filmov
tv
Why Spray Foam Under Asphalt Shingles is a Bad Idea
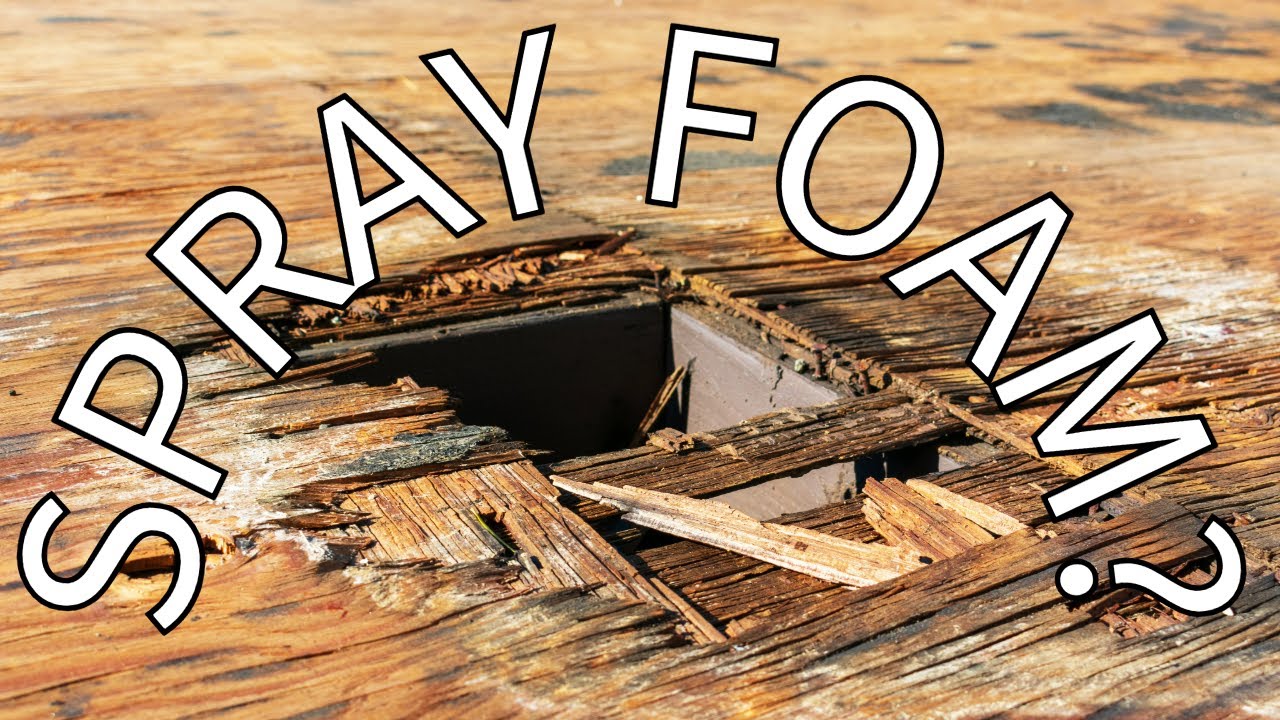
Показать описание
In this episode of Smith House, Jordan Smith, a design builder with Smith House Company, dives deep into the controversial topic of using spray foam on the backside of asphalt shingle roofs. With a focus on building houses that are beautiful, functional, resilient, and healthy, Jordan explains why he believes this common practice may not be the best approach.
⚠️ Key Points Covered:
Warranty Concerns: Some shingle manufacturers don't allow spray foam directly against the decking, potentially voiding warranties.
Replacement Challenges: If decking needs replacement, the spray foam must also be replaced, leading to added costs and complexity.
Exploring Alternatives: Jordan explores the drawbacks of traditional ventilated attics, the benefits and limitations of spray foam, and proposes a third approach for optimal performance and longevity.
🔍 Video Breakdown:
Introduction: Jordan introduces the topic and outlines his concerns.
Ventilated Attic: Discusses the benefits and challenges of traditional ventilated attic systems.
Spray Foam Solution: Explores how spray foam addresses some attic ventilation issues but introduces new challenges.
Optimal Roof Assembly: Introduces a continuous insulation house as a potential solution, highlighting its benefits over traditional methods.
🔧 Building for the Future: Jordan emphasizes the importance of thoughtful building practices that prioritize durability, energy efficiency, and ease of maintenance.
💬 Engage with Us: Share your thoughts in the comments below. Agree or disagree? Let us know! Have suggestions for future topics? We're all ears!
👍 Don't Forget to Like, Subscribe, and Follow! Stay updated with our latest content on Instagram and TikTok.
🔗 Connect with Us:
Thanks for watching, and see you in the next episode of Smith House!
⚠️ Key Points Covered:
Warranty Concerns: Some shingle manufacturers don't allow spray foam directly against the decking, potentially voiding warranties.
Replacement Challenges: If decking needs replacement, the spray foam must also be replaced, leading to added costs and complexity.
Exploring Alternatives: Jordan explores the drawbacks of traditional ventilated attics, the benefits and limitations of spray foam, and proposes a third approach for optimal performance and longevity.
🔍 Video Breakdown:
Introduction: Jordan introduces the topic and outlines his concerns.
Ventilated Attic: Discusses the benefits and challenges of traditional ventilated attic systems.
Spray Foam Solution: Explores how spray foam addresses some attic ventilation issues but introduces new challenges.
Optimal Roof Assembly: Introduces a continuous insulation house as a potential solution, highlighting its benefits over traditional methods.
🔧 Building for the Future: Jordan emphasizes the importance of thoughtful building practices that prioritize durability, energy efficiency, and ease of maintenance.
💬 Engage with Us: Share your thoughts in the comments below. Agree or disagree? Let us know! Have suggestions for future topics? We're all ears!
👍 Don't Forget to Like, Subscribe, and Follow! Stay updated with our latest content on Instagram and TikTok.
🔗 Connect with Us:
Thanks for watching, and see you in the next episode of Smith House!
Комментарии