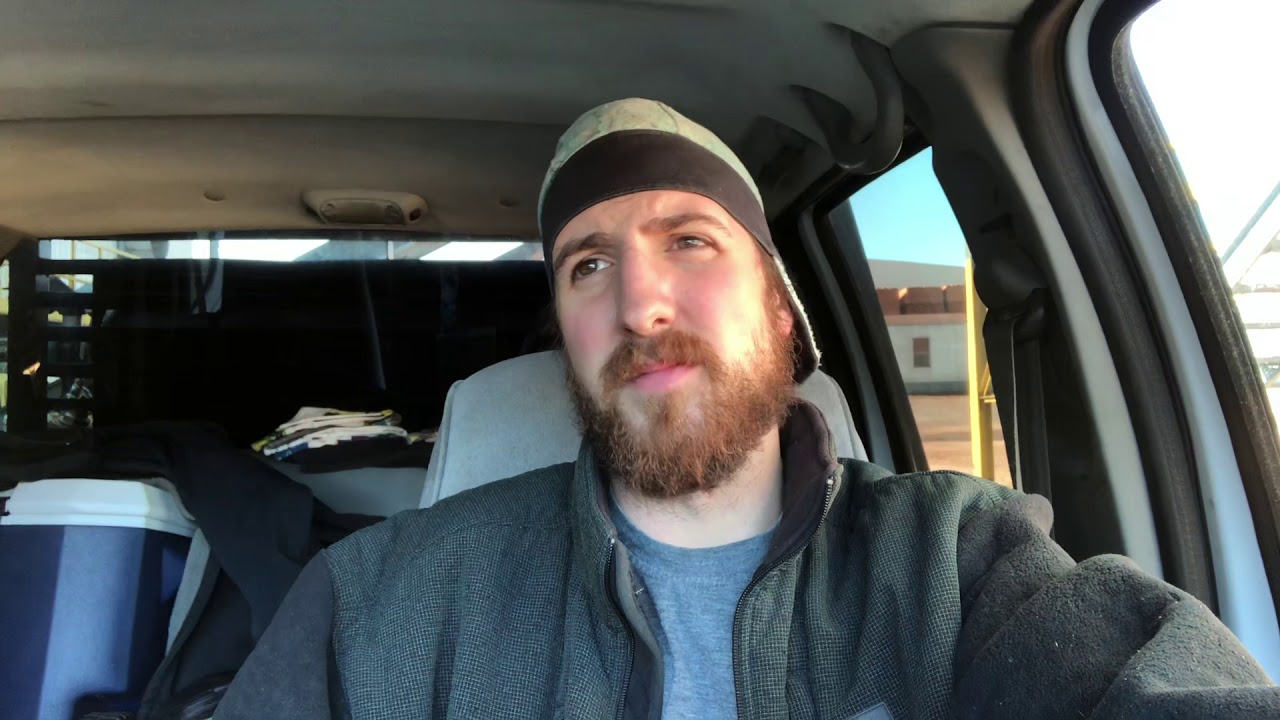
Показать описание
I once believed they should but now I more believe the only thing required of them is to be exceptional in their trade as we should be in ours
So you want to be a Certified Welding Inspector??? Tips and Tricks to Prepare for the CWI Test
AWS Certified: CWI
Prep before the prep ... CWI Exam
CWI 37 - AWS CWI's Automactically Qualify For ASNT Level II VT 2019
CWI 30 - Part A Welding Processes Quick View SMAW GMAW FCAW GTAW B U4a
How to Become a CWI (SI Certs Roadmap)
AWS Certified Welding Inspector (CWI) Certification
Welding And CWI Inspection On Udemy Online Courses
CWI Course - Module 1: Welding Inspection and Certification.
Option 1- Road to CWI Certification - 2 Weeks in Classroom
The Ultimate Guide to Developing Your CWI Career Path
CWI 41 - WIT CHAPTER 1 CWI WELDING INSPECTION AND CERTIFICATIONS
Fundamentals for Certified Welding Inspector - CWI/CWB exam Part A Sample Questions #viralvideo
CWI Exam II
Full Compilation of 100 CWI Part A Questions - Answers and Detailed Explanation!
Houston Welding Inspection Service - AWSCWI COM AWS CWI
International welding engineer exam questions: Material and their behavior for CWI and CSWIP
Pass CWI Part A EASILY with These Questions and Explanations! - Set 1
Professional AWSCWI.COM Guam Welding Inspection Services
Can you really make 100k as a welder?
(HIGHLY REQUESTED) LAND 1ST WELDING JOB| No Experience? Job Search Tips, Networking, Resume
Nondestructive Testing is part of the AWS Careers in Welding mobile experience!
100 CWI Part A Questions Full Compilation with Detailed Explanation
CSWIP CERTIFICATION PROGRAM #qualitycontrol #cswip
Комментарии