filmov
tv
Creating grid electricity cables involves several detailed and precise steps #manufacturing
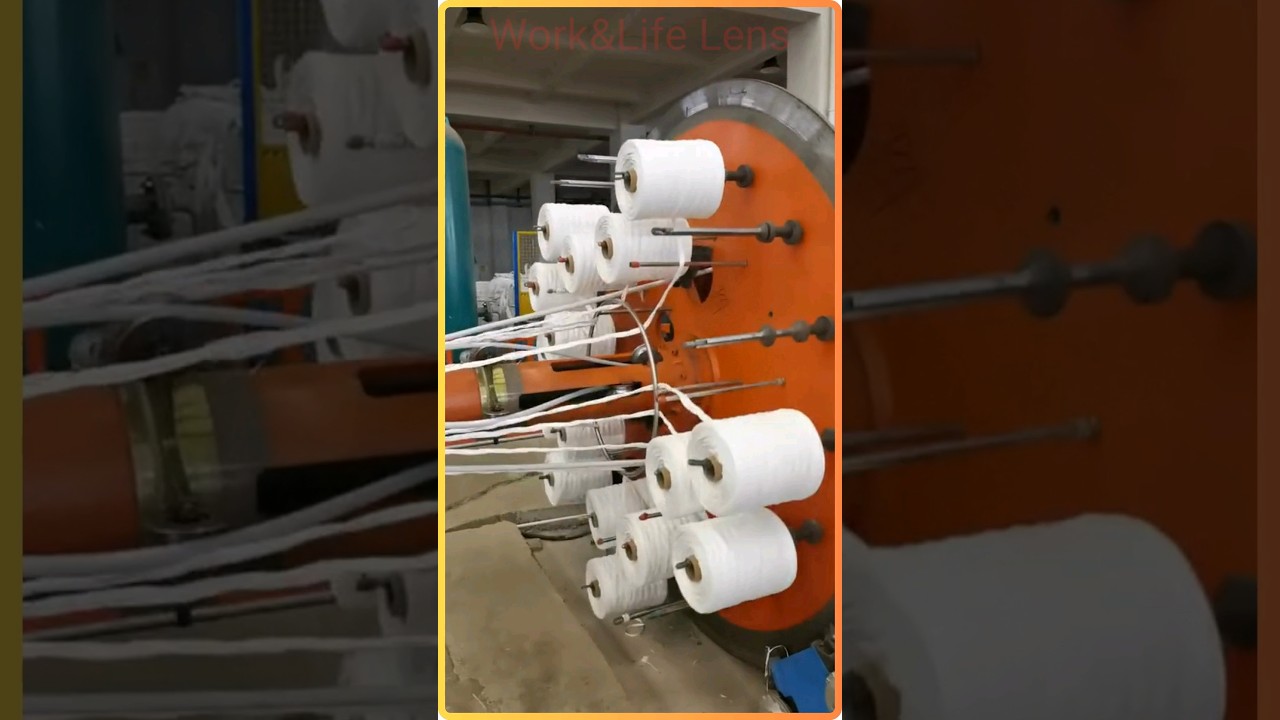
Показать описание
Creating grid electricity cables involves several detailed and precise steps to ensure they are durable, conductive, and safe for use.
1. Stranding
Spindles: Multiple aluminium wires are fed onto spinning spindles.
Stranding: The spindles twist the individual aluminium wires together to form a single, larger conductor. This process may involve several layers of twisting, depending on the desired cable thickness and application. The stranding process increases the flexibility and mechanical strength of the final cable.
2. Annealing (If Required)
Purpose: Annealing involves heating the stranded aluminium conductor to a specific temperature and then cooling it slowly. Although less common for stranded wire than for single-drawn wire, it may still be necessary to improve ductility and conductivity.
Benefit: This process softens the aluminium, making it more malleable and easier to handle during subsequent processes.
3. Insulation Wrapping
Material: The stranded aluminium conductor is then wrapped in an insulating material. This is often a white tape-like substance made from materials such as polyvinyl chloride (PVC), polyethylene (PE), or cross-linked polyethylene (XLPE).
Application: The insulation is applied by passing the stranded conductor through an extruder or wrapping machine. The machine covers the conductor with a consistent and uniform layer of insulating tape.
Purpose: This insulation is crucial for preventing electrical shorts, protecting the wire from environmental factors, and ensuring the safety and reliability of the cable.
4. Additional Layers (If Needed)
Shielding: For cables that require protection against electromagnetic interference, an additional layer of shielding might be applied. This can involve wrapping the insulated wire with metal tapes or braids.
Armouring: For cables intended for underground or underwater use, an extra layer of armouring, such as steel wire or tape, might be applied to protect against physical damage.
5. Winding onto Reels
Wooden Reels: The finished cable is then wound onto large wooden reels for transport and storage. These reels are designed to handle the weight and length of the cable, ensuring it remains intact and untangled.
Process: The winding process is controlled to ensure the cable is wound evenly and tightly, preventing kinks or bends that could damage the insulation or conductor.
6. Quality Control
Inspection: Throughout the manufacturing process, the cable undergoes rigorous testing and inspection. This includes checking the diameter, conductivity, insulation integrity, and overall quality.
Testing: Various electrical tests, such as high-voltage testing, are performed to ensure the cable meets all necessary standards and specifications. Tests also ensure the insulation is applied correctly and that the stranded conductor maintains its integrity.
7. Packaging and Shipping
Final Check: Before shipping, the reels are labelled with important information, including the cable type, length, and any relevant standards or certifications.
Transport: The reels are then securely packaged and transported to their destination, ready to be installed in the grid or other electrical systems.
Summary
Starting from the stranding stage, the process of creating grid electricity cables using aluminium wire involves twisting multiple wires together, possibly annealing, wrapping with an insulating material, applying additional layers if needed, winding onto reels, and thorough quality control checks. Each step ensures that the final product is reliable, safe, and capable of efficiently transmitting electricity.
1. Stranding
Spindles: Multiple aluminium wires are fed onto spinning spindles.
Stranding: The spindles twist the individual aluminium wires together to form a single, larger conductor. This process may involve several layers of twisting, depending on the desired cable thickness and application. The stranding process increases the flexibility and mechanical strength of the final cable.
2. Annealing (If Required)
Purpose: Annealing involves heating the stranded aluminium conductor to a specific temperature and then cooling it slowly. Although less common for stranded wire than for single-drawn wire, it may still be necessary to improve ductility and conductivity.
Benefit: This process softens the aluminium, making it more malleable and easier to handle during subsequent processes.
3. Insulation Wrapping
Material: The stranded aluminium conductor is then wrapped in an insulating material. This is often a white tape-like substance made from materials such as polyvinyl chloride (PVC), polyethylene (PE), or cross-linked polyethylene (XLPE).
Application: The insulation is applied by passing the stranded conductor through an extruder or wrapping machine. The machine covers the conductor with a consistent and uniform layer of insulating tape.
Purpose: This insulation is crucial for preventing electrical shorts, protecting the wire from environmental factors, and ensuring the safety and reliability of the cable.
4. Additional Layers (If Needed)
Shielding: For cables that require protection against electromagnetic interference, an additional layer of shielding might be applied. This can involve wrapping the insulated wire with metal tapes or braids.
Armouring: For cables intended for underground or underwater use, an extra layer of armouring, such as steel wire or tape, might be applied to protect against physical damage.
5. Winding onto Reels
Wooden Reels: The finished cable is then wound onto large wooden reels for transport and storage. These reels are designed to handle the weight and length of the cable, ensuring it remains intact and untangled.
Process: The winding process is controlled to ensure the cable is wound evenly and tightly, preventing kinks or bends that could damage the insulation or conductor.
6. Quality Control
Inspection: Throughout the manufacturing process, the cable undergoes rigorous testing and inspection. This includes checking the diameter, conductivity, insulation integrity, and overall quality.
Testing: Various electrical tests, such as high-voltage testing, are performed to ensure the cable meets all necessary standards and specifications. Tests also ensure the insulation is applied correctly and that the stranded conductor maintains its integrity.
7. Packaging and Shipping
Final Check: Before shipping, the reels are labelled with important information, including the cable type, length, and any relevant standards or certifications.
Transport: The reels are then securely packaged and transported to their destination, ready to be installed in the grid or other electrical systems.
Summary
Starting from the stranding stage, the process of creating grid electricity cables using aluminium wire involves twisting multiple wires together, possibly annealing, wrapping with an insulating material, applying additional layers if needed, winding onto reels, and thorough quality control checks. Each step ensures that the final product is reliable, safe, and capable of efficiently transmitting electricity.