filmov
tv
Low Cost Hydroforming
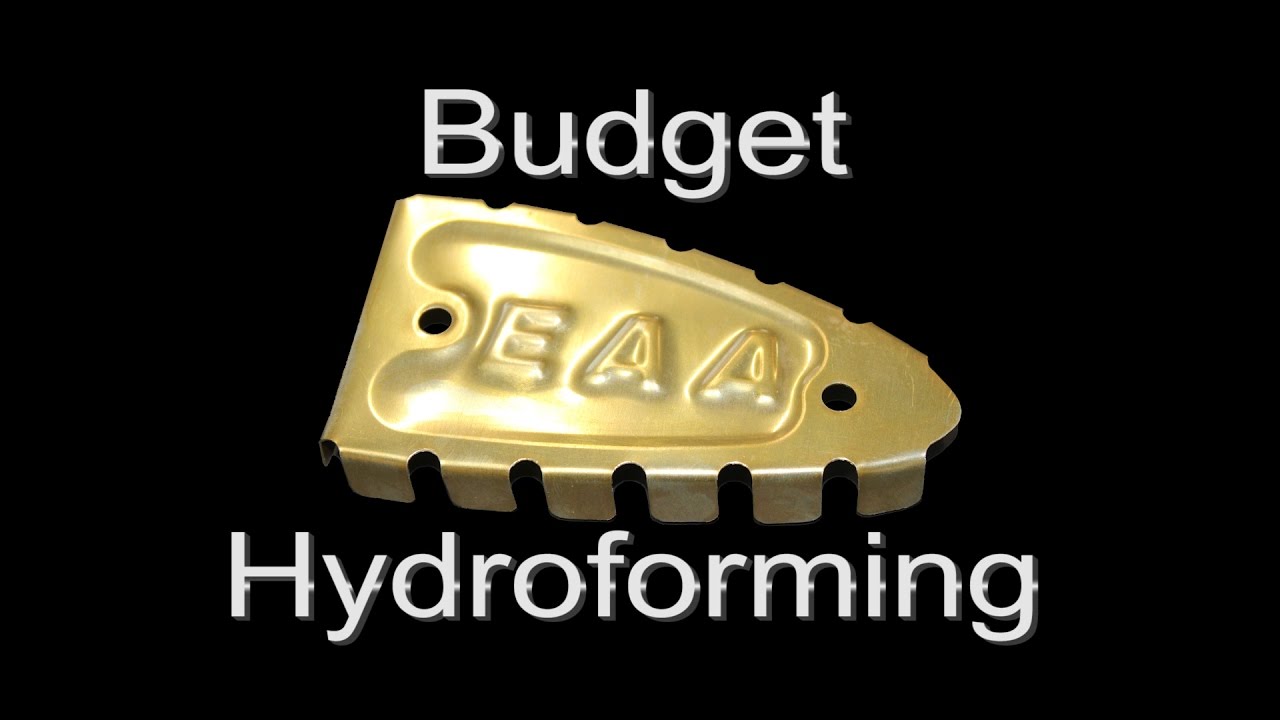
Показать описание
Low cost hydroforming on the Rainbow Aviation Video channel with your host Brian Carpenter. In this episode were going to be taking a look at a low cost way to manufacture your own aluminum hydro-formed parts.
This is a companion video for technically speaking article published in the May 2016 sport aviation magazine
Link to free plans
This is a companion video for technically speaking article published in the May 2016 sport aviation magazine
Link to free plans
Low Cost Hydroforming
This is Quintus Hydroforming -- Low Tool Costs, Short Lead Times, and High Quality
Hydroforming Process
Hydroforming
Hydroforming - How it works
Hydroforming at home
Hydroforming for the Automotive Industry- Low Tool Costs, Short Lead Times, and High Quality
Quintus Technologies Flexform™ Hydroforming QFC 0.7x1.8 - 800 Press
DIY Hydroforming Tutorial
Quintus Hydroforming Principle Animation (Chinese Subtitle)
Hydroforming Sheet Metal Process - Sheet Metal Forming - Hydroforming Video - F&BMFG
hydroforming aluminum bike frame China customize,sheet hydroforming technology Manufacturer in china
Metal Hydroforming
Hydroforming Process - Facts About Hydroforming at JMP
Hydroforming | Kubes Steel
||Metal Sheet Hydroforming|| Hydroforming || Metal Sheet|| Tube Hydroforming|| #shorts #ytshorts
Hydroforming
My hydroforming machine
Top 6 Hydroforming Advantages | Jones Metal
Trial setup for Hydroponic Lovers😊😊; Contact @9300756573; #JS_Hydroponics
hydroforming exhaust pipes machine china manufacturers.
Quintus Technologies Flexform (Hydroforming) Principle Animation
sheet metal forming hydroforming process Manufacturer in china,tube end forming machine China compan
Quintus Hydroform -- Low Tool Costs, Short Lead Times, and High Quality
Комментарии