filmov
tv
Woodturning a Platter with Thick Inlays
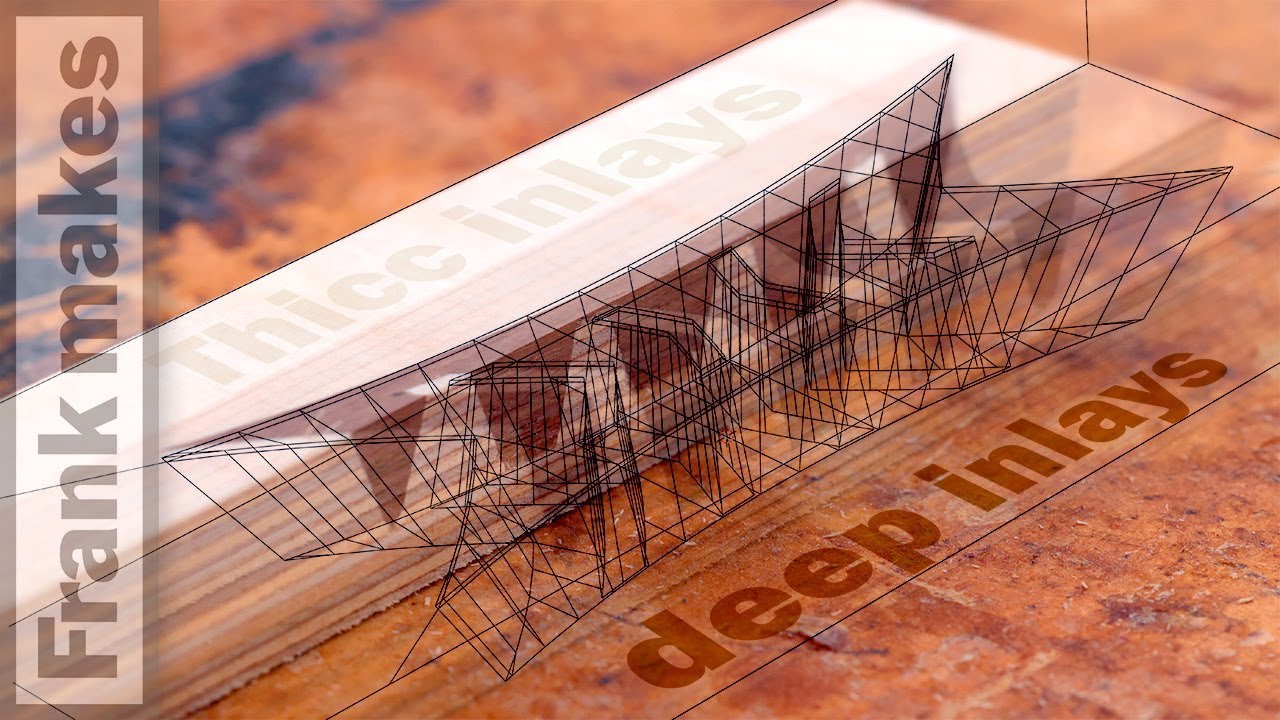
Показать описание
What really intrigued me about building and using a CNC machine was the idea of being able to cut complex inlays that I could then wood turn. I've done several projects with this in mind, but in these projects I've always used a straight router bit to get a deep inlay. In woodturning, the inlay needs some thickness to be able to have a curved surface. What I've been trying to do over the last few months is to do v-carved inlays where you use a bit that has a point on it to carve the positive and negative of the inlay. What this allows is more pointy inside corners. You can use the tip of the tool to carve that corner. But I have found this becomes much more complicated as the inlay is now a three-dimensional object and not just a straight extrusion. There are many videos online about doing the carve inlays but none of them really talk about doing deep or thick inlays as most people are doing inlays for cutting boards or surface work. The first mistake I made early on is that I need to define the bit that I'm using very precisely in the program. The bit I was using had a 30 second of an inch diameter bullnose at the tip and I had been defining it as just a pointed bit with an infinitely pointy point. This small detail made the inlay not fit correctly. After cutting the piece that I had worked on gluing together, and had done many many tests, I thought everything was working well. However, when I cut the pieces to see how they had fit together, they still did not fit together correctly. I put the project aside for a few weeks and I thought about why I was having a problem. I think what I had done was I had made a design that looks symmetrical but I hadn't quite drawn it symmetrical. When I put the pieces together I just didn't have them oriented correctly and they didn't quite fit perfectly. So in my final iteration, I redrew my shapes to be perfectly symmetrical and thus it wouldn't matter which way they went in. And in this final piece it seems to be working fairly well. I think the other issue that I need to work through is that it takes a lot of force to glue the two angled inlays together. So I need to make some kind of press for gluing up the pieces.
After all of my experiments with inlays, I finally woodturned a simple platter on the lathe. The form was a small bowl in the center with a very wide rim. I could put the thick inlays in this wide rim. This was a first step in trying to make a not very complicated woodturning project to practice woodturning with inlays.
Tools used in this project can be found at
To see upcoming projects follow me on social media
0:00 (introduction)
1:13 (glue up)
3:33 (testing inlays)
6:19 (glue up)
8:08 (CNC)
15:00 (second attempt)
21:33 (woodturning)
24:36 (conclusion)
After all of my experiments with inlays, I finally woodturned a simple platter on the lathe. The form was a small bowl in the center with a very wide rim. I could put the thick inlays in this wide rim. This was a first step in trying to make a not very complicated woodturning project to practice woodturning with inlays.
Tools used in this project can be found at
To see upcoming projects follow me on social media
0:00 (introduction)
1:13 (glue up)
3:33 (testing inlays)
6:19 (glue up)
8:08 (CNC)
15:00 (second attempt)
21:33 (woodturning)
24:36 (conclusion)
Комментарии