filmov
tv
Tutorial – The limitations of three-axis CNC milling (From 3D model to CNC fabrication, part 1)
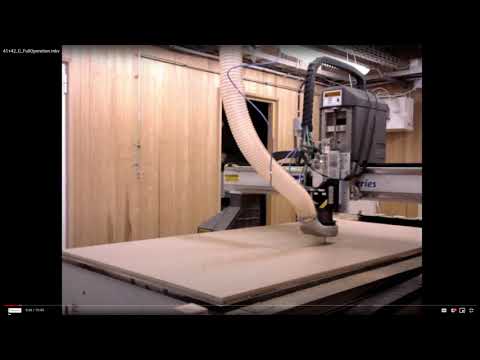
Показать описание
This tutorial introduces the limitations of three-axis CNC milling, in the context of utilizing the CNC router in the KTH Architecture school Workshop.
Timestamps:
0:00 Introduction
0:16 Only perpendicular milling – no overhangs
0:45 Maximum cutting depth
1:16 Minimum radius for concave corners
1:44 Calculating maximum cutting depth
3:09 Outro
Google Drive folder with KTH community resources:
This tutorial is part of a series, "From 3D model to CNC fabrication":
Playlist link:
Part 1: The limitations of three-axis CNC milling
Part 2: Preparing your model in Rhino for CNC milling
Part 3: Obtaining Educational Access to Fusion 360
Part 4: Importing into Fusion 360 and setting up stock
Part 5: Importing a tool library into Fusion 360
Part 6: Authoring a clearance toolpath in Fusion 360
Part 7: Authoring a roughing toolpath in Fusion 360
Part 8: Authoring a finishing toolpath in Fusion 360
Part 9: Post-processing toolpaths in Fusion 360
Part 10: Preparing your physical stock for CNC milling
Part 11: Initializing the CNC machine and setup tools
Part 12: Calibrating tools and defining work origin
Part 13: Executing the toolpaths and cleaning up
Please note that the 10 mm margin between collet and top of stock is not a hard margin, and one has to take into account the topography of the particular model that one mills (a steep model is riskier, in terms of collet collision, than a more moderately elevated one). The advantage of having a 10 mm margin in mind from the start is that the margin might be consciously diminished, should the need arise, while still maintaining a margin between collet and top of surface – if one does not keep such a 10 mm margin in mind, and works from the outset without such a margin, then there is little that can be done to avoid collisions if necessity arises to allow for a deeper cut. For the tool index nr. 10 used as an example here, when used in this tutorial series to mill the model authored by Erik Wingquist, we have adjusted the collet-to-top-of-surface margin to 7 mm, as an example of this not being a rigid, hard margin, but a soft margin, which nevertheless should not approach less than 5 mm (taking in mind whether previous toolpaths have completely eroded the top surface or not, and by how much).
Disclaimer:
This tutorial aims to increase student awareness of the versatility of the digital tools available for use within the context of the architectural education offered by KTH. As such, it might not be generally applicable, but on the other hand, if even one student is helped by it with fulfilling deliverables requirements, the purpose of this tutorial is satisfactorily achieved. There might be inaccuracies in this tutorial video – if you identify any significant one, please tell us in the comments.
Timestamps:
0:00 Introduction
0:16 Only perpendicular milling – no overhangs
0:45 Maximum cutting depth
1:16 Minimum radius for concave corners
1:44 Calculating maximum cutting depth
3:09 Outro
Google Drive folder with KTH community resources:
This tutorial is part of a series, "From 3D model to CNC fabrication":
Playlist link:
Part 1: The limitations of three-axis CNC milling
Part 2: Preparing your model in Rhino for CNC milling
Part 3: Obtaining Educational Access to Fusion 360
Part 4: Importing into Fusion 360 and setting up stock
Part 5: Importing a tool library into Fusion 360
Part 6: Authoring a clearance toolpath in Fusion 360
Part 7: Authoring a roughing toolpath in Fusion 360
Part 8: Authoring a finishing toolpath in Fusion 360
Part 9: Post-processing toolpaths in Fusion 360
Part 10: Preparing your physical stock for CNC milling
Part 11: Initializing the CNC machine and setup tools
Part 12: Calibrating tools and defining work origin
Part 13: Executing the toolpaths and cleaning up
Please note that the 10 mm margin between collet and top of stock is not a hard margin, and one has to take into account the topography of the particular model that one mills (a steep model is riskier, in terms of collet collision, than a more moderately elevated one). The advantage of having a 10 mm margin in mind from the start is that the margin might be consciously diminished, should the need arise, while still maintaining a margin between collet and top of surface – if one does not keep such a 10 mm margin in mind, and works from the outset without such a margin, then there is little that can be done to avoid collisions if necessity arises to allow for a deeper cut. For the tool index nr. 10 used as an example here, when used in this tutorial series to mill the model authored by Erik Wingquist, we have adjusted the collet-to-top-of-surface margin to 7 mm, as an example of this not being a rigid, hard margin, but a soft margin, which nevertheless should not approach less than 5 mm (taking in mind whether previous toolpaths have completely eroded the top surface or not, and by how much).
Disclaimer:
This tutorial aims to increase student awareness of the versatility of the digital tools available for use within the context of the architectural education offered by KTH. As such, it might not be generally applicable, but on the other hand, if even one student is helped by it with fulfilling deliverables requirements, the purpose of this tutorial is satisfactorily achieved. There might be inaccuracies in this tutorial video – if you identify any significant one, please tell us in the comments.