filmov
tv
Building a Solar Plane - Part 2
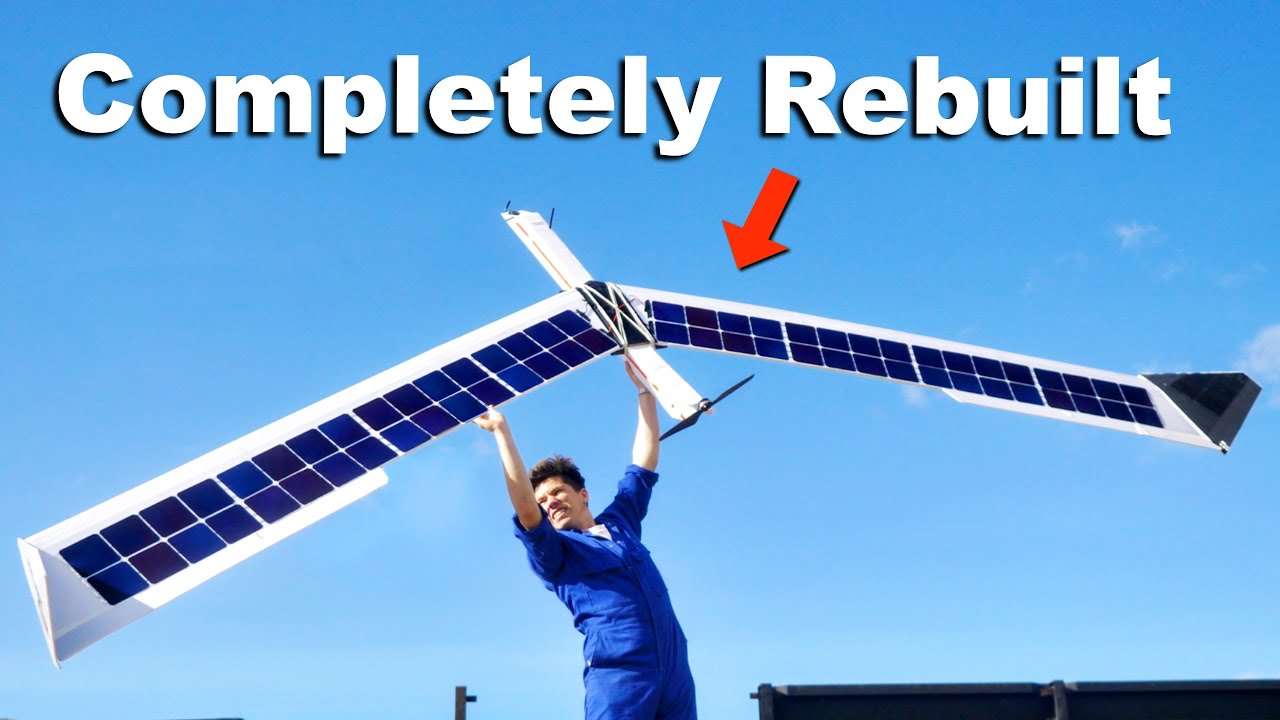
Показать описание
Thanks to @DIYPerks for his help with this build!
Recently, I talked about this project with the BBC when they visited the Project Air workshop to check out the Guinness World Record for the Worlds Largest RC Aircraft Carrier.
DISCLAIMER: This video is purely for entertainment value. Personal use of video content is at your own risk. Recreations of experiments, activities and projects are the sole legal responsibility of the person(s) involved in replicating them. I can not be liable for any information or misinformation, wrongful use, damage to personal property, death or any circumstances that result from replication of any projects seen. Be safe!
Building a Solar Plane
Building a Solar Plane - Part 2
RC Solar Plane Flight Duration Test
R/C Flying Solar Panel???
SOLAR Powered RC FPV Plane Build and Maiden - RCTESTFLIGHT -
Solar Plane V4 Cross-Country Waypoint Mission
Students build solar plane from scratch for record attempt
Solar powered drones: flying wing, multicopter, glider
rc glider powered by solar energy
Solar powered stratospheric plane could save lives
Solar Plane V3 FPV Flight to Mountain Peak - RCTESTFLIGHT
Flying to the edge of space using only solar power
Circling the Globe in a Solar-Powered Plane
SOLAR DRONE with 4GLte SIM CARD MOD 40 Mile Flight - Parrot Disco 4G - Long Range FPV Ukraine RECON?
00-03376 - Solar Plane Mobile
DIY: Make a Solar RC Plane under 60$
How to build an Autonomous UAV for Long Range FPV & Autonomous Missions
2.6M FPV Glider with Solar Cells on Wing
#youtubeshorts RC airplane
Elon Musk on Solar 😱😱😱
The solar-powered aircraft flying high in the atmosphere | BBC News
How to build an Autonomous UAV for Long Range FPV & Waypoint Missions - Lightweight UAV
This Genius Airplane consumes Less Fuel than SUV
DIY Solar RC Plane under 50$ Version 2
Комментарии