filmov
tv
The BEST 3D printing material? Comparing PLA, PETG & ASA (ABS) - feat. PRUSAMENT by Josef Prusa
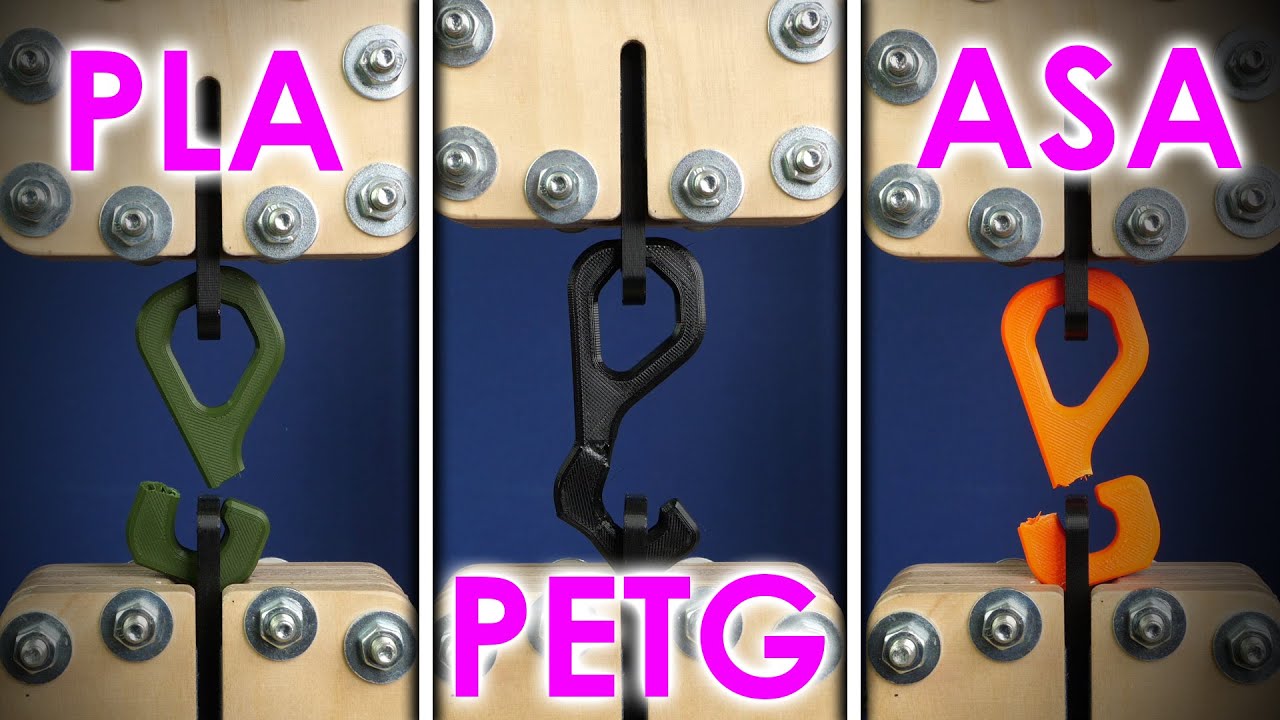
Показать описание
Which 3D printing material is best for your application? I tested PRUSAMENT PLA, PETG and ASA to see how the perform in the categories: Price, Printability, Printing Quality, Static Strength and Layer Adhesion, Ductility, Stiffness, Impact Resistance and Thermal Resistance.
Let's find out how the materials perform and when you should use which!
Print settings of the hooks:
3 perimeters, 20% infill, 0.165mm layer height, 8 top & bottom layers
💚 Support me 💚
Join as a YouTube member!
🤑 Get the materials:
🎙Check out my PODCAST with Tom Sanladerer
🎥 Related videos:
⚙ My gear (Affiliate Links):
🎥 CAMERAS & LENSES
🎙AUDIO
🔴 LIVE STREAMING
Let's find out how the materials perform and when you should use which!
Print settings of the hooks:
3 perimeters, 20% infill, 0.165mm layer height, 8 top & bottom layers
💚 Support me 💚
Join as a YouTube member!
🤑 Get the materials:
🎙Check out my PODCAST with Tom Sanladerer
🎥 Related videos:
⚙ My gear (Affiliate Links):
🎥 CAMERAS & LENSES
🎙AUDIO
🔴 LIVE STREAMING
The BEST 3D printing material? Comparing PLA, PETG & ASA (ABS) - feat. PRUSAMENT by Josef Prusa
What is the strongest 3D printing material
All the Different 3d printing Filaments Explained!
3D Printing Materials Explained: Compare FDM, SLA, and SLS
The 3D Printer I'd buy if I started over
Which is the MOST RIGID 3D printing material?
Which 3D Printed Gear is Best?
The ULTIMATE Guide to 3D Printing Materials - Usability and Demand for High-End Filaments
Best 3D Printer in 2024 | Top 6 Best 3D Printer in 2024
TOP 10 BEST 3D PRINTERS 2023
3D Printing For Outdoor Use: Materials Comparison - PLA, ABS, Nylon, PETG, TPU, ASA
Resin vs. PLA 3D Printing: Which Is Best??
Top 20 BEST 3D printed products to SELL! 🤑💰💵
The King of 3D printing materials? Polymaker PolyMax PC REVIEW
Flexible 3D Printing Filaments Tested - Which Flex is Best?
Plastic (FDM) or Resin (LCD) 3D Printing?! Which is BEST for Cosplay & Props?!
Which 3D Printer Should You Get? A COMPLETE Beginner's Guide
3D printing from flexible/soft plastic materials (filaments TPU, TPE, )
PLA vs ABS | What's the Difference for 3D Printing?
Resin VS FDM 3D printers: Which one is the best for miniatures?
What are The BEST 3D Printers? | After 3 Years of Testing Here’s My FAVORITES!
How much STRONGER is PLA+ really?
5 must-know 3D printing tips & tricks. (stronger and better looking prints)
Best Industrial 3D Printers and Their Benefits
Комментарии