filmov
tv
Complex Mold Split Using SolidWorks
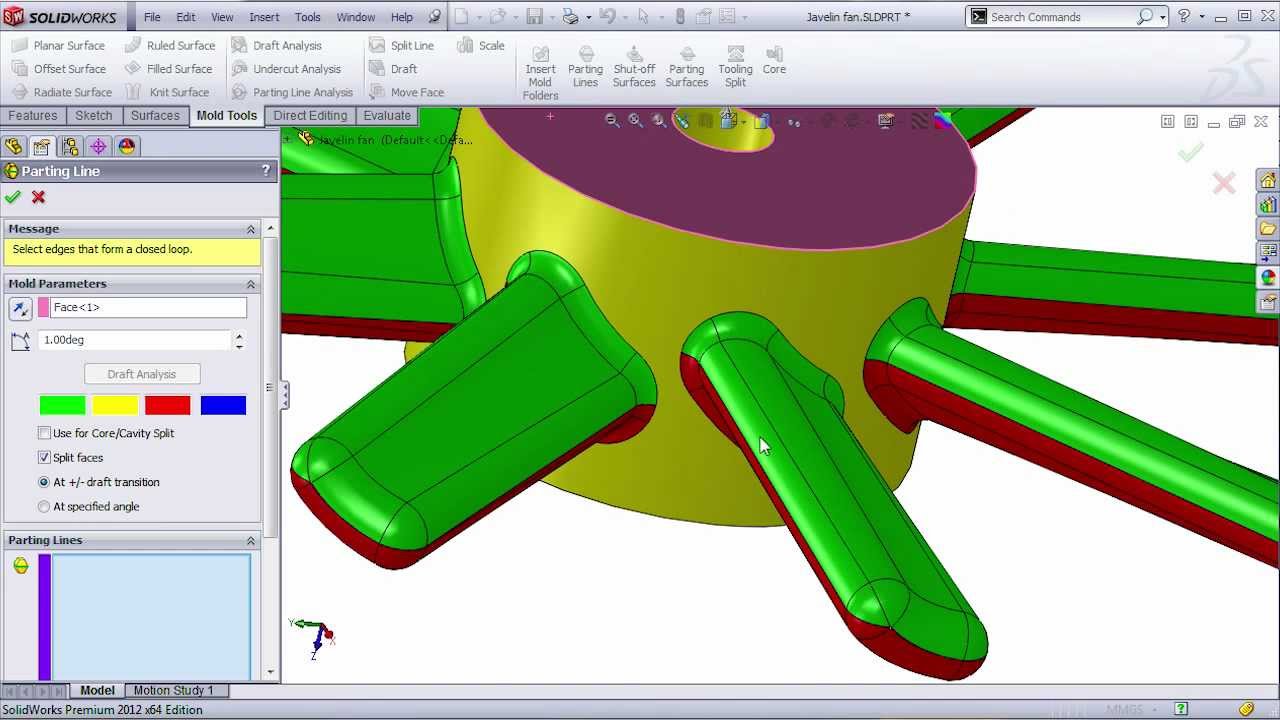
Показать описание
Sometimes, the standard workflow for creating a mold split is going nowhere. This video will show "unorthodox" ways to split the tooling very fast.
As a piece of advice - learn Surfacing if you want to become a Pro.
As a piece of advice - learn Surfacing if you want to become a Pro.
Complex Mold Split Using SolidWorks
Mold Parting Surface
Webinar Archives: Designing with SOLIDWORKS Mold Tools
Mold Design in SOLIDWORKS - Split Core Cavity With Surface - Toys 1/4
09 Tooling Split ( SOLIDWORKS Mold Design Tutorial )
FP1 SolidWorks 2016 Basic Cavity Split Tutorial Part 1
SOLIDWORKS MOLD DESIGN - SPLIT Core Cavity - Elbow 1/4
Tech Tip Tuesday: Mold Tools
SOLIDWORKS Quick Tip - Demo of the Mold Tool
E6 SolidWorks Mold using configurations
SolidWorks Mold Tools - How to make parting line Non Planner with Surface part 1/4
MOLD | How to Create CORE-CAVITY || SOLIDWORKS TUTORIAL
Problem in parting surfaces / in complicated mold / in Solidworks
SolidWorks tutorial: using mold tools to make a split cavity.
Solidworks Tooling Split Mold Tools Tutorial
SOLIDWORKS - Mold Tools Part 2 - Split Line and Parting Line
SolidWorks Mold Design | SolidWork Basket mold Tutorial
Solidworks Parting Line and Parting Surface Mold Tools Tutorial
Basic tutorial on Mold split in #solidworks - Lesson #1
SolidWorks Mold Tooling: How Non-Planar Parting Lines Can Give You the Edge
SolidWorks Mold Tutorial Core and Cavity of Stool
SOLIDWORKS: Perform a Simple Tooling Split
SOLIDWORKS 2011 - Manual Mode for Parting Surfaces
SOLIDWORKS - Mold Tools Tricks Pt. 2: Parting Lines and Surfaces
Комментарии